5 minute read • published in partnership with NexSys
Case Study: How Pryor Marking maximised ERP investment and transformed processes with NexSys and SYSPRO
Pryor Marking Technology is a longstanding UK manufacturer, renowned globally for its innovation in industrial marking and traceability solutions. Operating across advanced manufacturing sectors including aerospace, automotive and defence, the company’s goal is clear: to lead the market not just through technology, but through excellence in quality, service, and delivery.
With a rich history spanning more than 175 years, Pryor’s capabilities range from hand tools to cutting-edge laser marking systems. With so much experience, it would be easy to imagine a company could rest on it’s laurels, but Pryor are well aware of the need to keep pace and that is writ large in their approach to ERP – the software that underpins it all.
For more than 20 years, Pryor has relied on SYSPRO to handle its engineer-to-order operations. As Richard Allen, Head of IT, explains, “SYSPRO’s been in place longer than many of our staff, so it’s not just a system; it’s a core part of how we operate.”
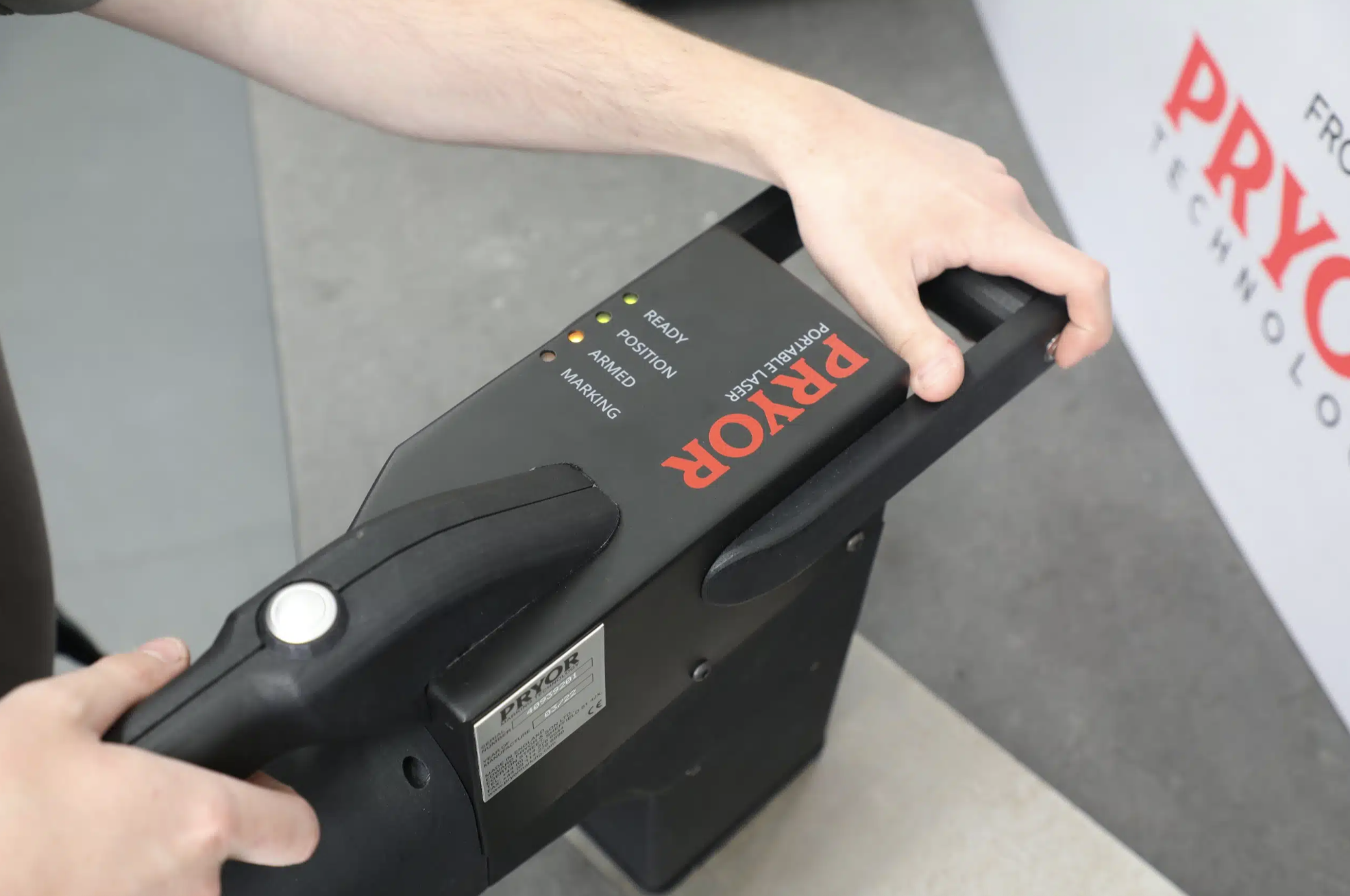
Picture: Pryor Marking Technology
Custom engineering, seamlessly delivered
Pryor’s engineer-to-order projects, especially in the automotive sector, demand seamless data flow from CAD designs to purchasing and production. With SYSPRO and DataSwitch, designers export complete assemblies from SolidWorks directly into SYSPRO, triggering stock code generation and purchase order requirements. This has been pivotal in delivering bespoke Pryor’s flagship robotic marking cells capable of high-speed marking with built-in redundancy.
