6 minute read • published in partnership with PP Control & Automation
Exclusive: National insurance hikes spurn a new burden on manufacturing’s resilience
Tony Hague, CEO of PP Control and Automation (PP C&A) believes the implications of the Autumn Budget’s NIC hikes will put a burden on a thinning manufacturing resilience after years of global disruptions. But he exclusively tells Zenoot that it could also be a trigger for something long overdue – accelerated adoption of automation and a renewed focus on analysing core vs non-core competencies.
In the wake of the UK Government’s budget announcement, manufacturers are carefully evaluating the potential impacts of the National Insurance contributions (NICs) changes. Chancellor Rachel Reeves announced a £25 billion annual rise in employers’ NICs, a move that has been met with apprehension from pretty much every industry leader across the country.
These adjustments, whilst aimed at supporting broader economic goals, present significant challenges for manufacturers already grappling with high operational expenses and skill shortages. It feels somewhat disheartening after a clear lack of support in our industry from the previous government, to now have to consider navigating big NIC hikes imposed by a new one. As employment costs increase, driven in large part by these NIC hikes, businesses must pivot to strategies that balance their labour force needs with mitigating escalating costs.
Our sector is highly sensitive to changes in employment costs, given its reliance on a diverse, skilled workforce. NICs, representing a significant portion of employers’ expenses, directly impact a manufacturer’s operational expenditure (OpEx). With the recent budget, the pressure to reevaluate staffing costs becomes urgent. The NIC rise could particularly strain small and medium-sized manufacturers, whose margins are already squeezed by inflationary pressures on materials and energy.
