3 minute read - 25th May 2023
UKBIC to build £36m Flexible Industrialisation Line
The UK Battery Industrialisation Centre (UKBIC), the UK’s national battery manufacturing scale-up facility, has secured £36m in funding for the facility’s new Flexible Industrialisation Line (FIL).
The new line will bridge the gap between UKBIC’s Volume Industrialisation Line (VIL) and existing kilogramme scale demonstrator lines available elsewhere. Construction of the new flexible line is set to get underway in September of this year, with the equipment coming online during 2025.
The new line will provide battery developers with a cost-effective route to market, enabling companies to move from R&D through to large-scale production, without having to take cell development outside of the UK. Once completed, FIL will be owned by UKBIC but operated jointly by UKBIC and WMG to facilitate effective transfer from research into industrialisation.
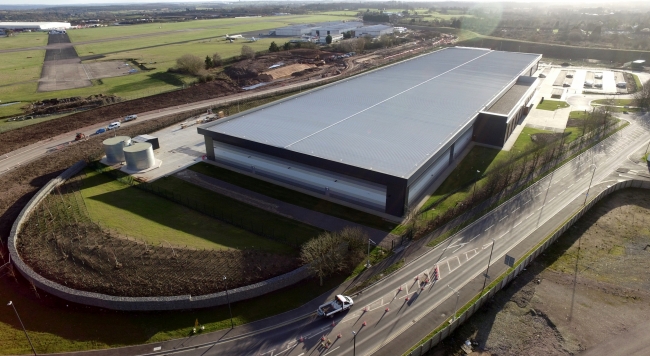
The UK Battery Industrialisation Centre is to build a £36m Flexible Industrialisation Line to support UK-based battery cell development / Picture: UKBIC
Funding for the new line is being provided by UK Research and Innovation, as part of the UK Government’s Faraday Battery Challenge, a £541m investment programme which supports world-class scientific technology development and manufacturing scale-up capability for batteries in the UK.
Since it opened in July 2021, UKBIC has successfully supported 24 advanced scale up and industrialisation battery technology projects across numerous battery developers and end users, supported by its existing facilities and capabilities.
Dr Ahmad Mohsseni, UKBIC’s chief technology officer, said: “The construction of this new facility will be hugely significant for UKBIC and the UK battery industry. Once built, this new Flexible Industrialisation Line, will provide companies with a unique platform to enable them to get a foot on the scale-up ladder, from research & development through to volume manufacturing.
“Companies can find it incredibly difficult to source the volume of advanced materials required for early scale trial and demonstration – the smaller the quantity needed, the better for executing early-stage optimisation cycles and production trials. To date, we have mitigated the amount of material and time required for running our larger scale manufacturing equipment for early customers through developing techniques such as half-width coating, running at slower speeds and half mix batches of slurry, but more is needed to support industry with a truly cost-effective route to commercialisation.”
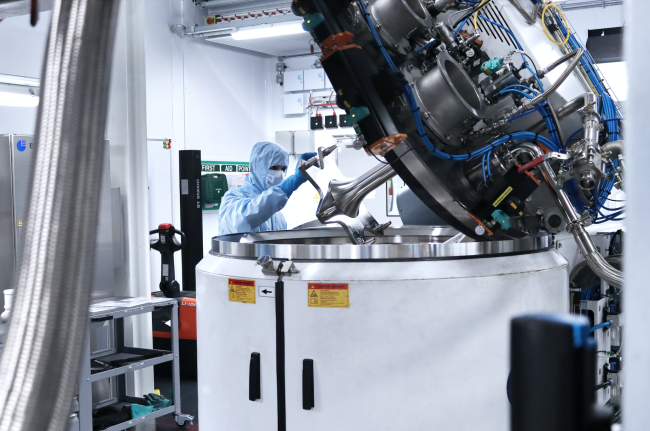
Funding for the new line is being provided by UK Research and Innovation, as part of the UK Government’s Faraday Battery Challenge / Picture: UKBIC
Jeff Pratt, UKBIC’s managing director, added: “The scaling up of battery cells is notoriously difficult, time-intensive, and complex. When technology developers get to the point of trying to attract investors or customers, they are looking for high quality control and industrial standards, which is a key reason for turning to UKBIC. The challenge is that they may have a significant programme of product and process developments to be completed before they can continue. Our specialist high-volume manufacturing equipment is perfect for those organisations in need of representative scale-up, but not necessarily for those organisations at an earlier technology readiness stage of their development. That’s where FIL, once built, will come in.”
Tony Harper, director of the Faraday Battery Challenge, said: “When customers leave laboratories or pilot lines for product development, there is still a huge amount of process iteration required before cells can be successfully scaled at the cost, quality, and performance required for giga-scale production. UKBIC’s existing Volume Industrialisation Line is ideally placed for the later stages of manufacturing process to validate that product can be made in volumes of tens of thousands and above. This is where it becomes cost-effective and representative of an industrial plant run, and therefore a vital part of the commercialisation process. The gap for the UK is in early production quantities, between the low hundreds and low thousands of cells, which is where our new line will come in.”