4 min read • published in partnership with 1st MTA
Insight: Multi-part clamping revolutionises CNC machining efficiency
With hundreds of zero-points across the table or pallet of a vertical or horizontal machining centre, Sinco MultiZero workholding offers ultimate modularity and exceptionally high precision for securing multiple components for milling and drilling. The Slovenian-made systems are sold into the UK and Irish markets under an exclusive agency agreement with 1st Machine Tool Accessories (1st MTA), Salisbury, which describes here how manufacturers can harness the advantages of the workholding equipment to maximise productivity and accuracy.
How Sinco MultiZero works
Central to Sinco’s approach to increasing CNC machining efficiency and profitability are the novel, virtually limitless workpiece clamping arrangements made possible by its MultiZero base plate. It features an array of precisely spaced, conical, zero-point locations across its entire surface, at 50 mm or 100 mm centres. The high-density grid maximises usage of machine capacity by simplifying multi-part clamping over the entire table, utilising matching centring elements on the underside of other MultiZero modules that fit accurately into the conical holes.
These additional elements include pallets that attach to the base plate and can hold workpieces directly. Five different types are available for manual or automatic clamping of parts on a machining centre, while a die-sink or wire-cut EDM platform, measuring machine or assembly station may be similarly equipped. Pallets can be supplied fitted with an RFID chip to allow integration into an Industry 4.0 factory environment, enabling automation, digitalisation, automatic data capture and scheduling of production.
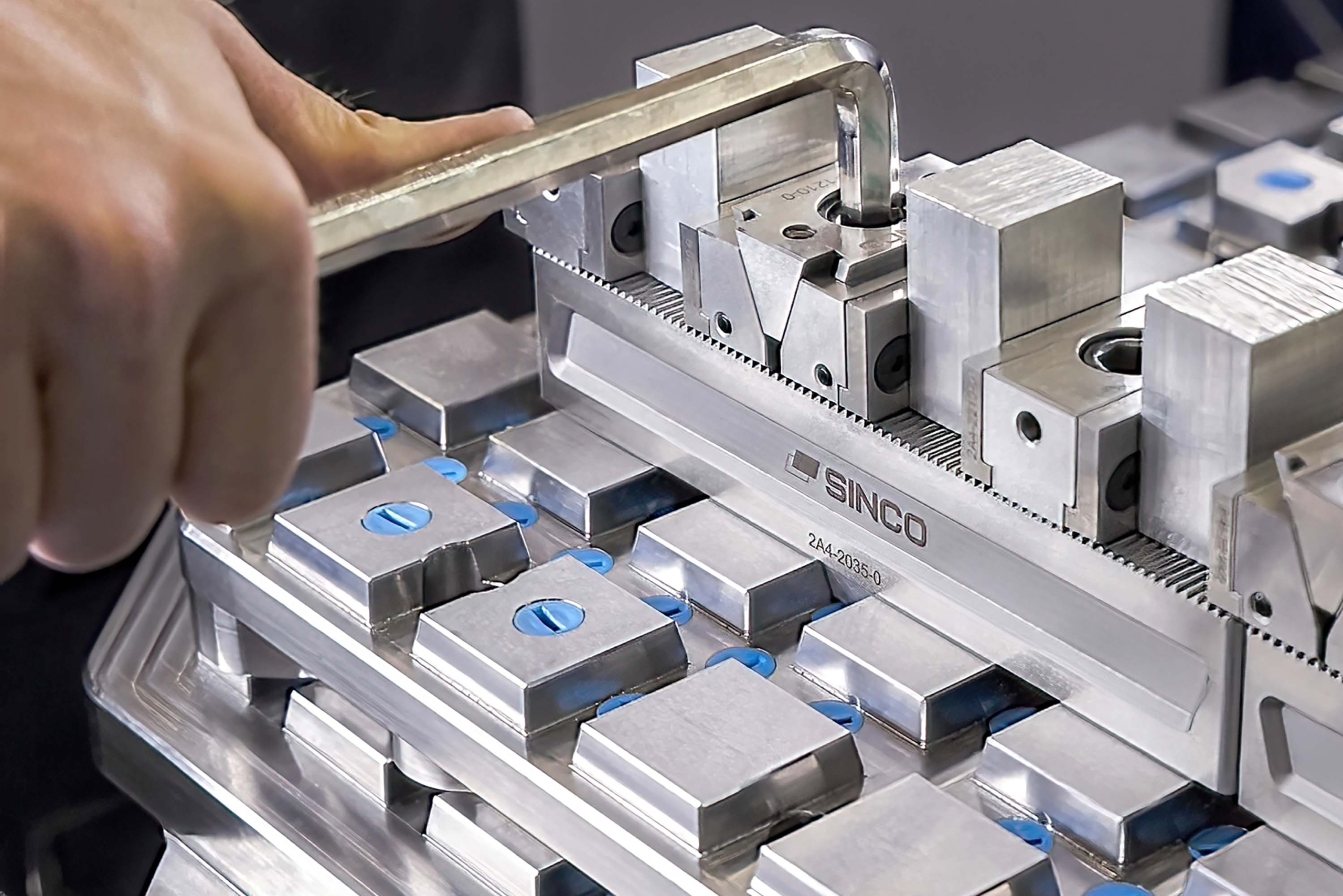
Enhancing CNC machining efficiency with Sinco’s multi-part workholding / Picture: 1st MTA
Other accessories such as modular vices, stoppers and risers can be mounted on top of the pallets in countless ways to suit different workpiece sizes and shapes. The absence of unnecessary jaws exposes the maximum surface of the part, reducing the number of set-ups and operations needed for completing the machining or inspection. Sinco claims a repeatability of 5 microns each time a new clamping element is added to one of their workholding set-ups, allowing very high precision metal cutting.
Each mechanical element is secured with an M12 screw having 65 kN of holding power, while pneumatic modules are rated at 55 kN. Pallets are held to the base plate with a force of 260 kN, making the whole configuration very rigid.
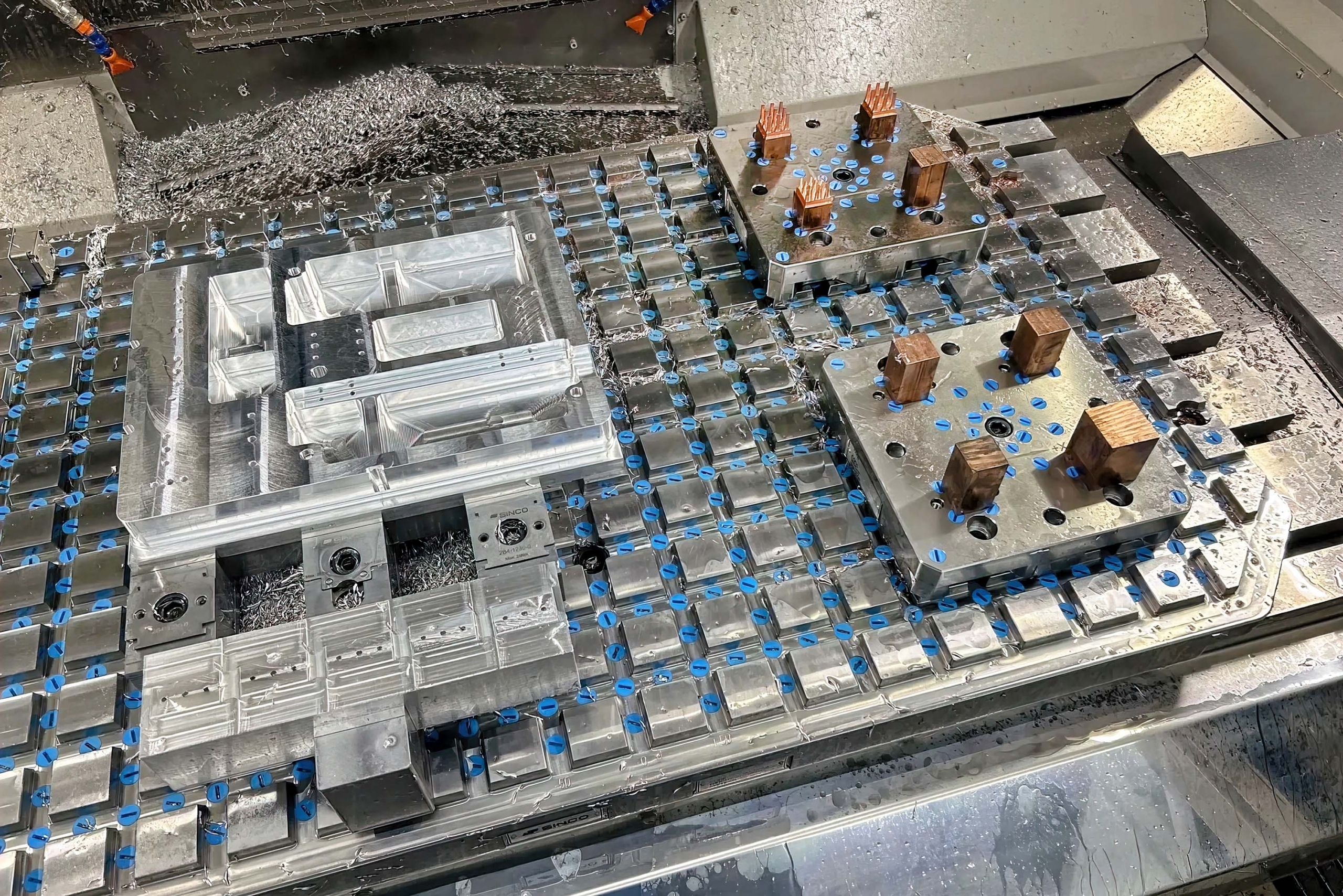
Aluminium workpieces (left) held in modular vices on a MultiZero base plate, with additional copper workpieces (right) prepared for electrode production on MultiZero EDM pallets / Picture: 1st MTA
Increasing productivity, reducing idle time, improving cost per part
In today’s highly competitive manufacturing environment, where every second of machine uptime directly impacts the bottom line, the ability to maximise utilisation and reduce costly idle time is paramount. The Sinco MultiZero system meets these challenges by offering a robust, flexible and extremely accurate workholding solution that empowers machine shops to achieve unprecedented levels of productivity by clamping multiple parts at the same time.
In this way, a machine can continue cutting for significantly longer without manual intervention. It not only extends unattended production time but also frees up skilled operators to manage several machines concurrently, or to focus on higher-value tasks such as programming, quality control or strategic planning.
The traditional bottlenecks associated with frequent workpiece changeovers, tool exchanges and machine set-up adjustments are dramatically reduced, leading to a substantial increase in factory throughput and a reduction in the overall cost per part produced. These improvements are magnified if the extended spindle engagement time allows a machine shop to move towards more lights-out manufacturing.
Beyond set-up efficiencies, the Sinco MultiZero system contributes to a reduced number of tool changes, leading to increased productivity. If a batch of identical workpieces is involved, instead of changing tools multiple times for each individual part, a single cutter can perform the same operation across all clamped components before it needs to be returned to the magazine, leading to a more streamlined and faster machining cycle.