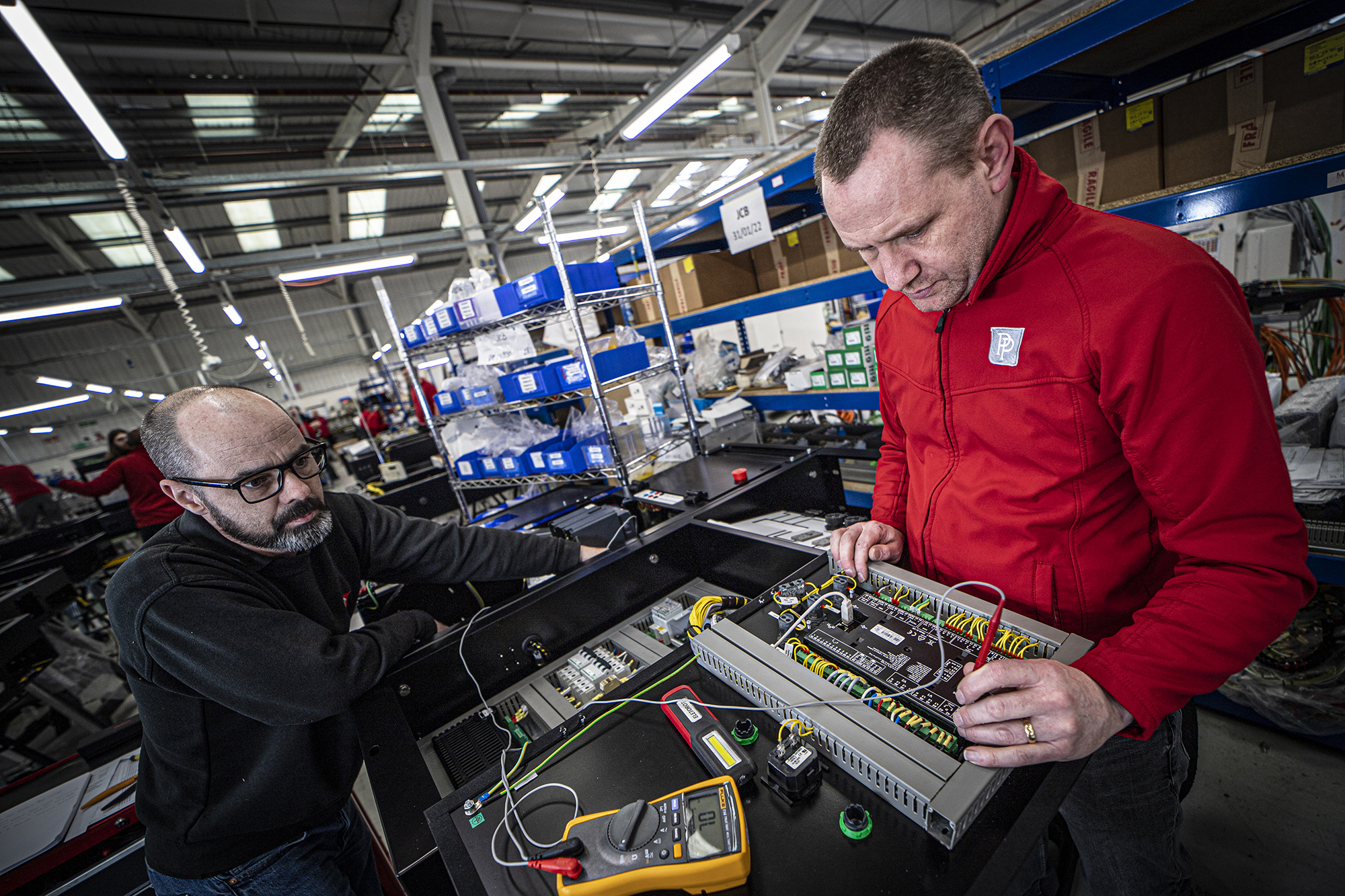
Picture: PP Control and Automation
When viewed from a longer-term perspective, the costs associated with traditional employment models (e.g., payroll taxes, pensions, training, and now higher NICs) can drive manufacturers to seek alternative approaches. Many firms are realising the value in strategies that not only reduce reliance on direct employment but also offer flexibility in operational costs – a need that automation and indeed, outsourcing, can effectively address.
For many OEMs, adopting automation and strategically outsourcing engineering and production capabilities will offer a path that not only alleviates immediate financial pressures but also builds a foundation for sustainable growth.
Is this actually the catalyst we need?
The UK’s position in automation and robotics adoption seriously lags behind nations such as Japan, South Korea, and Germany, which have long been leaders in integrating robotics into their manufacturing and service industries. In 2023, we ranked relatively low in terms of robot density per worker compared to these frontrunners.
Reasons for slower adoption in the UK are multifaceted, involving issues like underinvestment in manufacturing, a service-dominated economy, and a shortage of skilled workers trained in robotics. Additionally, there is a tendency for businesses to approach automation cautiously due to concerns about short-term costs and the potential impact on the workforce.
The risk of falling further behind in this growing field is significant but the budget announcements might inadvertently be a catalyst for accelerating our adoption of these technologies. Even without this influence, we should be thinking about adopting automation more strategically – as other nations continue to advance, the UK risks losing competitiveness. That is especially true in high-tech manufacturing and export-driven markets.
