3 minute read • published in partnership with ITI Group
Insight: How to implement a successful condition monitoring strategy to optimise asset reliability
Implementing condition monitoring involves continuously tracking the health and performance of equipment or machinery to detect potential issues before they cause failures. It is widely used in industries such as manufacturing, power and utilities, and warehousing. Mike Taylor from ITI Group shares expert insights and best practices for implementing an effective condition monitoring strategy to optimise asset reliability, minimise unplanned downtime and drive continuous improvement across your operations.
In a marketplace saturated with condition monitoring solutions, the implementation of an effective strategy is key to achieving success. It’s not just about buying volumes of sensors; end-users need to ensure that their selected SaaS service provider offers the necessary support to implement the right condition monitoring solution for their business. At ITI Group, we prioritise helping clients clearly understand the value of their condition monitoring solution by demonstrating its ROI. This approach builds trust and ensures that clients feel confident about making further investments when the SaaS agreement concludes.
Here’s a step-by-step approach to implementing a successful condition monitoring program:
1 – Define objectives and scope
• Determine the goal: Are you monitoring to prevent breakdowns, optimise performance, reduce maintenance costs, or comply with regulations?
• Consider carrying out a criticality assessment.
• Identify the ROI – what will be the payback and how long will it take for the return?
• Decide what equipment or systems need monitoring (e.g., pumps, motors, turbines).
2 – Select the right monitoring techniques
There are several methods for monitoring the condition of equipment:
• Vibration Monitoring: Detects imbalance, misalignment, or mechanical wear.
• Temperature Monitoring: Indicates overheating or irregular temperature behaviour.
• Oil Analysis: Monitors contamination and degradation of lubricants.
• Ultrasound: Used for detecting leaks and electrical faults.
• Acoustic Emission: Monitors structural issues or cracks in equipment.
• Thermography: Uses infrared cameras to detect temperature variations in machinery.
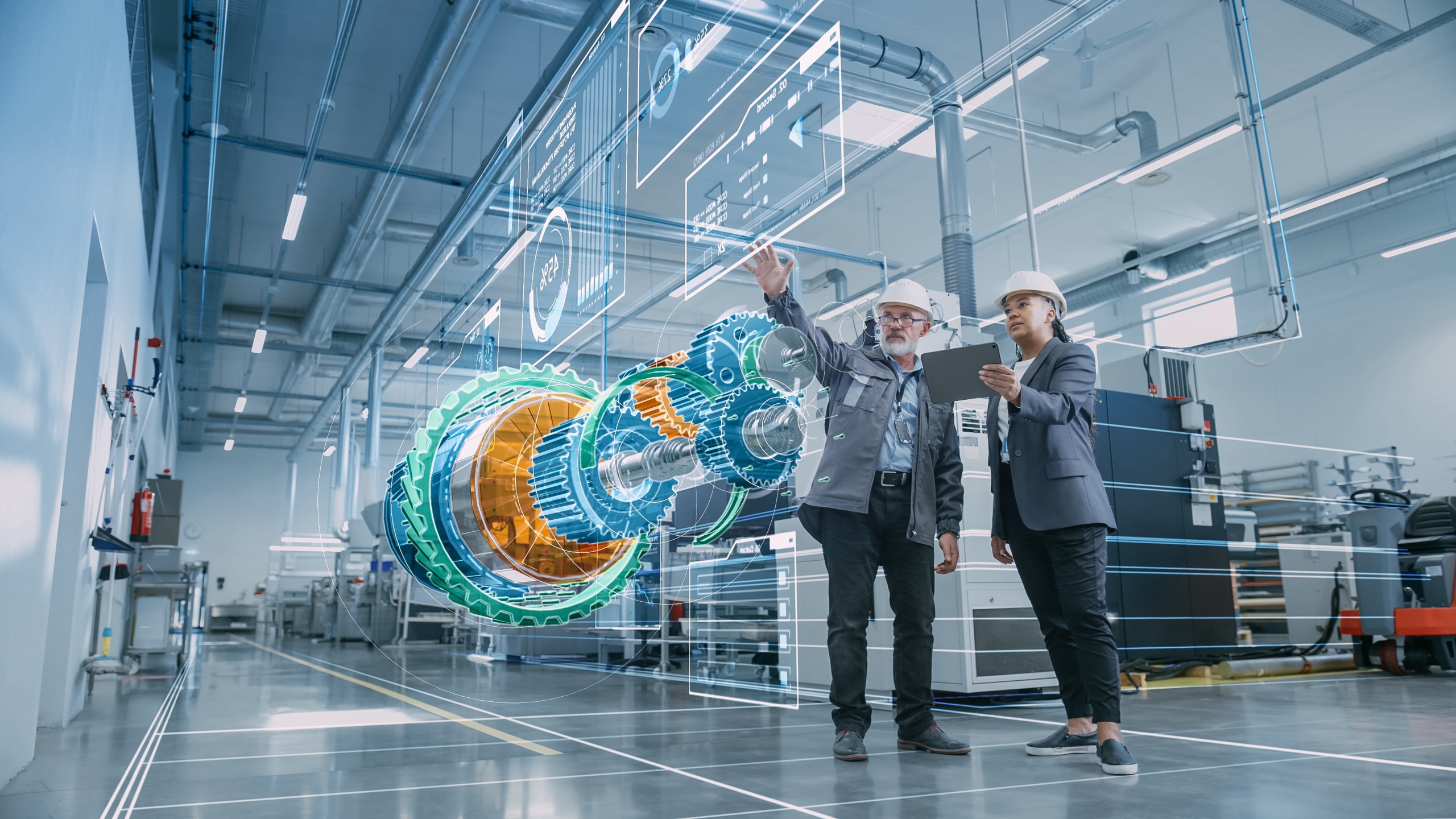