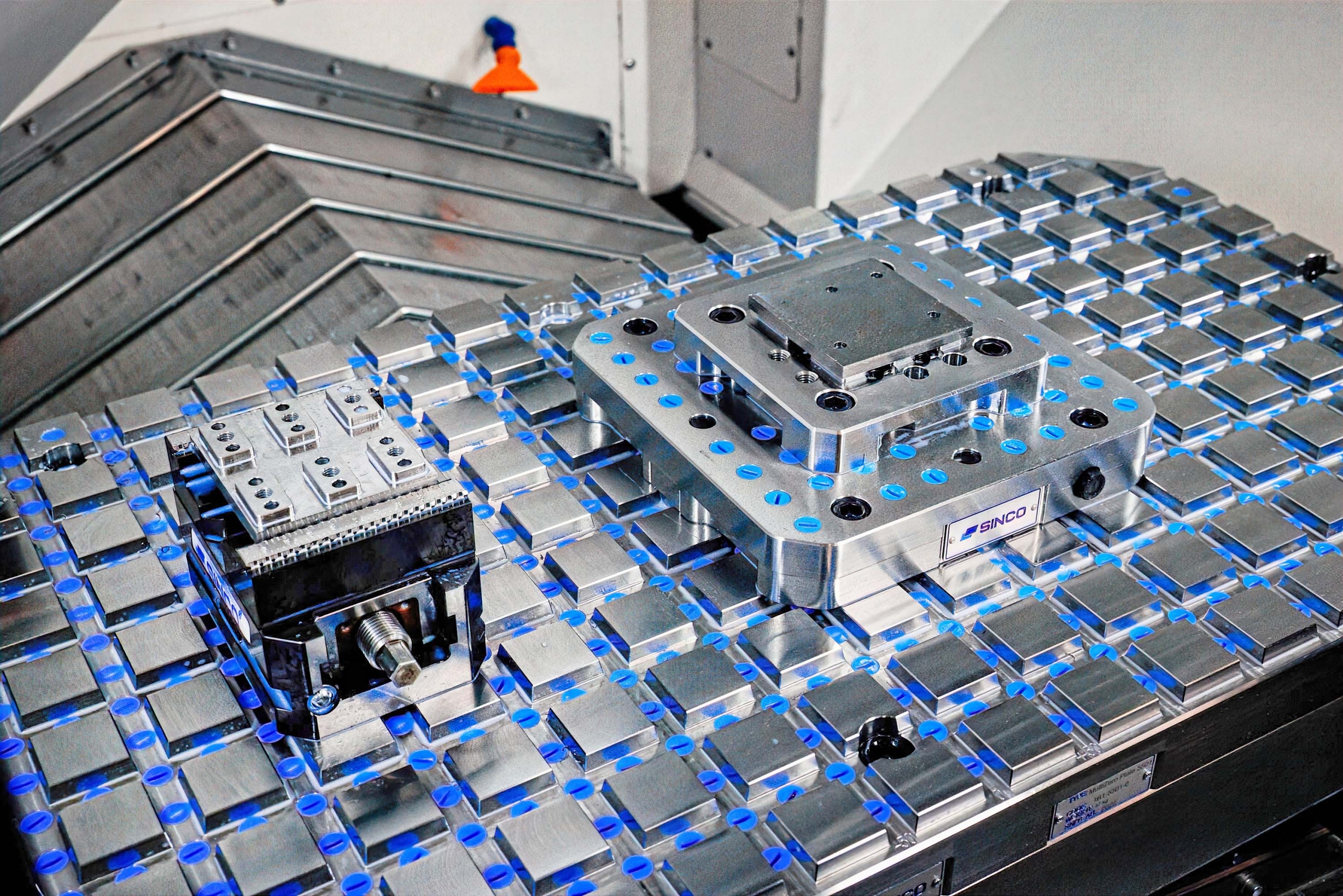
An alternative Sinco MultiZero clamping system configuration / Picture: 1st MTA
Integrating a modern Sinco production strategy
While the benefits of multi-part clamping are clear, implementing such a strategy can present difficulties, particularly concerning complex programming, accommodating variations in workpiece sizes and the need for adaptable fixturing. Sinco MultiZero directly addresses these challenges through its innovative design and the provision of a virtual model for each workholding element. The 3D data can be integrated into the programmer’s CAD/CAM system to allow the pre-planning of clamping strategies, improving the effectiveness of the cutting cycle that is generated and preventing potential problems later in the process.
1st MTA is committed to partnering with manufacturers to integrate a modern Sinco production strategy into their workflows, and to provide the consultancy and support needed to optimise machine utilisation, reduce idle times and achieve higher output. Shops that embrace the MultiZero system will not only streamline their processes, but also gain a significant competitive edge by unlocking new levels of efficiency and profitability.