2 minute read - 11th April 2024
Longcliffe invests £2.4m to boost capacity and sustainability
Long-established family-owned Derbyshire company Longcliffe Quarries is investing £2.4m in two new mills for its calcium carbonates (limestone) operations. This investment in the most up to date technology will enhance the company’s ability to supply the exacting requirements needed of high purity calcium carbonate powder products; and, at the same time, increase the sustainability of its operations.
The high purity of the limestone Longcliffe extracts from its quarries enables the company to produce around 100 products for a huge range of critical industries, from animal feeds and pet foods to grouts, glass and adhesives. This investment will improve the company’s overall operation, helping to secure its future and the 190 jobs it supports.
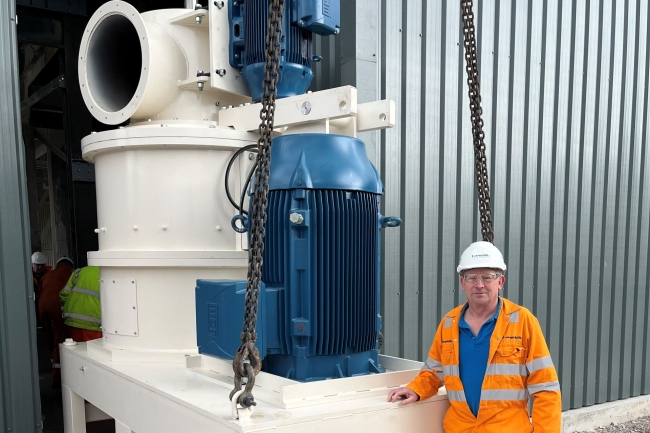
Longcliffe is investing £2.4m to boost capacity and sustainability / Picture: Longcliffe
Longcliffe group managing director, Paul Boustead, said: “This is a substantial investment for Longcliffe. As a supplier of essential high purity calcium carbonate products, we are always reviewing all aspects of our operation and looking to the future to ensure continuous and efficient supply. These two 14-tonne horizontal mills are the latest technology and are being installed in two phases – one in April this year, and one in the autumn. They will deliver many benefits to the environment, our employees, our customers and our business. For the environment they will contribute towards our goal of becoming carbon neutral to the weighbridge by 2030. The mills will decrease the kilowatts of electrical energy we use by over half a million each year; and they will also reduce the amount of material we have to transport within our site.
“One of the drivers for this investment is the change in the British Standard for cement which takes the allowance for replacement of cement with limestone-based extenders from 10% to 20%, so reducing cement’s carbon footprint. Our pure calcium carbonate is also attractive to cement producers as it does not affect the strength of the final concrete. Taking all this into account, this market for our product has grown and we needed to shore up and increase our capacity to produce these materials. These mills will deliver an increase in production capacity of 30 per cent. And for our employees, the project will improve conditions for drivers who will now be loading material into newly covered silos for processing.”
The two new horizontal mills will work alongside one vertical mill, with an older vertical mill being removed from the operation. The new mills have an integral classifier, reducing processing time and saving energy. With the vertical mills, the material has to be classified separately so is more energy intensive. The mill project is also supporting UK manufacture with the components being manufactured all within an hour of Longcliffe’s site. The majority of the machining and assembly is taking place in Uttoxeter.