5 minute read • published in partnership with K3 Syspro
How technology can help reduce the environmental impact of manufacturing
When focusing on reducing waste, using energy more efficiently and creating a greener supply chain, the manufacturing sector can use technology to reduce its environmental impact. This too can lead to significant productivity improvements. K3 Syspro takes a look at the opportunities available.
Awareness of the impact of climate change and human impact on the planet is at an all-time high. This has largely been driven by media coverage through programmes such as Blue Planet II which highlighted the devastating effects of plastic pollution; the global youth climate strikes, inspired and spearheaded by Swedish Nobel Peace Prize nominee 16-year-old Greta Thunberg; and the large protests of civil disobedience by the activist group Extinction Rebellion across cities in the UK and globally.
Politicians in the UK across parties have met with Thunberg and Extinction Rebellion members to discuss a more active and ambitious approach to decarbonising the economy and achieving net zero carbon emissions by 2025 – 25 years earlier than the current plan.
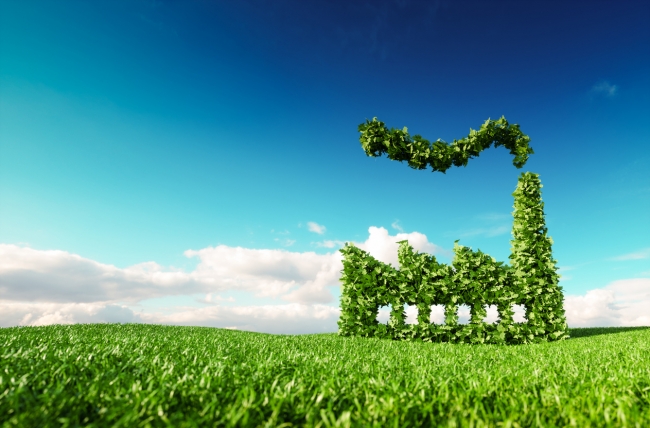
ERP technology can help make decisions on a range of topics, from planning the factory floor in a more efficient manner, buying more energy efficient machines to looking at implementing a full green initiative / Picture: Getty/iStock
So, what can the manufacturing sector do to reduce the environmental impact that it has on the planet
Circular Economy
Few industries are on the sustainability drive quite like the plastics sector. Ever since David Attenborough highlighted the growing issue of plastic waste through Blue Planet II, manufacturers have been pushed by consumer demand to seek out new ways to replace single-use plastics with more sustainable options, as well as developing manufacturing processes that have less impact on the environment.
Today, the case for sustainability is undisputed. Several types of plastic require less energy to produce than alternative material options, the calorific value of some plastics can be recovered through energy-from-waste techniques and the material plays a vital role in providing building insulation, aiding more sustainable construction efforts. However, the transition to plastics sustainability goes far beyond the end product itself. In fact, the journey to more sustainable plastics begins even before the manufacturing process, at the materials requirements planning stage. And technology can play a part here.
A key enabler of improved sustainability is the elimination of unnecessary waste across all manufacturing operations for plastics processors. This starts at the design concept stage of a product and continues through the product life cycle. The aim is to create a “circular economy” which has the fundamental principles of reduce, re-use, recycle, re-engineer or re-manufacture. The idea is to design waste out of every manufacturing process right from the start through to the end of life for the product.
Removing waste in the wider manufacturing sector
When it comes to operating leaner processes, a fully integrated Enterprise Resource Planning (ERP) solution delivers several benefits. Intelligent systems such as SYSPRO can process electronic data interchange (EDI) order files overnight without human intervention. This enables the accommodation of rapid changes in customer requirements amidst very tight lead times. Automatic changes to raw materials or production orders can ensure deliveries are always fulfilled and only accurate levels of raw material are requested.
