5 minute read • published in partnership with Desoutter
Insight: Manufacturers can improve productivity without having to make huge equipment investments
Boosting factory output doesn’t have to be complex or costly. Making simple, expert-guided changes in the right spots can deliver productivity improvements without the hassle or hefty price tag.
In the ongoing debate on how to raise manufacturing productivity, discussions typically revolve around the skills gap, technology adoption, R&D investments, regulatory reforms, transport infrastructure and greater industry-school collaboration. While calls for large-scale systemic changes dominate conversations, there are immediate improvement opportunities that manufacturers can seize that won’t break the bank and are proven to deliver tangible benefits.
“A common fault code we see in almost every factory is trigger release,” says Michael Heath, UK Operations Manager for Desoutter – a global leader in assembly solutions and process control. The fault occurs when the operator releases the trigger before the tool completes the cycle. This results in the operator having to attempt the fixing again and can lead to confusion in regards to believing that there is a fault with the tool itself.
“While this may seem a minor issue in isolation, our data analysis software reveals a high frequency of this fault occurring, especially in factories with temporary workers unfamiliar with intelligent tooling equipment. Without our DeMeter software, this fault typically goes unnoticed as each instance is relatively small. However, when customers utilise DeMeter to identify and address efficiency issues, we often find quick wins like this deliver the largest payback.”
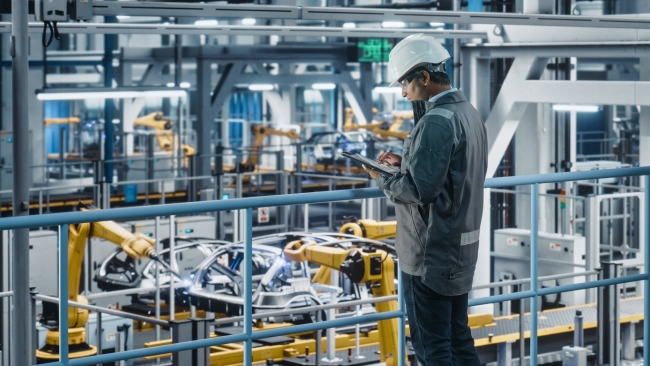
There are immediate improvement opportunities that manufacturers can seize that won’t break the bank and are proven to deliver tangible benefits / Picture: Getty/iStock
Tackling trigger release is a prime example of marginal gains, a philosophy of making small, incremental changes that collectively contribute to significant improvements. It’s an approach that Desoutter vocally champions, believing that every efficiency gain or innovation, no matter how small, contributes to the overall success of the manufacturing sector.
Stephen Draper-Garcia, CPI Business Line Manager, points to another frequently overlooked marginal gain – tool optimisation. “Many companies opt for the simplest or most familiar tool configuration. Doing so may deliver repeatable and acceptable results; however, fine-tuning controller settings and precisely configurating tools to the application can yield a 10% to 15% efficiency improvement in TAKT time. We recognise the time and cost pressures manufacturers face but we want to challenge the ‘good enough’ mindset. Our mission is to help manufacturers achieve their best and then encourage them to aim even higher.”
Holistic problem-solving
Desoutter’s proven approach involves bridging the divide between departments, providing a holistic view of operations. While factory workers have narrow responsibilities and targets, Desoutter engineers can immerse themselves in understanding fully the end-to-end production process. Their goal is to boost efficiency and productivity by fostering communication, collaboration and a shared understanding of business challenges.
“Siloed working and tunnel vision remain commonplace, especially between maintenance and engineering, and IT and production. Rarely does anyone have the time or opportunity to step back, look at things differently and question whether there’s a better way or where the real problem lies,” Stephen explains. “By having a holistic view and acting as a conduit between departments, we break down silos and encourage a collective approach to problem-solving.”
