3 minute read - 7th October 2024
Advanced Engineering show to help bridge the gap between design and production
The disconnect between design and production continues to plague many manufacturing projects. Errors and inefficiencies arise when intricate details fail to translate seamlessly from the digital world to the factory floor. Enter, the “digital thread” concept — a single source of truth that links data with manufacturing processes. Simon Farnfield, event director at Advanced Engineering, explores the potential of this technology to streamline communication, eliminate errors and accelerate time-to-market for new products.
As modern design software and advanced production machinery, like production-scale 3D printers, continue to emerge, manufacturers are exploring the limits of what’s possible. According to Make UK and PwC’s 2024 Executive Survey, 71 per cent of firms agree digital tech will drive productivity. Despite this optimism, manufacturers face a glaring problem — a disconnect between designers and production staff.
Converting a well-thought-out concept into a complex product is a delicate process and intricate details can be easily lost when transferred from a digital file to the factory floor. Quality errors emerge when a product’s execution fails to meet the standards set by the initial design. On the other hand, design errors occur when the envisioned product promises more than what current manufacturing capabilities or quality controls can achieve. We often see these mismatches on the factory floor, where rapid innovation quickly overtakes production practicalities.
One way of bridging the design-build gap is early communication. Design engineers and production staff must engage in regular, clear dialogue to avoid misunderstandings that could result in errors and misalignment. Another option is investing in sophisticated technology that allows manufacturers to create a digital record — a single source of truth.
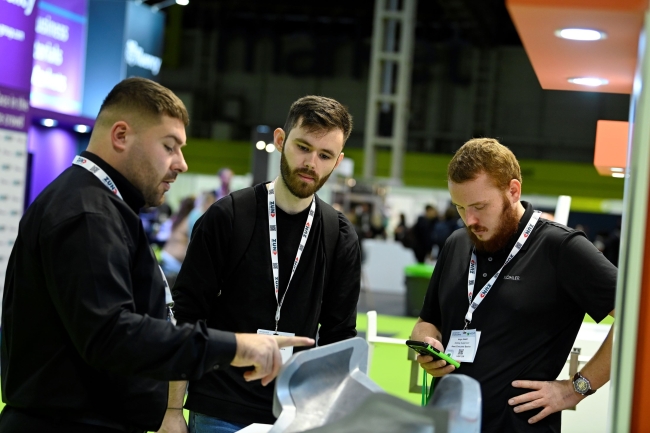
The Advanced Engineering show return to The NEC Birmingham on October 30th and 31st / Picture: Easyfairs
Enter the digital thread
Digital thread is an emerging technology driven by model-based systems engineering (MBSE). It can provide manufacturers with a single source of truth, connecting everything from the initial concept design to manufacture, all the way through to a product’s end of life.
When applied across the production ecosystem, a digital thread can help manufacturers capture every aspect of the product lifecycle and include everyone — from design and manufacturing engineers, to supply chain partners and customers. The benefits of a more connected approach are clear. Streamlined collaboration lowers the risk of miscommunication, and manufacturers can simulate the impact of any part changes in the digital model. Therefore, they can identify and address potential problems before they get to the factory floor, saving time, money and resources on rework.
Using a more digital approach also has efficiency benefits. We’re talking about a system where data capture throughout the product lifecycle is now possible. This creates a regular feedback loop that manufacturers can tap into, so they can refine and revise their products quickly before getting them in front of customers.
Why now?
In the manufacturing world, there is enthusiasm for new technologies such as 3D printing and machine learning, so you’d think building a digital thread would be straightforward. In reality, many manufacturers have yet to fully embrace digital tech. For example, the same Make UK-PwC survey found that only 23 per cent of manufacturers see opportunities in digital technologies.
So, where does this leave the digital thread? Many manufacturers are saying growing costs are their biggest challenge, which could be a reason for digitalisation becoming less of a priority. For example, the last survey is in stark contrast with Make UK’s previous research, which found that 49 per cent of manufacturers beginning to adopt technologies like cloud and machine learning. Yes, digital reluctance is high, but digital threads are more than a gimmick — they could be crucial for cutting costs.
If manufacturers want to improve efficiency, reduce waste and speed up production, they should start by understanding what digital tools are available and how they could benefit on the factory floor. Then, they can think about introducing a digital thread to bring these together — bridging the gap between design and production.
There’s no better way to keep up to date on the latest in digitalisation than by attending Advanced Engineering UK. The event is returning to the NEC, Birmingham, on October 30 and 31, 2024, and you can register for your free ticket by visiting www.advancedengineeringuk.com.