With a small IT team, Pryor has maximised its ERP investment through close collaboration with NexSys, adapting the platform over time rather than replacing it.
Because the solution evolves with us, we’ve never felt the need to look elsewhere,” Allen adds. That trust has paid off through years of consistent support and system improvements and upgrades that reflect the changing shape of the business.
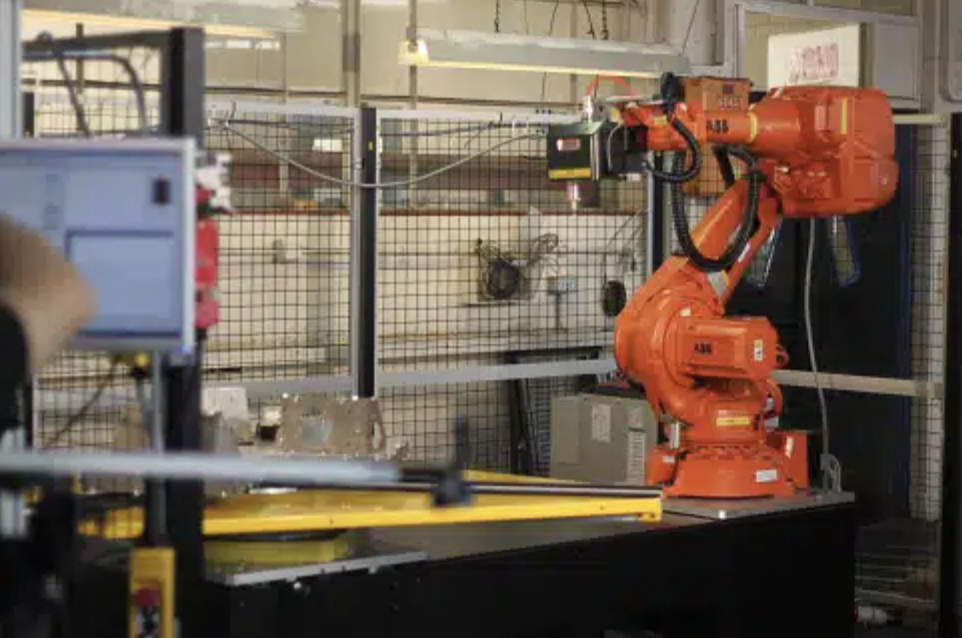
Picture: Pryor Marking Technology
A measured upgrade: migrating to SYSPRO 8
The largest project Pryor has undertaken with NexSys was the upgrade to SYSPRO 8, completed in April 2023. Aware of just how core SYSPRO is to the business, Allen took the view that this wasn’t just an upgrade, but a clear opportunity for business improvement.
As such a carefully phased approach was adopted. The IT team prioritised early admin training, followed by end user training, which then facilitated two months of user acceptance testing (UAT), allowing teams to explore the new system in real-time without disrupting daily operations.
As Allen puts it, “We sat down with users in every role and looked at how they used the system and simply asked the question ‘how could we make it better?’.”
This method ensured that a user group from each area of the business could test live scenarios in a safe environment, building familiarity and uncovering opportunities for customisation. The feedback led to better internal documentation, enhanced reporting, more intuitive dashboards, and improved consistency of approach and user experience across modules.
