4 minute read • published in partnership with KUKA
Case Study: The automation helping one manufacturer see a 2.5x productivity gain
When science and technology company Merck Millipore, based in County Cork, Ireland, recognised the need to move from a manual operation of inserting O-rings into medical sample plates, it selected KUKA Platinum Partner DesignPro to design an automated system that would boost quality and productivity.
Ireland’s life sciences sector has become a big player in the country’s industrial landscape, attracting brands from all over the world, including Germany’s Merck. Merck Millipore’s site in Tullagreen, Carrigtwohill, Co Cork, has been in operation for over 30 years and employs around 850 people. It is an important employer in southern Ireland and a market leader in the sector.
“We have three main product areas on this site. We manufacture filtration membranes, medical devices with the filtration membrane in place and chromatography media” says John Hughes, Senior Manufacturing Engineer, Pilot Operations. “Our products are used in the research, development, and manufacture of biotechnological and pharmaceutical drug therapies globally, as well as in research and application laboratories. ”
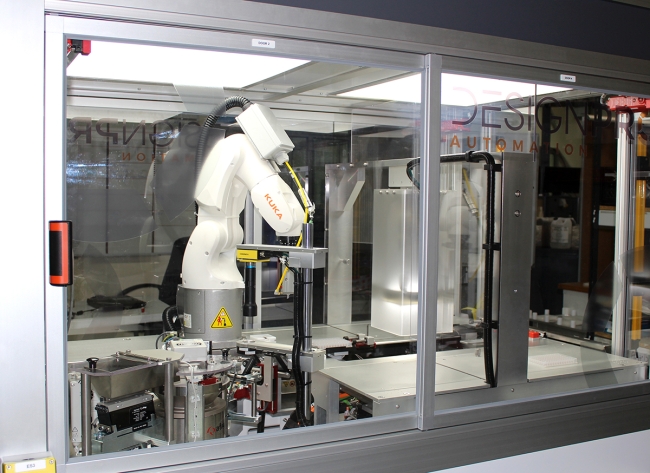
Picture: DesignPro Automation
The process that Merck Millipore sought to improve was the manufacture of its multi-well filtration plates. They are typically used to filtrate fluid samples for research and application testing. The user may fill the wells utilising a multi-channel pipette to optimise test times.
Time-consuming, manual operation
Each filtration plate l has a pre-defined number of membrane coupons and silicone O-rings inserted. The process required a very high need for precision given the stack-up tolerances in question. The o-rings are slightly oversize, in order to make a perfect seal, and will subsequently be bonded to the membrane.
Merck Millipore experienced a high degree of variability throughout the manufacturing process when it operated a manual system. Some operators utilised different instruments and methodologies the process itself was quite slow and cumbersome which the Operations team found difficult optimise. Production throughput under the manual system was not meeting our capacity requirements. With rising demand for testing equipment – which would accelerate with the emergence of the Covid-19 pandemic – higher output was recognised as a priority.
“Our multi-well filtration plates endured a high-degree of variability on a continuous basis so we had to look at alternative technologies for creating integral plates,” John Hughes explains. “We worked closely with our R&D team based in the US to develop a new system that would meet both our manufacturing requirements and those of our customers. We collaborate closely with our colleagues in the US, through the product development phase ensuring our customer requirements are prioritised as well as Design for Manufacturing (DFM) for potential automation equipment builds. On collaborating with the KUKA Platinum Partner, John says “We have worked with DesignPro before and, after a rigorous selection process which included many vendors, we engaged them to design and build a piece of equipment that would automatically insert the silicone O-rings into the multi-well plates.”
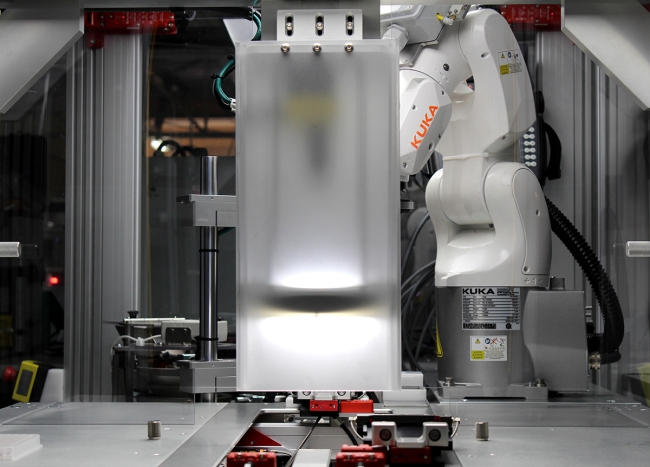
Picture: DesignPro Automation
DesignPro Automation is headquartered in Rathkeale, Co Limerick, which is about 100km (63 miles) from Cork. Patrick Downes, DesignPro’s Business Development and Innovation Manager, takes up the story.
Analysis: quality and productivity
“O-rings can be incorrectly placed or aligned; there was always the chance of a well being missed; and the process of manual handling could cause splits and material failures. As the O-ring was inserted, a rolling action could lead to misplacement,” Patrick explains.
The membrane was very easily damaged during the process and this could lead to defects, or they could have been placed in the wrong orientation. There were also differences between the top and bottom of the well.
“There were a lot of challenges,” Patrick continues. “We offered proof of concept at the start. We used equipment we already had in our facility and set up a vision system to see into the well – which is quite deep – to see the entire membrane and check the accuracy to one-tenth of a millimetre. We took a few images and proved that the system could pick up defects and orientation on the membrane, before the O-ring was inserted, and thus verify quality.”
The development phase in the automation also covered visual checking of the O-rings themselves. Once that had been confirmed the cell could be designed and tested.
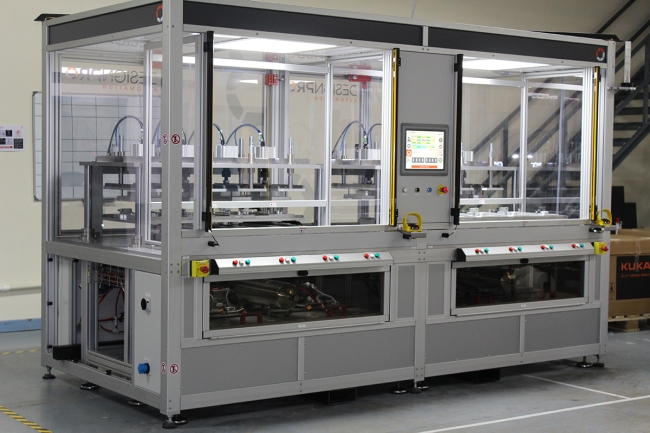
Picture: DesignPro Automation
Solution: KUKA KR3, automated placement and inspection
A KUKA KR3 6-axis robot was selected to place the O-rings, with servo drives to ensure positional accuracy, with 100% inspection by a Cognex vision system. The robot cell has enabled Merck Millipore to transform its output significantly..
“The selection of supplier, development FAT (factory acceptance test) and installation took a year in total,” says John Hughes. “What we have now is an automated cell that has 2.5X the throughput with 100% automated visual inspection to ensure all finished goods that are shipped to customers meet their high quality standards. Our overall quality and productivity has been enormously improved.”