4 minute read • published in partnership with Stäubli
Insight: Stäubli’s QCC contributes to mining sector net zero ambitions
The mining industry faces steep challenges when it comes to reducing emissions and pollution. The nature of mining work necessitates the clearance of land, the use of chemicals, and the ongoing deployment of heavy vehicles for digging and processing.
The contribution vehicles make to overall emissions from mining sites is significant. Mining vehicles account for 50 to 80% of the direct carbon emissions at the mine, with the amount of vehicular emissions tending to be greater for more mature mining sites, where deposits of ore require longer travel and hauling times. With 68 million tonnes of CO2 being emitted by some 28,000 mine trucks each year, there is huge potential to reduce the overall environmental impact of mining by addressing vehicular emissions.
Currently the International Council On Mining & Materials (ICMM), one of the major mining industry bodies, is looking to replace all mining vehicles with electric vehicle (EV) alternatives by 2050. Although EV’s are growing in popularity in many countries, and improved vehicle charging infrastructure is facilitating their use, the idea of replacing heavy duty mining vehicles does pose some additional challenges that are not faced by smaller domestic vehicles.
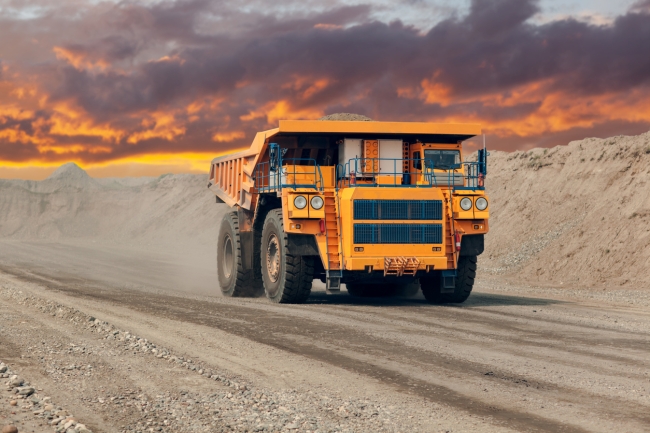
Picture: Getty/iStock
Mining sites often have very rough terrain and are often located in remote areas. The distances covered when transporting loads may be great, so there needs to be reasonable confidence that batteries can maintain their charge over these long-distance journeys, whilst hauling several tonnes of material.
All of these factors mean that batteries need to offer superb levels of reliability and any weight saving or improved capacity is critical. However, despite the numerous challenges, companies such as Stäubli are pioneering many new technological solutions to make EV’s a viable alternative.
These new innovations are helping the mining industry make the much-needed transition to low emission vehicles for a greener future. Stäubli has developed a connection system for the automatic charging of high-powered systems. One of the additional challenges for mining vehicles over their domestic cousins is that of the sheer scale of the vehicle, which means that the power demands are so much greater, so additional electrical infrastructure is needed.
The automated connection system – the QCC – offers a universal solution for charging various types of heavy-duty electric vehicles including buses, boats, and trucks, with relatively short recharging times. The system can transfer the high levels of power required for fast recharging of both lithium-ion batteries and supercapacitors. This innovative solution also allows for a new approach for electric vehicles, using smaller lightweight batteries and frequent charging for an overall more efficient vehicle that is not impeded by the burden of large battery storage capacity.
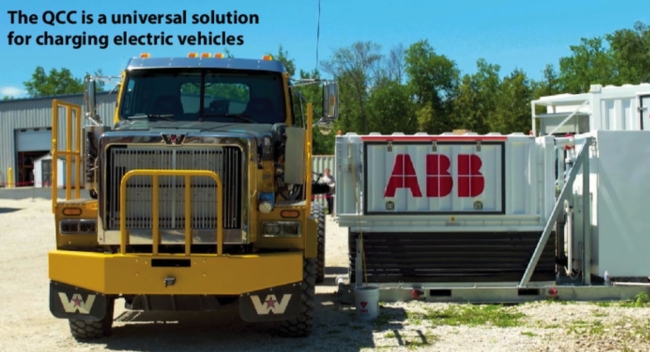
Picture: Stäubli
Just 20 minutes of charging time can provide four to five hours of continuous operation. The QCC system can provide up to 1500V and 670A continuous, or 1000A over the short term for very rapid charging, with the added benefit of being future proof through the ability to scale power and design. The QCC reframes the idea of the types of vehicles and batteries which can be used in mining applications, as it is designed to be easy to integrate within existing plants.
Customer Benefits
The system offers interoperability according to standards IEC 63407/ SA E3105/3. Stäubli’s QCC solution features integrated angular and positioning misalignment compensation, eliminating the need for any external positioning sensors or adjustment parts. There is also a self-cleaning mechanism, particularly important for the dusty and dirty mining environment, which will further extend the already impressive service life, guaranteeing reliable operation over a large number of mating cycles with virtually no maintenance.
Safety is of the utmost concern within mining sites, where there are often accidents each year, and much of the equipment is continually exposed to relatively harsh environmental conditions. As an enclosed and fully automated connection solution, no manual input or interaction is required during the charging process, and the system is also protected against touch, eliminating any risk for nearby workers.
Decarbonisation
There are now a number of targets, agreed worldwide, which outline decarbonization plans to be achieved by 2050. The benefits and positive environmental impact that EV’s could bring to the mining industry are clear, as is the need to change current practises, however achieving these may appear prohibitively expensive.
Another benefit of the QCC is that it can be retrofitted with ease to existing infrastructure. In addition to opening up the possibility of using vehicles with smaller batteries, the installation of the QCC does not require any major construction effort. The small footprint of these charging points also means there is no need for redesign, or any major work required to incorporate the benefits of rapid charging within existing sites.