Real-world results – accuracy and time saving
A key component of the digital infrastructure is DataSwitch which integrates Pryor’s SYSPRO instance with its ecommerce site, CAD software, and operations in the US. The result has been a significant reduction in manual input and near-total elimination of data entry errors.
For example, when the US branch submits a restocking request, DataSwitch automatically generates a purchase order and corresponding UK sales order, with no requirement for duplication and correspondingly no errors.
Allen admits that data entry mistakes on large branch transfers would sometimes occur. “A restocking order for our US facility might contain thousands of line items. If that’s being input by hand, errors are bound to creep in. DataSwitch has massively sped up the process and it gives us real confidence in automating our transactions and business processes.
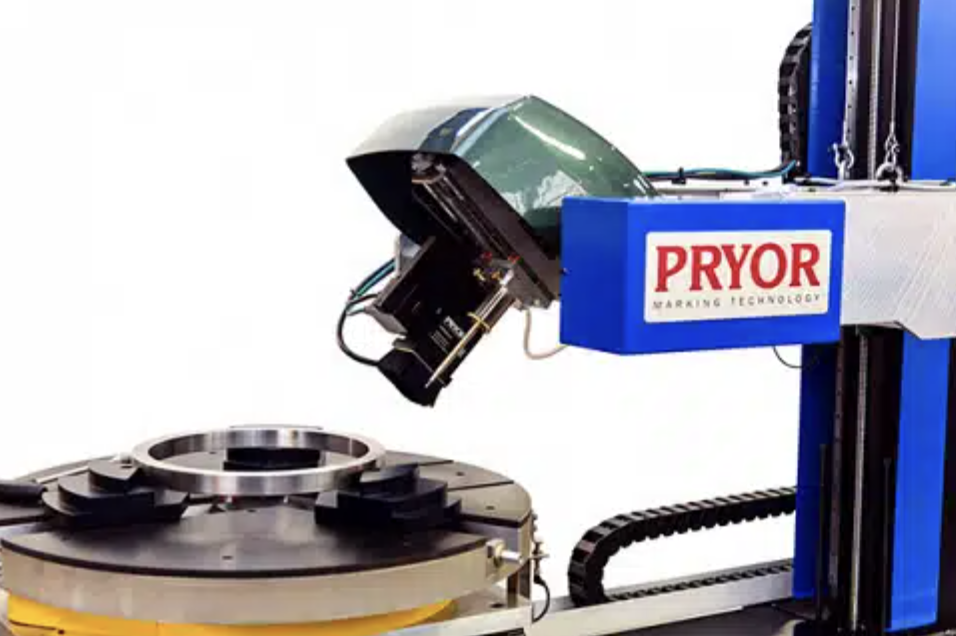
Picture: Pryor Marking Technology
Culture of continuous improvement
Post-upgrade, the company launched an internal SYSPRO resource portal, featuring onboarding documents and a feedback loop for user-requested changes. “We wanted people to take ownership,” says Allen. “That two-way conversation is driving a more consistent and efficient use of the system.”
The move to SYSPRO 8 also created an opportunity to formalise training and standardise procedures. By engaging staff at every level of the business, Pryor has not only improved operational consistency but also fostered a sense of ownership among users. “It’s about empowering people,” Allen says. “We no longer have different people doing the same task in slightly different ways.”
With the ongoing development of custom dashboards, tailored forms, and intuitive reporting now standard, the company has also seen a large drop in requests for bespoke reports and data analysis. Coupled with the use of Power BI to visualise SYSPRO data, this has opened new doors for analytical insight, helping end users to find the information they need quickly and easily themselves and managers to make better decisions across procurement, production and finance.
Building the future
Looking ahead, Pryor’s upcoming relocation after 70 years at its current site is viewed as a catalyst for further modernisation. “It’s a clean slate to rethink shop floor layout, lean processes and equipment,” says Allen. With SYSPRO as the digital backbone, Pryor is well-positioned to embed automation and enhance operational flow.
Power BI reporting, layered on SYSPRO’s SQL backend, is already providing deeper insights to inform this transition. “It’s all about using data to drive better decisions,” Allen adds. “SYSPRO gives us that single source of truth across the entire business.”