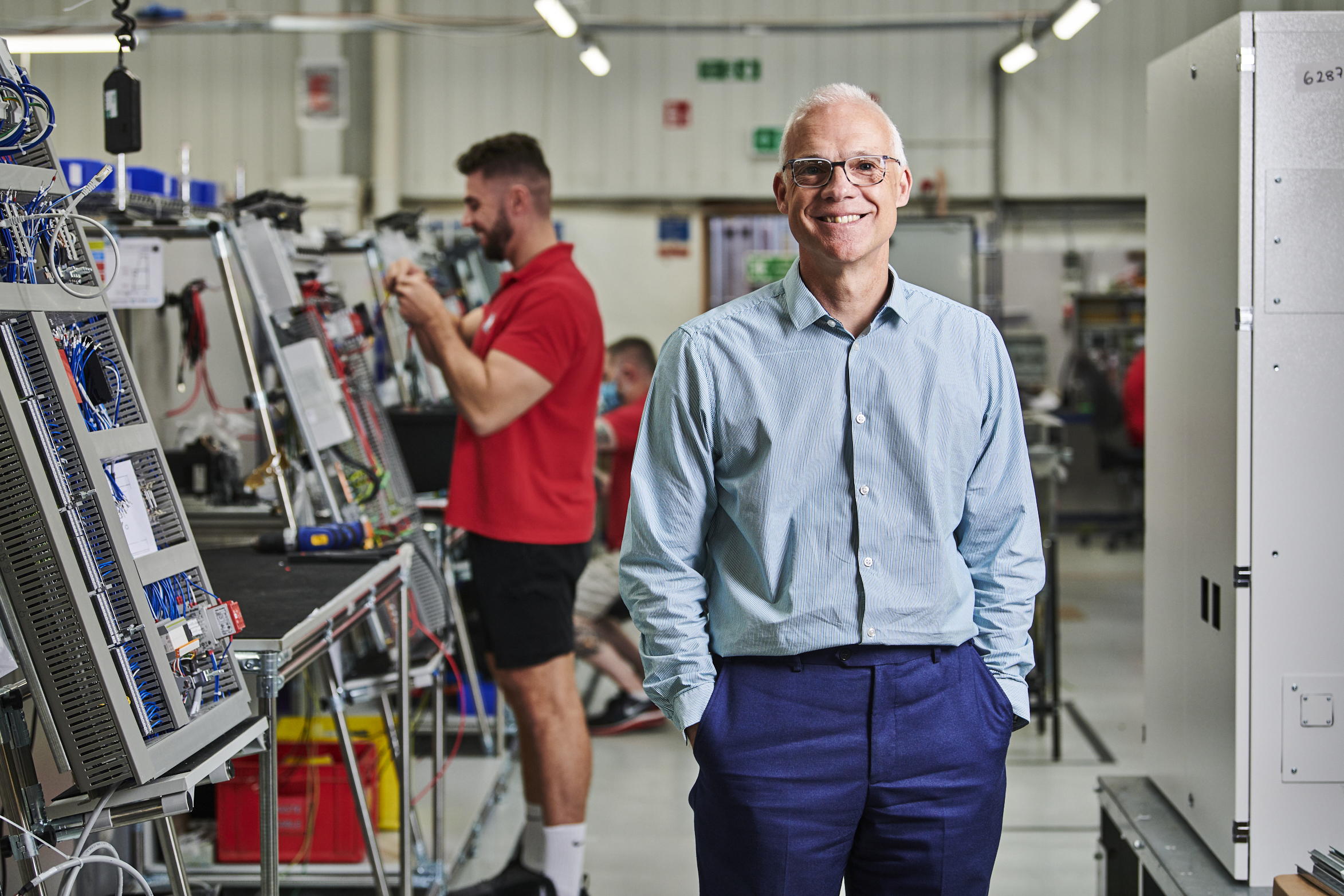
Picture: PP Control and Automation
Reducing dependency on high-cost labour
Automation is often viewed through the lens of enhancing productivity, but its financial benefits go far beyond efficiency gains. For manufacturers burdened by rising labour costs, it can actually mitigate the impact by reducing dependency on human labour. Automating repetitive, high-labour tasks can lead to substantial savings, including NICs, wages, and training investments.
Four key factors come to mind in light of the budget announcements: lower long-term OpEx, consistency and efficiency, scalability and flexibility, and resilience to workforce gaps.
1 – Automation systems typically require an initial capital investment, but they drastically reduce ongoing employment costs, turning labour-intensive processes into manageable, predictable expenses.
2 – Machines offer consistent performance with minimal error, contributing to higher product quality and fewer costs associated with rework or quality control.
3 – As demand fluctuates, automated systems can be adjusted with minimal additional cost, whereas increasing or decreasing a human workforce involves substantial costs and logistical challenges.
