5 minute read • published in partnership with Desoutter
Insight: Strategies to maximise aerospace production capacity
To meet soaring demand for new aircraft, aerospace companies must increase output without compromising quality. Achieving this balance hinges on successfully blending best-of-breed technology with expert human know-how.
The commercial aerospace sector is experiencing a remarkable recovery, buoyed by a healthy backlog of 15,694 orders for aircraft and almost twice that for engines*. The resurgence in international travel is fuelling demand, with order rates soaring, especially for wide-body aircraft. Long-term growth indicators are also strong, with numerous major deals expected to be announced at the Farnborough International Airshow.
This growing confidence is welcome news for UK aerospace, a sector that already contributes nearly £11bn in value add to the UK economy, exports goods worth £20bn annually and directly employs 104,000 people, including 6,000 apprentices*.
The current backlog, estimated to be worth nearly £248bn to the UK alone, represents over a decade’s worth of work at current production rates. Fulfilling these orders, however, presents a formidable challenge. While prime aircraft manufacturers like Airbus, Boeing, COMAC and Embraer look to ramp up production, they are being held back by a lack of capacity.
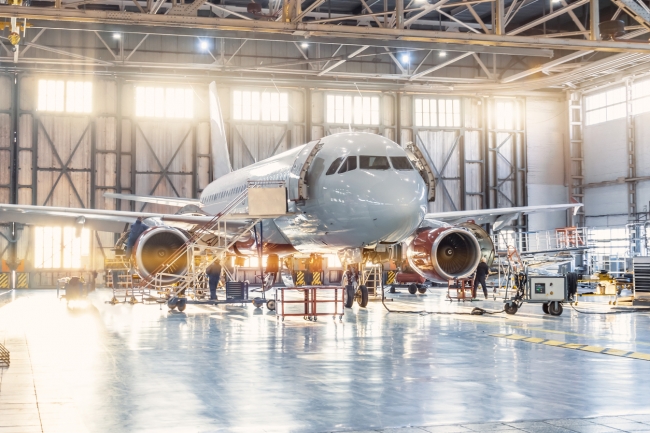
Picture: Getty/iStock
Tackling this challenge is vital to capitalising on the sector’s growth trajectory, says Howard Green, an aerospace specialist at Desoutter – a global leader in assembly solutions and process control.
“To meet booming demand, manufacturers are having to build all parts of an aircraft, from cockpits to tails, more quickly while maintaining the highest levels of safety and quality. However, the availability of people and production capacity remains a major constraint,” he explains.
Substantial gains from simple changes
In aerospace, there is a constant demand to reduce labour hours and manufacturing costs per part. Fortunately, massive efficiency gains can be made through simple changes like improving right-first-time quality and ensuring that work instructions or help documents are readily available to operators. Equally, the drive towards carbon neutral manufacturing sets out fantastic opportunities through the reduction or removal of compressed air as battery powered tooling becomes a reality.
Scott Howard, Aerospace Sector Manager at Desoutter, illustrates how a small change can lead to significant time and cost savings; “Millions of holes are drilled every year in aerospace factories, often through multiple layers of material at once. Drilling through 38mm of composite on top of 19mm of titanium can take over two minutes with a fixtured pneumatic drill, compared to just 46 seconds with a fixtured smart electric drill.
“Both take exactly the same 41 seconds for the titanium. The huge 63% decrease in overall cycle time is down to the electric tool’s ability to optimise its drilling speed – slower through titanium, faster through composite. A pneumatic drill can’t achieve this performance as it will be set to the optimum speed for the hardest material in the stack. This time saving from simply switching from pneumatic to electric is a great example of how optimisation, not revolution, can deliver an instant return.”
For those wishing to go a step further, light automation like robotic arms or collaborative robots (cobots) presents a significant opportunity to drive efficiency, precision and safety in aerospace manufacturing.