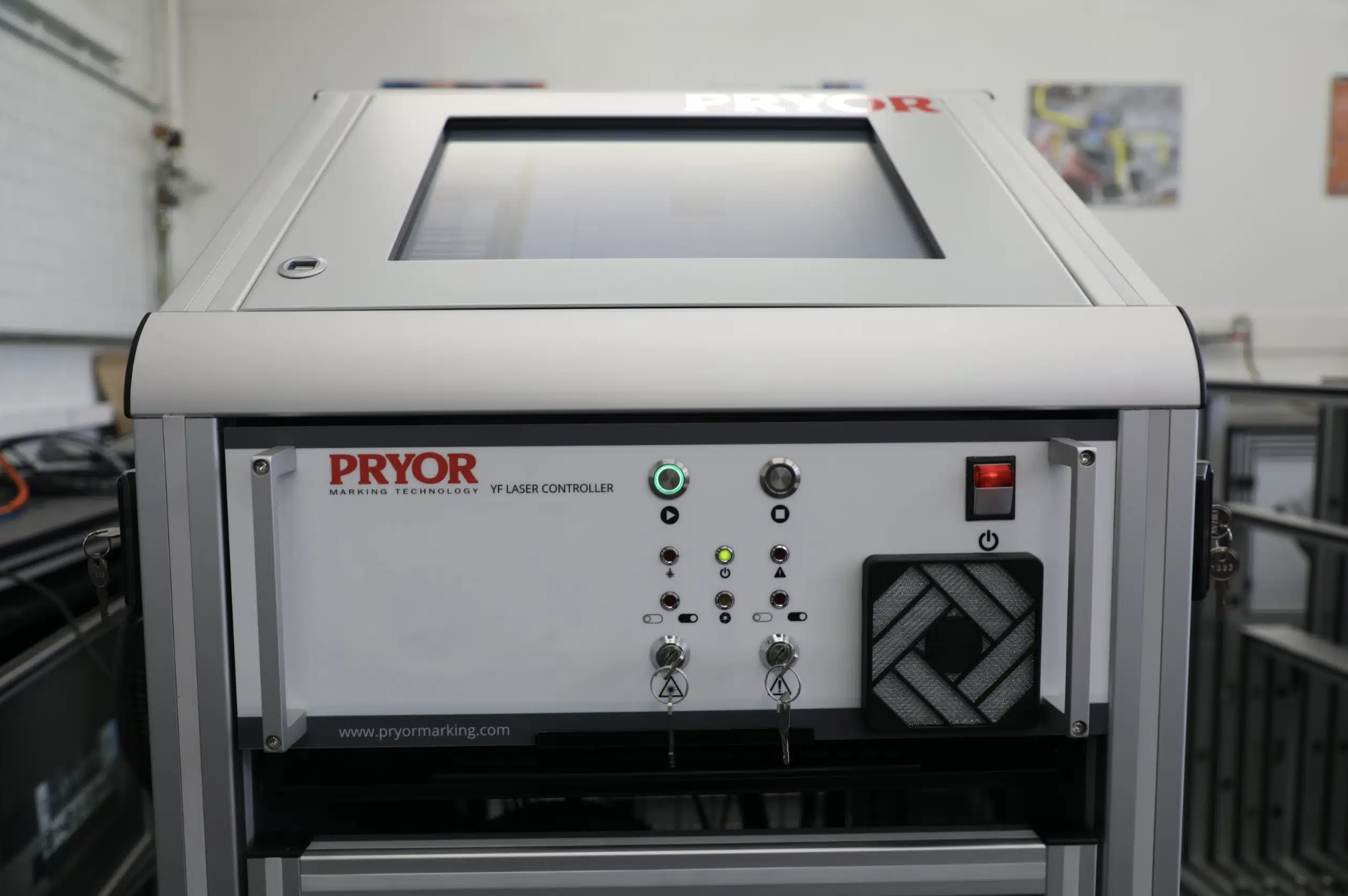
Picture: Pryor Marking Technology
Trusted partnership
NexSys has been integral to Pryor’s ERP journey. With a knowledgeable, long-standing support team and a proactive approach to client engagement, NexSys continues to help Pryor adapt and thrive. “They know our business inside and out,” Allen says. “They’ve helped us tailor SYSPRO to fit our processes, not the other way around.”
Would Pryor recommend SYSPRO and NexSys? “Absolutely,” says Allen. “Especially for manufacturers with complex workflows like ours. It’s modular, flexible, and incredibly well supported.”