4 – Automation reduces dependency on hiring for hard-to-fill roles, a challenge intensified by the UK’s current skills gap in manufacturing.
Automation technologies, including robotics, AI-driven inspection systems, and autonomous logistics solutions, empower manufacturers to streamline operations without inflating employment costs. For example, robotic process automation (RPA) in production lines can take over repetitive tasks, freeing up employees to focus on roles that generate higher value for the business.
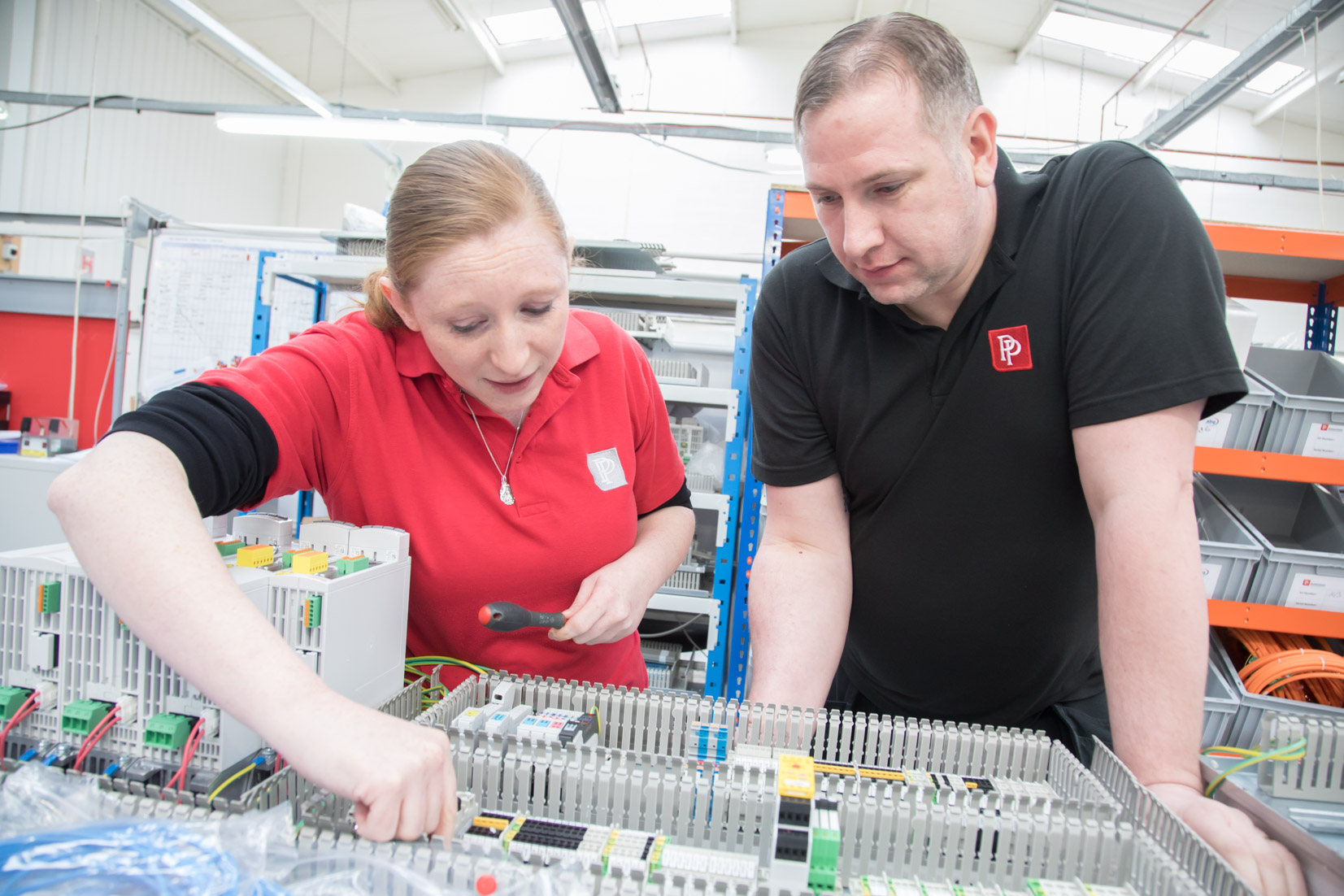
Picture: PP Control and Automation
Transforming fixed costs into flexible expenditures
In addition to automation, outsourcing engineering and production capabilities offers manufacturers another potent tool to mitigate the effects of NIC changes. After all, automation won’t be the answer to every production or worker requirement.