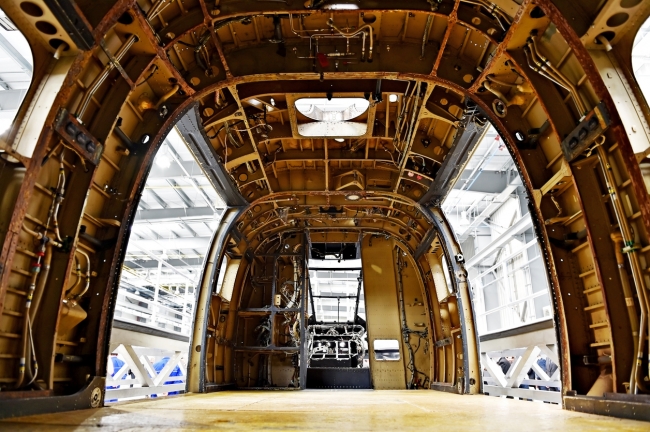
Picture: Getty/iStock
“By automating repetitive tasks, robots significantly reduce human error while boosting productivity. Their flexibility and adeptness at handling intricate operations ensure unparalleled accuracy and consistency,” Howard says.
For some companies, lightweight automation may represent their first foray into robotics. For more experienced users, it might be about replacing heavy automation systems with lower-cost, more flexible solutions. Regardless of the driver, Desoutter is well-experienced in integrating light automation seamlessly into existing workflows for tasks such as riveting, drilling, fastening and more.
Addressing the core challenge
Light automation is part of the Desoutter ECOSYSTEM, an interconnected ecosystem of tools and technologies designed to enhance efficiency, empower operators and drive continuous improvement.
It brings together a range of flexible, scalable and intuitive technology solutions with expert support to tackle current and future production challenges effectively. At its heart are Desoutter’s five interconnected cores:
• Connected Assets: Integrates operational equipment with IT for real-time quality measurement, error-proofing, traceability and asset management.
• System Integration: Provides tailored packages of tools, software and light automation to suit all applications.
• Motion Capture: Offers real-time tracking of assets and operator movements to increase right-first-time quality and efficiency.
• Process Control: Simplifies production complexity through workstation management, operator guidance, task standardisation and variant management.
• Data-Driven Decisions: Employs continuous production data analytics with alerts and notifications for informed decision-making and proactive action.
These cores directly align with three key focus areas in aerospace: safety, quality and cost, Howard explains; “Increasing shop safety can be as simple as replacing your pneumatic or air-powered equipment with ergonomic electric tools, creating a quieter, more comfortable workspace without trailing hoses.
“Operator guidance systems with user-friendly interfaces can guide workers through assembly step by step, optimise your manufacturing process and eliminate the risk of forgotten operations and confused components. Data analytics can track every aspect of production in real-time, enabling you to detect abnormal operations and identify trends, bottlenecks and areas for improvement.”
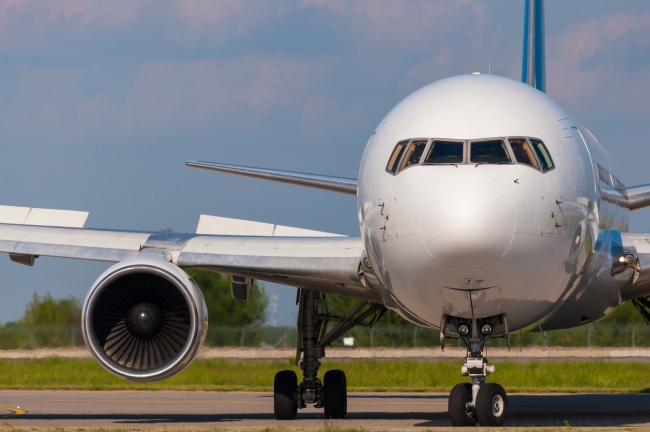
Picture: Getty/iStock
Understanding total cost of ownership
Solutions like these are flexible, scalable and proven to simplify the assembly process, boost line efficiency and improve final product quality. Yet, aerospace has been slower to embrace them compared to other sectors like automotive and general industry.
Could it be that aerospace companies are failing to grasp the total cost of ownership? TCO encompasses all costs associated with buying, operating and maintaining equipment over its entire lifecycle, not just the initial purchase price. Understanding TCO is crucial for making decisions that optimise short and long-term financial returns.
“At Desoutter, we stress the importance of evaluating TCO to truly understand the value of our solutions. This involves considering not only the upfront investment but also factors such as energy consumption, maintenance costs, downtime, productivity and future scalability,” says Howard.
Scott agrees, adding that simply choosing a solution because it has a lower initial investment is often not the best strategy; “By only focusing on the short-term, you risk making decisions that may seem cost-effective today but prove more costly in the long run.
“We understand that aerospace manufacturers are under severe financial constraint. However, with healthy order books, a decades’ worth of work and more growth forecast, now is the time for long-term, bold decisions and Desoutter can support you at every stage to prove this.”