6 minute read • published in partnership with Kawasaki Robotics
Insight: Eleven benefits of robotic automation in manufacturing and engineering
With more than 200,000 robots shipped worldwide, Kawasaki Robotics is a leading supplier of industrial robots and robotic automation systems with a broad product portfolio, able to service a wide range of applications across diverse industries. Here it shares eleven benefits robotic automation provides to the manufacturing and engineering sectors.
Ever since they hit the manufacturing floors of automobile manufacturers in the 1960’s industrial robots have been delivering no shortage of benefits to the bottom line. They have made factories safer, more efficient and more profitable. As the technology advanced and the benefits became apparent general industry manufacturing companies also began to adopt robot automation as a way to reap the rewards and increase their competitive advantage.
1 – Reduce floor space
Robots aren’t just limited to floor mounted configurations. Today’s robots are much more versatile offering inverted, shelf, wall and floor mounted configurations. This opens up a host of options for maximizing floor space.
Additionally, robot designs of recent years are significantly leaner than their predecessors and physically take up much less space than before. Programming also provides a means to reduce the amount of space needed allowing robots to work in very tight/confined spaces.
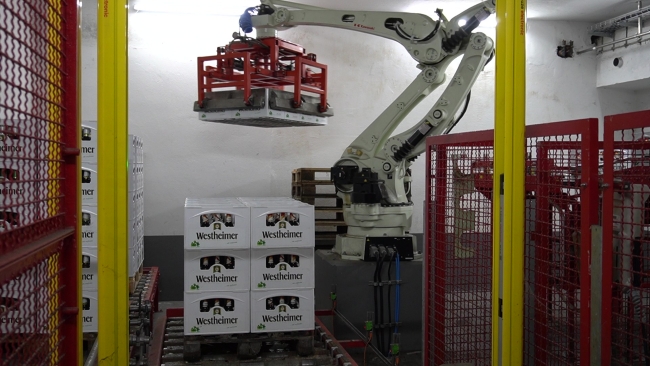
Picture: Kawasaki Robotics
2 – Improve product quality
Accuracy and repeatability are the two key features of an industrial robot that allow it to achieve consistently high quality parts, for most any type of product one can manufacture, regardless of application. Flawless finishes on painted surfaces, high quality welds that ensure the integrity of a product, and handling the most delicate of materials without damage are all real benefits that improve product quality.
3 – Reduce labour turnover
Recent studies have come out in favor of robotic automation, disproving the theory that they eliminate humans in the workforce. In fact, studies suggest that by bringing industrial robots in to do the “dull, dirty and dangerous” tasks manufacturers are able to retrain and redeploy their workforce into higher skilled jobs, resulting in greater job satisfaction for the worker and more value for the employer.
Additionally, as the workforce ages we are seeing fewer and fewer job seekers that are looking to enter into roles that involve heavy labour. Often, tasks requiring the high precision demanded by today’s industrial processes and/or the manual labor involved in the tasks, are seen as undesirable careers. This is yet another way industrial robots can contribute as they fill the gap left behind the retiring workforce.
4 – Reduce operational costs
The adoption of industrial robotics into manufacturing processes can allow businesses to realize significant savings in both direct and overhead costs. Due to their inherent flexibility and ease of programming industrial robots are able to be easily adapted to new production lines without the need for costly training which takes additional time away from production.
Their accuracy and repeatability means they consistently deliver the highest quality parts, minimizing defects and waste. Additional savings can be realized as industrial robots do not require healthcare, insurance or income and they have minimal need for heating/cooling, lighting and other comforts which further reduces energy consumption.
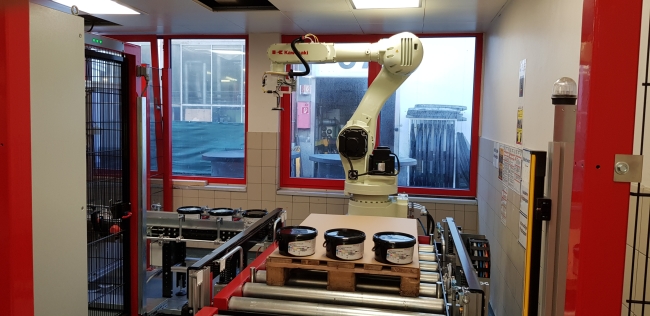
Picture: Kawasaki Robotics
5 – Increase manufacturing flexibility
Probably one of the most compelling benefits of robotic automation is the ease of change between processes, allowing manufacturers to meet the ever increasing need for product customization and design changes due to customer demand.