Outsourcing shifts certain fixed costs associated with in-house capabilities into variable, on-demand costs, allowing manufacturers to align expenses with operational needs. This transition is particularly valuable when NIC increases make the cost of ownership for employees and assets prohibitive.
Again, I’m going to stick with four key factors here: cost flexibility and OpEx reduction, access to specialised expertise, reduced capital expenditure, and enhanced focus on core competencies.
1 – Outsourcing specific engineering and production tasks allows manufacturers to scale expenses directly with demand, eliminating the burden of maintaining full-time employees for capabilities that may only be periodically required.
2 – Outsourcing provides manufacturers with access to a specialised talent pool and advanced technologies that may be expensive to develop in-house. This is crucial for specialised skills or capabilities, such as automation, complex engineering, or effective supply chain management, where talent shortages are evident in the UK.
3 – By outsourcing certain functions, manufacturers can avoid costly investments in infrastructure and equipment, further reducing the financial strain of fixed costs.
4 – Outsourcing allows manufacturers to focus their internal resources on strategic initiatives and high-value activities, improving overall business performance.
For example, rather than investing in an in-house team for every phase of production, manufacturers might contract with outsourcing partners for supply chain management, and engineering and production requirements from NPI to final assembly. This enables the company to adapt more fluidly to changes in demand or supply chain disruptions, as outsourcing partners often have broader resources and networks to manage volatility.
