5 minute read • published in partnership with NoMuda
“A perfect marriage with our manufacturing processes” – How NoMuda VisualFactory enables Carnegie Robotics to continue pushing boundaries
When your solutions perform dangerous tasks like detecting and neutralizing buried explosives, reliability is paramount. By optimizing shop floor operations and improving traceability, NoMuda VisualFactory ensures companies like Carnegie Robotics benefit from increased manufacturing efficiency and adhere to the highest quality standards.
Carnegie Robotics is a global leader in advanced sensors, software, and autonomous platforms for challenging environments, including construction, mining, marine, and defense. Renowned for cutting-edge advancements in robotics technology, the company has worked on projects ranging from unmanned ground vehicles (UGVs) for military applications to autonomous platforms for agricultural and material handling use.
With its products frequently carrying out demanding and dangerous tasks, Carnegie Robotics prioritizes the highest levels of precision, reliability, and quality assurance in its manufacturing processes. Maintaining these high standards amid rising project complexity required making the shift to digital manufacturing, explains Grant Gross, Director of Manufacturing and NPI at Carnegie Robotics.
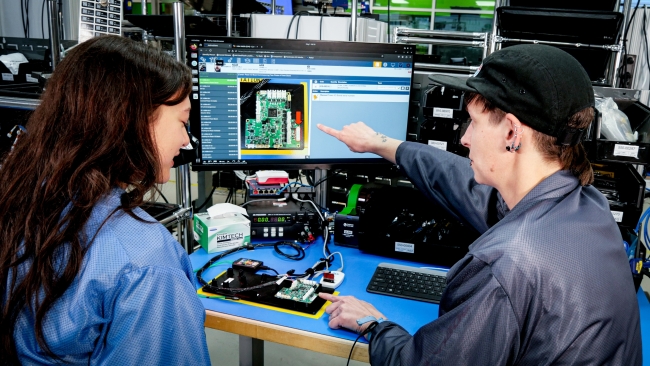
Picture: Carnegie Robotics
“A military project we were involved in saw us building 16 robots, each comprising nearly 5,000 unique components and a total of almost 8,000 parts. Many of these parts required specific torques for their fasteners. We immediately saw the limitations of our traditional work instructions and assembly procedures, prompting us to seek a more advanced solution.”
Carnegie Robotics turned to NoMuda VisualFactory, a leading manufacturing execution system (MES) software platform that helps companies digitize their shop floor operations and improve production efficiency and first-time quality. “VisualFactory solves my three biggest challenges,” says Grant. “It streamlines our build instructions, enhances quality assurance, and drives continuous improvement.”
Intuitive digital work instructions
Before VisualFactory, Carnegie Robotics was using Microsoft Excel to create work instructions for assembly technicians. The process was awkward, time-consuming, and required separate procedure management software to review and approve each set of directions. With operators having to manually write down when each step was completed, the risk of steps being done in the wrong order or skipped entirely was ever-present, meaning additional in-process checks had to be put in place.
“To maintain the level of quality we require, it became incredibly cumbersome and costly to manage that system,” Grant explains. “In that respect, VisualFactory has changed the game.” Using VisualFactory, Carnegie Robotics can now set up digital work instructions that are displayed to assembly technicians via computer screens.
The standardized instructions provide a clear step-by-step guide for completing a specific task, including components, tools, checks, warnings, drawings, and videos. Unlike printed paper or PDFs, VisualFactory’s digital instructions are “dynamic, living documents. We can quickly and easily update them as our manufacturing processes evolve,” Grant says.
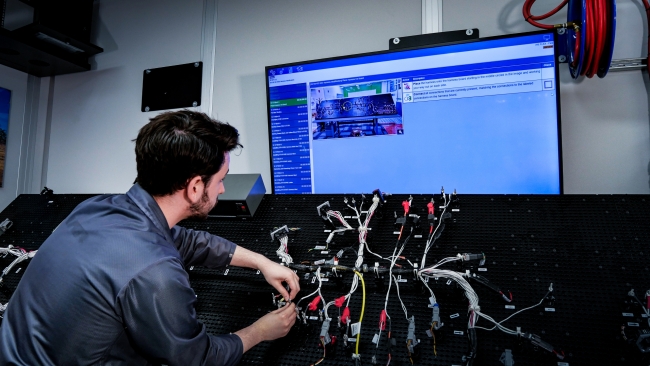
Picture: Carnegie Robotics
Ensuring traceability and compliance
An important aspect of VisualFactory for Carnegie Robotics, in addition to being intuitive and easy to follow, is its ability to simplify traceability and compliance. Instructions are only displayed for the specific task at hand, with the next instruction only shown once the system has verified that the previous step has been completed correctly.
“We are building ever-more complex projects, making it critical that our manufacturing processes are precisely followed. VisualFactory provides 100% assurance that our defined build sequences are being adhered to,” Grant explains. “Our staff are all issued with ID cards which enable them to log into a job via VisualFactory. Tied to each ID is a record of the operations and procedures a worker has been trained to perform. Try to work on a station you’re not qualified for and the system will deny you access.”