However, waste is not always a physical entity. Indeed, time is one of the biggest waste streams found in manufacturing, which leads to more energy being used. Long drawn-out manual processes do not only extend production times but also place unnecessary strain on employees and increase energy consumption, contributing to a largely unsustainable workforce and CO2 emissions. A more sophisticated approach to inventory management that automates manual processes and helps reduce production times can significantly enhance sustainability.
With the assistance of an advanced ERP solution, inventory can be processed electronically, accelerating raw material intake and associated quality control checks. Furthermore, parameters such as inventory storage conditions can be set within the ERP system to help minimise premature material wastage. For example; products (such as food and chemicals) which need to be kept at a certain temperature, can avoid being wasted thanks to sensors alerting staff when the correct storage conditions are not met.
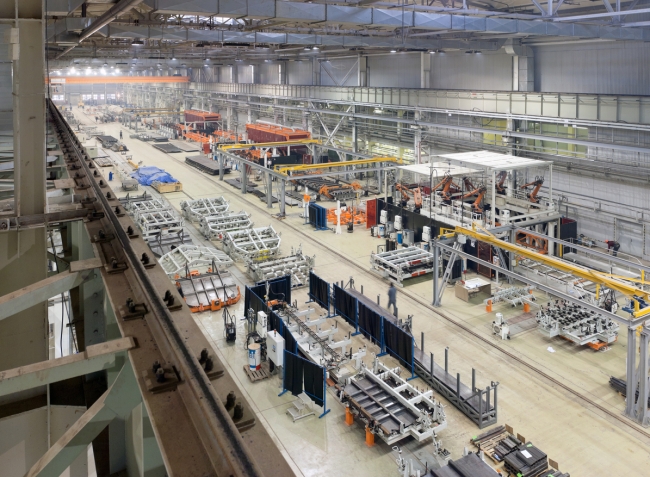
Everything from inbound logistics and operations to service and sales has the potential to be streamlined to reduce waste and update operational processes, thus making a business more sustainable / Picture: Getty/iStock
Reducing energy and costs
Understanding how to use less energy in your manufacturing processes can not only deliver economic benefits but will also assist with your own sustainability.
A fully integrated ERP system holds the key to all your business-critical information and can be used to identify the most productive plant and equipment cycles, to plan maintenance and operational schedules and, therefore, understand the potential ramifications of equipment failure. When plant managers can track historical trends showing machine failure, it becomes possible to predict future disruption and implement active redundancy measures to automatically reconfigure equipment operations and minimise disruption. This information can also help to schedule maintenance and repair work at optimum times to ensure equipment is not only running more efficiently but also that electricity use and the downtime associated with unplanned repairs are kept to a minimum.
With all of the data ready for interrogation at the touch of a button, ERP can help managers and directors make decisions on a range of topics, from planning the factory floor in a more efficient manner, buying more energy efficient machines to looking at implementing a full green initiative.
A greener supply chain
It’s not just the immediate manufacturing environment that can become more sustainable with the help of ERP – the entire supply chain can benefit. For example, data held within ERP applications can help plant managers better understand the environmental impact of logistics and transportation, and flex processes accordingly. And by regularly reviewing data held within ERP systems, loads can be distributed in more efficient ways and greenhouse gases can be reduced simply by switching to local suppliers or following faster delivery routes.
With so much global attention and focus on improving the sustainability of human behaviour, it is important that sustainability practices are implemented throughout the supply chain as this can later benefit the planet. Everything from inbound logistics and operations to service and sales has the potential to be streamlined to reduce waste and update operational processes, thus making a business more sustainable. After all, the key to creating a more sustainable product lies in a leaner, greener production process. At K3 Syspro we offer free discovery sessions to explore what companies want to get out of their ERP system, which areas of the business can be improved on and how this can be achieved, including how to make processes leaner and more environmentally friendly.
As humans, we have a long way to go to help the recovery of ecosystems, habitats and biodiversity. As is being highlighted through the various environmental movements, the aim is to achieve net zero emission and address the impact of physical pollution across the planet. But by creating leaner production processes, the manufacturing sector has a key part to play in meeting these goals.