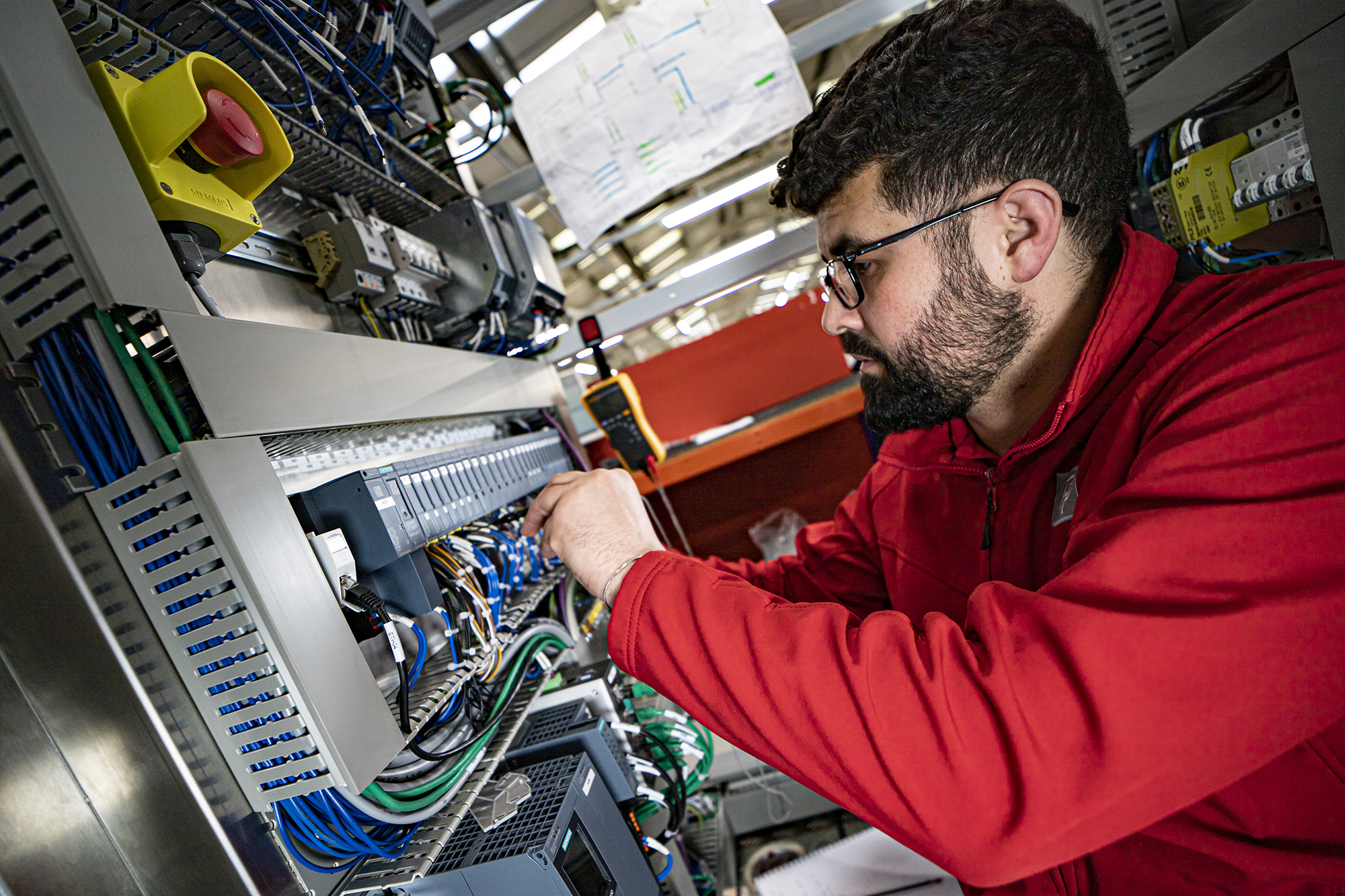
Picture: PP Control and Automation
For manufacturers considering automation and/or outsourcing, several factors should guide the decision-making process.
Evaluating which processes are critical to competitive advantage and which can be automated or outsourced without compromising quality or brand value is the first consideration. You’ll then be faced with a decision – who do we partner with?
Select businesses that align with your strategic goals, ensuring quality standards, compliance with regulatory requirements, and the ability to scale alongside your growth trajectory. Finally, conduct a thorough cost-benefit analysis, considering not only the initial costs of automation or outsourcing, but also the long-term financial and operational benefits.
Every now and again, something comes along and redirects us
The NIC adjustments in the UK Government’s autumn budget underscore the importance of adaptive strategies for manufacturers facing higher employment costs. By adopting automation and/or exploring outsourcing opportunities, manufacturers can alleviate financial pressures whilst positioning themselves for resilience in an evolving economic landscape.
We see large-scale shifts in strategies every now and again, and they’re usually driven by factors previously unseen and direct us towards things we have historically been resistant to. Teachings from the pandemic or the 2008 financial crisis can offer lots of insights – Iceland being one.
For decades, Iceland’s economy was heavily dependent on fishing. The idea of expanding tourism was viewed with scepticism, as many Icelanders preferred preserving their natural landscapes from foreign influence. The 2008 financial crisis hit the country especially hard, leading to a severe banking collapse.
