1 minute read
Flexitallic invests £200,000 in new production technology
Flexitallic, the global leader in static sealing solutions, has expanded its manufacturing capabilities for its innovative Change™ gasket with an investment in new production technology.
The company has invested around £200,000 in state-of-the-art machinery at its facility in Cleckheaton, West Yorkshire, to supplement its existing Change™ gasket manufacturing operation in Texas, United States.
The introduction of the manufacturing equipment will enable Flexitallic to increase production in line with the industry demand for the ChangeTM technology and enable shorter lead-times for Europe and the Eastern Hemisphere.
Change™ has become the most significant development in the gasket and sealing industry in the past five years with more than 50,000 sold into sectors such as Steel, Power, Chemical, Refining, and Pulp and Paper, around the world.
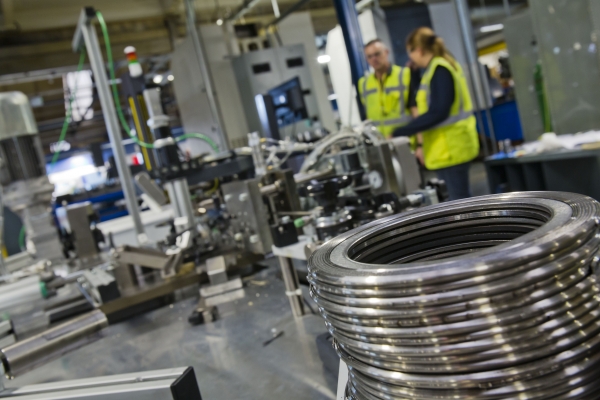
Investment in state-of-the-art machinery / Picture: Flexitallic
Developed by Flexitallic in direct response to customers’ long-term heat exchanger sealing problems, Change™ is a highly-resilient metal-wound gasket, designed to deliver the most dynamic static sealing technology ever.
Manufactured using proprietary equipment, Change™ has a proven track-record showing it outperforms conventional gasket technology in challenging environments, especially in applications with mechanical and thermal cycling conditions.
It has also achieved independent industry accreditation from TALuft for its ability to deliver the tightness of a Kammprofile with the recovery of a Spiral Wound Gasket.
This is achieved through the application of a unique metal spiral profile, which is more advanced than those found in standard gaskets. This profile, combined with a laser welding process, facilitates the construction of a robust and dynamic seal.
Phil Kelshaw, Flexitallic’s Sales Director – Eastern Hemisphere, said: “With demand for Change™ increasing across all markets and industries, the investment in a European manufacturing capability was an essential next step for the company.
“It will enhance existing production expertise at our UK facility and support our ambitions to provide an increasingly responsive service to customers in European, Middle East and Far East markets.”