The ease of which an industrial robot can be reprogrammed means there is little barrier between the changes in consumer need and a manufacturers ability to respond to the market in a timely and cost-effective manner, thus increasing their competitiveness. Industrial robotics are the solution to today’s high-mix, low-volume productions and the ability to run different products on the same
6 – Improve health and safety
There is no disputing the rising costs of healthcare for both individuals and businesses. Providing workers with safer environments that minimize their exposure to the risks associated with certain tasks provides numerous benefits. By taking over the dull, dirty or dangerous tasks, industrial robots decreased the likelihood of accidents caused by contact with machine tools or other potentially hazardous production machinery. They also eliminate many adverse health effects associated with redundant and repetitive tasks that lead to conditions such as repetitive stress injuries, muscle fatigue and more.
7 – Reduce capital costs
Using robots to achieve faster, more efficient production lines can help reduce capital costs associated with inventory and work in progress (WIP). By moving products faster in production, businesses can better predict the production rate and ensure a fast and efficient service is delivered to the market at the right time. Due to their flexibility you can reprogram a robot to handle a different product or task often within the same production line, eliminating the need for additional capital purchases. Also, todays industrial robots are able to collect and share data about their performance that can give insights into its health and maintenance needs allowing manufacturers to maximize the life of their capital equipment.
8 – Improve quality of work
A business’s greatest assets are their employees and smart manufacturers understand the costs associated with high turnover, unhealthy or unsafe work environments and low job satisfaction and they seek to minimize them. Industrial robots improve working conditions for many employees, reducing their need to work in unsafe environments such as those associated with harsh chemicals, less than ideal temperatures, poor air quality and more. This further frees up the employees to be retrained with far more valuable skills allowing them to be redeployed in areas where humans are more uniquely suited and comes with greater job satisfaction.
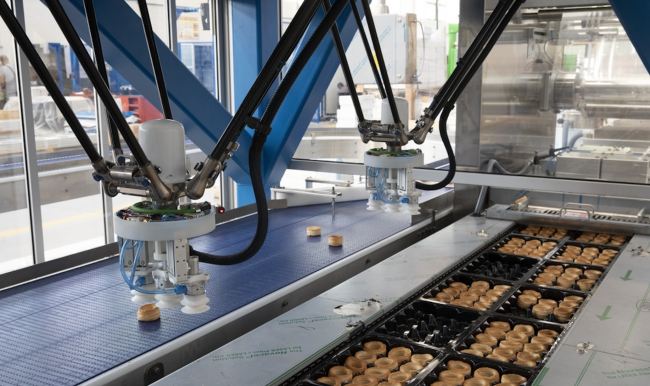
Picture: Kawasaki Robotics
9 – Reduce waste
There are numerous types of waste in the manufacturing process, all of which have a cost that affects the bottom line and need to be minimized to reap the most profitability out of your business. Industrial robots can minimize waste in a variety of ways. Perhaps the most obvious being the high quality finishes that are inherent with robot automation, or perhaps its the ability to handle the most delicate of parts without damage. It could be the reduction of contaminants entering a process leading to recalls and/or warranty work or the precision in which adhesives and/or paints are applied to parts leading to less product being used. Whatever the process or application, chances are that a robotic automation solution can contribute to waste reduction.
10 – Increase production output
Incorporating industrial robots into manufacturing processes helps improve production output, resulting in increased revenue and efficiency. Robots are able to operate 24/7 with no breaks and minimal maintenance to keep them running at optimal performance. They do no suffer from fatigue and never sacrifice work quality due to being overworked. They also produce superior quality at a fraction of the time it would take a human for the same task, resulting in more quality parts, in shorter time periods, available to be brought to market.
11 – Insight and analytics
Industry 4.0, Industrial Internet of Things (IIOT), big data, the cloud, AI…do all of these terms sound familiar? Do you even know what they mean? Are you adopting these practices into your factory?
Today, connected devices, sensors and the like allow companies to maximize their competitiveness because they have learned how to mine the data their industrial machines produce and collect it for analysis. They then can optimize their processes which allows them to make every part of their operations more efficient. Industrial robots can contribute to this as well. They enable those overseeing production to predict maintenance needs, reduce downtime and connected robots can even communicate with each other in the cloud syncing a variety of information and statistics that improves overall efficiency and collaboration. They can use AI and machine learning to improve their processes delivering better performance.