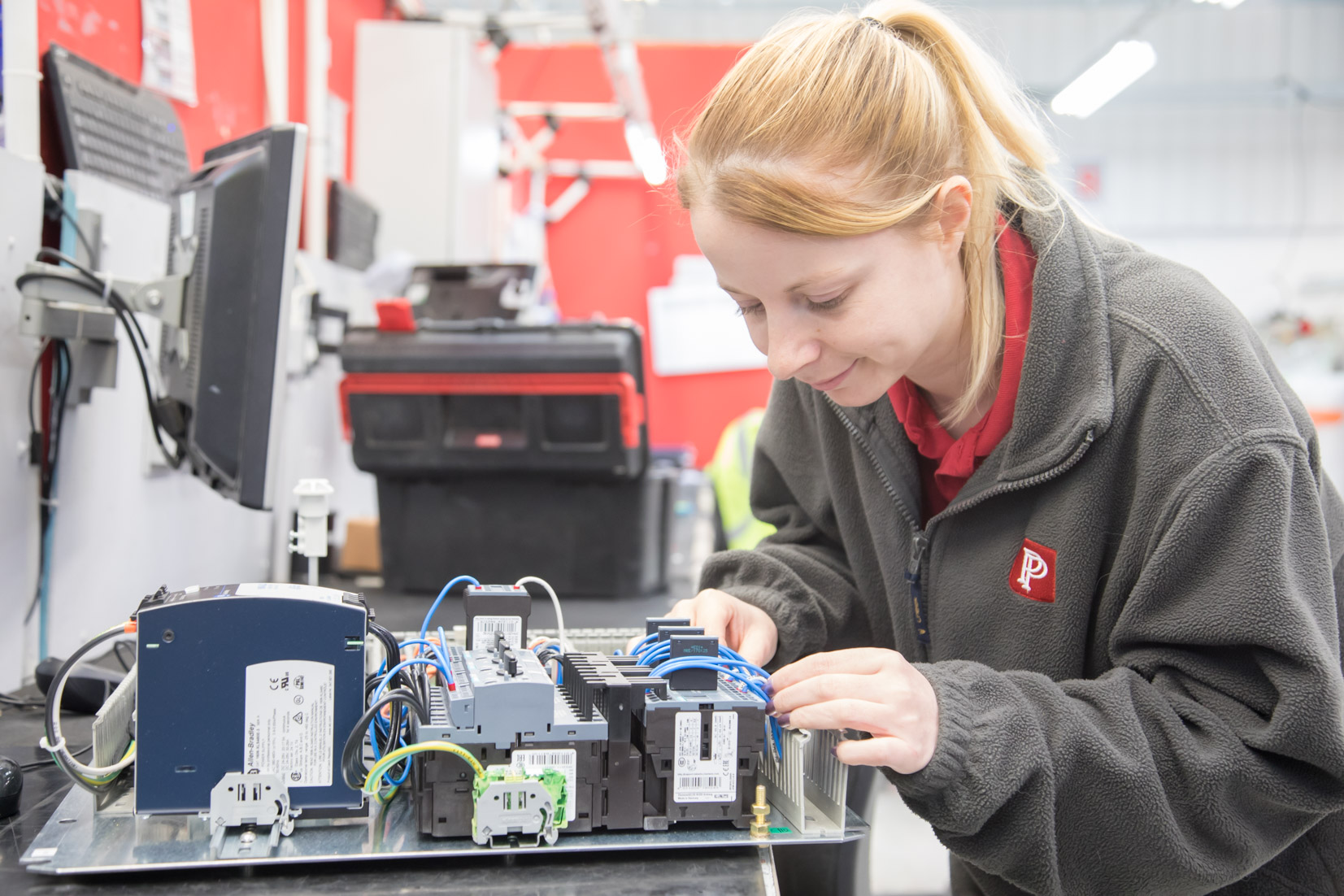
Picture: PP Control and Automation
With traditional sectors faltering, it turned to tourism as an economic saviour. Iceland became a top travel destination, and tourism has since become a pillar of its economy. This shift helped it recover financially and raised international awareness of its culture and natural beauty. This example serves as a powerful analogy for reinventing a legacy industry in the face of financial hardship.
The strategic shifts I believe will now play out enable manufacturers to transform traditionally rigid cost structures into agile frameworks, allowing them to respond effectively to both current challenges and future demands. As the manufacturing sector embraces innovation and rethinks strategies, it will not only overcome the immediate impacts of the NIC increase but also pave the way for sustainable growth in a competitive, high-cost environment.
It might be time to be more Iceland!