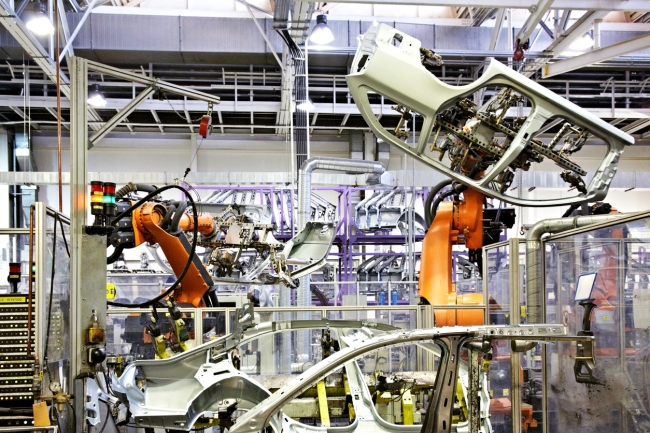
Some manufacturers have a misconception that improving productivity relies on investing in new equipment and technology, and that’s not necessarily the case / Picture: Getty/iStock
Identifying root causes and evidence-backed decision-making are crucial elements of this approach. Pivotware is a key part of Desoutter’s toolbox, helping companies move away from assumptions and gut feelings to making data-driven decisions. This powerful process control and worker guidance system provides transparent processes and a reliable information source, with assembly errors immediately detected and remedied thanks to smart tools and real-time feedback.
“Machines and software systems are inherently efficient; efficiency has been drilled into every aspect of their design from the drawing board to installation. Inefficiency comes from people, and it’s not always their fault,” Michael says. “Workers might be overstretched, undertrained or hindered by outdated processes and tools. This creates a breeding ground for lost productivity, costly errors and missed opportunities for improvement.”
Desoutter addresses these inefficacies head-on, providing not just cutting-edge tools and systems, but also the expertise and support necessary to empower workers, streamline operations and sustain constant improvement.
“When we began collaborating with a leading heavy equipment manufacturer, our aim was to help them produce a key assembly in-house and ensure a fault-free operation,” Stephen explains. “Despite the complexity involved, our close partnership resulted in a first-of-its-kind assembly and electrical testing station, and through the integration of our Pivotware process control, they now maintain an unprecedented 0% failure rate.”
Working in partnership with manufacturers
The remarkable 240% growth in Desoutter’s consultancy services over the past two years highlights the rising demand for their unmatched expertise and support. The boom comes at a critical time. In the face of supply chain disruptions, market uncertainties and fierce competition, the need to improve manufacturing productivity and efficiency has never been greater.
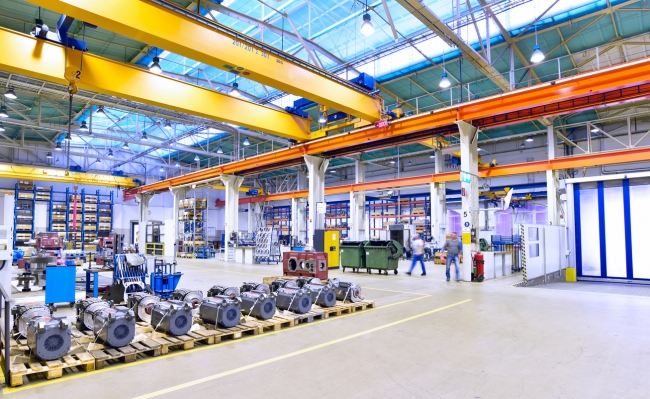
Desoutter addresses these inefficacies head-on, providing not just cutting-edge tools and systems, but also the expertise and support necessary to empower workers, streamline operations and sustain constant improvement / Picture: Getty/iStock
“Continuous improvement waits for no one. It’s not about merely surviving the next 12 months, it’s about achieving sustained long-term growth, and contracts don’t last forever,” Michael says. “We’ve seen recent instances of manufacturers losing out on contracts due to their production environment falling short of OEM or Tier 1 expectations. Continuous investment is vital to ensure you not only meet but exceed the minimum requirements.”
For those unable to invest in the foreseeable future, the message is clear – making do with the status quo isn’t your only option.
“You don’t have to wait until securing the budget before speaking with us,” Stephen says. “There’s a misconception that improving productivity relies on investing in new equipment and technology, and that’s not necessarily the case. There are likely inefficiencies within your business that you’re not aware of, and we’re eager to review those with you. There are almost certainly optimisations we can offer you to gain more value from what you already have. You may not know your factory’s full potential. We can work alongside you to map out a strategy to unlock it.”