Picture: Getty/iStock
3 – Install sensors and data acquisition systems
• Install appropriate sensors and the right locations (e.g., vibration, temperature, pressure, etc.) on the equipment.
• Ensure that data acquisition occurs in real-time for effective monitoring.
4 – Data processing and analysis
• Use software tools to analyse data and detect trends or abnormalities.
• Apply techniques like:
Threshold-based analysis (e.g., if temperature exceeds a certain level, trigger an alert
Pattern recognition (using machine learning to detect patterns that indicate failure modes).
Predictive modelling (using historical data to predict future failures or maintenance needs).
5 – Set alerts and triggers
• Set up automated alerts for the maintenance team when a parameter exceeds a predefined threshold.
• Ensure alerts are timely and actionable to avoid unnecessary downtime.
6 – Maintenance decision support
• Use the insights from condition monitoring to optimise maintenance schedules. This can shift from reactive (fixing after failure) to proactive (fixing before failure) or predictive maintenance.
• Continuously refine the predictive models to improve accuracy.
7 – Integrate with enterprise systems
• Integrate the condition monitoring system with the broader enterprise system (e.g., Enterprise Resource Planning, ERP) to streamline maintenance workflows.
• This integration helps track inventory, manage labour, and streamline the procurement of replacement parts.
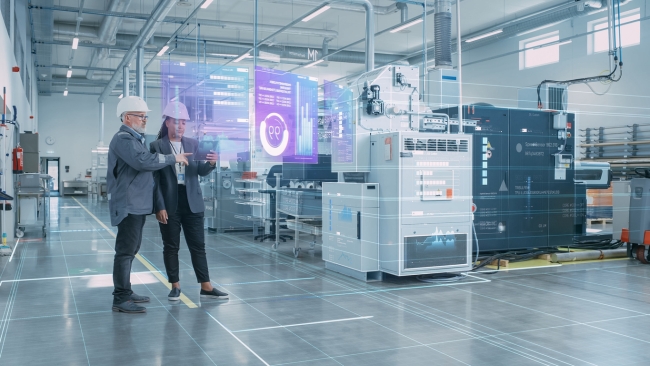
Picture: Getty/iStock
8 – Training and skill development
• Train your maintenance and operations teams to understand the data, how to interpret it, and how to take action based on the insights provided.
• Invest in the continuous improvement of staff through workshops and certifications in data analysis, sensor calibration, and condition-based maintenance.
9 – Continuous improvement
• Collect feedback from your team and adjust the monitoring systems, parameters, and methods as needed.
• Regularly review the performance of your condition monitoring program to ensure it is meeting its intended goals.
By following these best practices, you can establish a strong foundation for your condition monitoring solution, fully leverage its capabilities, and achieve maximum return on investment. Learn more about ITI Group’s condition monitoring solutions.