4 minute read • published in partnership with igus
Feature: Red Sea crisis exposes UK industry’s flaws, prompting new solutions
Persistent inflation and prolonged delays to imports are having a negative effect on UK manufacturing that relies on global supply chains. The Red Sea shipping crisis is hurting UK businesses now more than ever – is it time for a rethink of long-term supply networks? igus looks at some of the issues and how it is helping manufacturers address the challenges.
Attacks by Houthis rebels on commercial shipping in the Red Sea, causing the rerouting of many carriers via the Cape of Good Hope and long delays, are heavily impacting UK plc. Container freight rates have risen sharply since the crisis began. As the manufacturing sector grapples with this latest geopolitical disruption, the impact on production continues and is prompting ideas to secure supply lines in the future.
Navigating troubled waters
Houthi rebels, allegedly supported by Iran, have regularly attacked commercial ships in response to Israel’s actions in Gaza. On 6th March, three crew members of a ship were killed in an attack off southern Yemen – the first recorded deaths of attacks on commercial shipping.
The result: A logistical fait accompli forcing most shipping companies to reroute freight via South Africa, adding weeks to delivery schedules1. Raw materials, components, and finished goods— that hitherto flowed smoothly through the Suez Canal—now cost more and take far longer to arrive in Europe and the UK. As well as the mounting shipping costs, consider the additional carbon footprint. A ship travelling from Shanghai to New York adds over 2,000 nautical miles by routing via the Cape of Good Hope2.
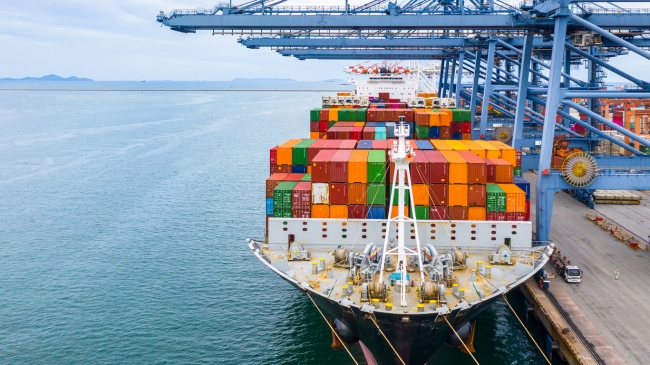
Picture: Getty/iStock
Supply chain disruptions
Companies globally are feeling the effects, and the monthly S&P Global Manufacturing PMI shows manufacturing production was down up to January, There were improvements in the PMI in January – the decline in new orders was the smallest recorded in recent months3, and a similar story for export orders, as this declining story began to turn3. S&P believes manufacturers are adjusting and the impact on prices has so far been weaker than seen during the covid pandemic.
Despite this January rally, this is an unhealthy picture overall. February’s S&P PMI showed production declined, as new orders fell4. Several manufacturers noted that they faced the difficult choice between accepting delays from re-routed shipping or facing the prospect of paying higher prices to source from closer to home. These disruptions have a knock-on effect on production schedules, exacerbating inflationary pressures. At a time when both domestic and overseas demand remains weak, factories are caught in this storm of uncertainty.
And it’s not only supply issues causing concern. Following reports of the Rubymar UK-owned cargo ship being sunk in recent weeks, the spilling of oil and fertilizer in the Red Sea has raised concerns about the environmental impact of this and other attacks. It is reported that over 21,000 tons of fertilizer is now sitting on the ocean floor making, with a 30-km oil slick, an environmental disaster5.
Alleviating stock issues
Amid the gloom, what can be done? igus offers a glimmer of light. “We have always worked hard to ensure our UK stock levels remain high,” says Matthew Aldridge, managing director of igus in Northampton, “and now more than ever high stock levels are crucial to keep production running. We are holding greater stock than ever before, from plain bearings and linear rails, to energy chains and cables, to try and alleviate the supply chain stresses that many UK manufacturers are suffering from.”
One solution for constrained supplies: igus’s in-house readycable production line is today custom-building and testing more readycables than ever, alongside all the other products being built and shipped every day. Will this disruption herald a new age of “make to stock”, shunned for years in favour of “make to order”?
Charting a better course ahead
As the Red Sea crisis continues, factories in the UK must adapt. Some have sought alternative, more local suppliers, albeit at higher costs, but higher prices become irrelevant next to the production downtime costs of having no parts. Other firms are recalibrating inventory strategies, some are turning to predictive maintenance; but more than anything, customers want reliability.
With several online tools to help specify applications, igus can help its customers get the best products for their application, with a reliable life cycle for every product.
The challenges will persist. The Houthi attacks have cast a shadow over the UK production landscape, and companies must navigate these troubled waters with resilience, ingenuity and hope. It will be fascinating to see if these trends accelerate the reshoring of some manufacturing and boost the case for more sovereign capability in area like semiconductor manufacturing.