“This level of control and visibility is invaluable. It enables us to see exactly who is working on what, at any given time, as well as ensuring every process is carried out by a suitably trained technician.” VisualFactory’s tool tracking feature was another crucial aspect for Carnegie Robotics. Previously, while scheduled reminders to check tools for calibration were in place, there was no mechanism to prevent the use of uncalibrated tools. This too required additional in-process checks, adding further time and complexity to the build process.
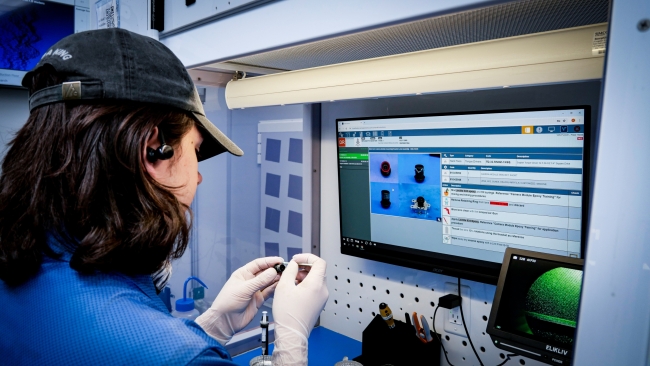
Picture: Carnegie Robotics
Now, VisualFactory requires tools to be scanned before an operation is performed to verify their collaboration against a database. If a tool is found to be out of calibration, it is immediately exchanged, helping ensure Carnegie Robotics meets the high standards of compliance customers expect.
Traceability and compliance are further enhanced through VisualFactory’s ability to create a ‘Digital Birth Certificate’ for each product. The system automatically captures and records every aspect of the manufacturing process, including the steps used, the technician responsible for carrying out each step, when they were completed, relevant build settings, and a full parts list.
This single source of information not only removes the cost and burden of manually recording this information but also provides a powerful repository of real-time insights into factory operations.
Harnessing data for continuous improvement
Using data for more informed decision-making and helping increase manufacturing efficiency is crucial in today’s competitive landscape. VisualFactory records every aspect of the production process, providing real-time updates on production volumes, labor hours, stoppages, cycle times, and rework rates.
“Data runs the world. As an industrial engineer, understanding our build times and costs is essential. This meant physically standing by each assembly station with a stopwatch and manually analyzing all the collected data. VisualFactory streamlines this process for us.
“As soon as a technician logs into the system and starts building, VisualFactory tracks every detail – who, what, where, when, and why. Achieving this level of granularity without a system like VisualFactory is nearly impossible.”
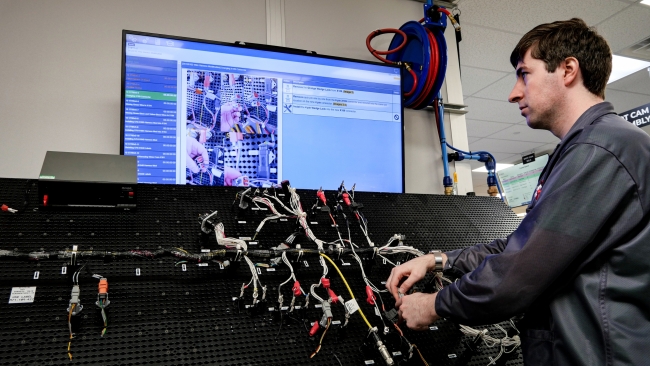
Picture: Carnegie Robotics
Grant describes having access to VisualFactory’s real-time dashboards and management reports marks “a generational leap” for Carnegie Robotics in continuous process improvement. “VisualFactory’s advanced capabilities allow us to make more informed and timely decisions for ongoing manufacturing efficiencies. We can quickly identify and resolve issues, and we have confidence that we are targeting the root cause rather than just addressing surface issues.”
A firm foundation for growth
As a fast-moving, innovation-focused company, Carnegie Robotics requires manufacturing solutions that offer “flexible rigidity.” Having experienced the drawbacks of in-house bespoke software, managers realized the need for a system offering robust functionality out of the box while allowing for customization and modification.
“Our manufacturing processes are unique because we need standardization and well-defined processes but we also have a high degree of product variation that requires flexibility and customization,” Grant explains. “VisualFactory truly offers the advantages of both worlds without any of the drawbacks.”
Reflecting on the partnership with NoMuda, Grant concludes; “It has been an incredibly positive relationship that continues to add value. From the outset, NoMuda VisualFactory has driven tangible improvements in our build processes and broader manufacturing operations. It has enhanced our production efficiency and agility, furthered our goal of a paperless manufacturing floor, and ensured our company is well-positioned for future growth. “Our manufacturing partners have been equally impressed with the results. Indeed, after witnessing VisualFactory in action, several are now looking at adopting it themselves.”