3 minute read • published in partnership with ITI Group
Insight: Smart manufacturing – How to ensure maximum ROI of your OEE project
Manufacturers are investing more in digital technologies than ever before, reaping benefits such as increased efficiency, reduced production losses and improved preventative maintenance. But how many organisations see value from their digital investments? ITI Group looks at what manufacturers should be focused on to maximise ROI.
Recent studies show that many digital project investments fail to deliver the intended business benefits:
• Less than 30% of digital projects meet their goals (McKinsey)
• Just 10% of companies have realised a tech-enabled business model (Bains & Company)
• Only 30% of digital initiatives result in sustainable change (Boston Consulting Group)
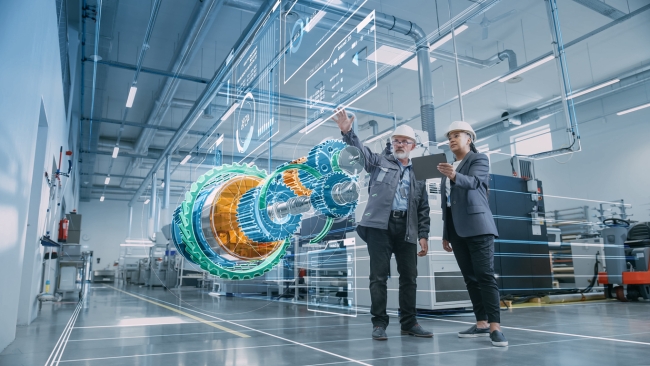
Picture: Getty/iStock
So, why will your project be any different? How will you ensure your OEE project delivers maximum ROI?
While justifying investment in digital technology to measure production performance (TEEP/OEE) may present some challenges, addressing these can lead to substantial benefits:
• Strategic investment with high potential returns: Although there are initial costs, these investments often lead to significant long-term gains and improved operational efficiency.
• Unified vision and benefits alignment: Aligning perceived benefits among stakeholders ensures everyone is on board, recognising the value this technology brings to the entire organisation.
• Seamless integration with existing systems: With careful planning and the right expertise, integrating new technology with existing equipment and systems can be smooth and enhance overall productivity.
• Enhanced data accuracy and reliability: Implementing these technologies provides an opportunity to improve data collection methods, resulting in more accurate and reliable performance metrics.
• Fostering a culture of continuous improvement: Embracing digital transformation encourages a culture of innovation, helping to overcome organisational resistance and driving continuous improvement.
Technology is only half of the solution
Other things should be considered when justifying an OEE project:
1 – Select a partner with domain expertise
Engage with a digital technology partner with specialist knowledge and experience in OEE projects. They can help you identify cost savings, inefficiencies, and areas for improvement that might be overlooked internally. By addressing these inefficiencies before making large-scale investments, you can avoid unnecessary expenses and ensure that your capital is allocated effectively.
2 – Ensure a consultancy-led approach to minimise risk
A consultancy-led approach to implementing OEE can help identify potential risks and challenges early on. This allows you to develop strategies to mitigate them before committing to significant investments, thereby reducing risk and enhancing the likelihood of success.
3 – Benchmarking & best practice techniques
Your partner should gather benchmarking data and provide best practice tools and techniques. This helps you understand how your operations compare to others and enables you to adopt proven strategies for improvement.
4 – Early system adoption & support
Training, coaching, and supporting your internal team to build internal capabilities are crucial elements of system adoption. This fosters a culture of continuous improvement and ensures long-term success.
5 – Maximise ROI of your OEE project
Upfront consulting activities allow you to pinpoint the initiatives that best support the business case. This approach lowers investment costs and improves the internal rate of return, maximising the ROI of your OEE project.
Improve your manufacturing operations in just 90 days with ITI Consulting’s OEE Express Programme Find out more on the out-of-the-box production reports powered by ITI Group’s performance/OEE module here. OEE Express Programme