5 minute read • published in partnership with Human Workspace
Insight: UK manufacturing lacks confidence, not productivity
While headlines frame the UK productivity ‘puzzle’ as a complex riddle, the reality couldn’t be simpler. We know how to boost throughput and global competitiveness; what’s missing is the confidence to act. It’s time to reclaim that confidence and unlock our true manufacturing potential.
In a world rife with uncertainty – economic swings, shifting market demands, climate change, geopolitical turmoil – you’d expect manufacturing leaders to at least have a solid grip on their factory floors. Yet, too many business owners don’t have that control. This lack of insight isn’t just a minor inconvenience, it breeds doubt and complacency.
When complacency sets in, manufacturers become satisfied with “good enough,” assuming what worked yesterday will work tomorrow. But this mindset holds them back while competitors surge ahead. Every moment spent resisting change is lost to those willing to challenge the status quo.
“If you’re unable to say with confidence exactly what’s happening on the factory floor, you can’t make the decisions that matter. You’re stuck in reactive mode, constantly firefighting instead of anticipating problems before they hit,” says Clive Sefton, operations manager at Human Workspace – a process optimisation specialist that combines physical infrastructure with smart manufacturing systems to boost performance. To break free from this complacency trap, owners don’t need more productivity tips, they need confidence. Confidence from knowing their operations are performing at their best, enabling them to steer their business with purpose.
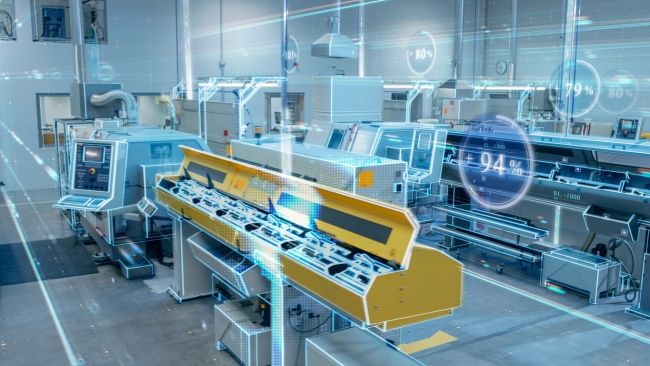
Picture: Getty/iStock
Confidence starts with clarity
Confidence in factory operations starts by having visibility into everything that’s happening – from machine performance and workflow rates to quality control and employee efficiency.
“This isn’t about guesswork or spending hours walking the floor with a clipboard and pen. It’s about using smart manufacturing technologies that are proven and priced to match SME budgets,” explains Nick Chippington, Systems Engineer at Human Workspace.
“These tools provide decision-makers with valuable insights, grounded in real-time data, to pinpoint inefficiencies, streamline processes and foster continuous improvement. When you know every part of your operation is optimised, bold decisions come easy.”
But this isn’t just about adopting new technology; it’s about building trust in your systems. Once an owner trusts their systems, they’re more likely to embrace strategies that drive competitiveness and growth.
Empowering your workforce
Building confidence doesn’t stop at systems – it’s about people, too. Equipping operators with the right tools and data can transform how they work.
“Imagine workers that can take ownership of their roles, identify issues in real-time and act on them. That’s the power of smart manufacturing systems and the confidence they inspire across your entire team; while giving you confidence they’re performing at their best,” Clive says.
“Leaders often underestimate how much their workforce can contribute when they have the tools and data to make on-the-ground decisions,” adds Nick. “With intuitive, easy-to-use technology in place, operators can proactively address issues and optimise workflows, rather than waiting for managers to step in.
“A key part of driving efficiency improvements is empowering operators with access to data, training and ergonomic solutions that help them deliver better outcomes for your business.”
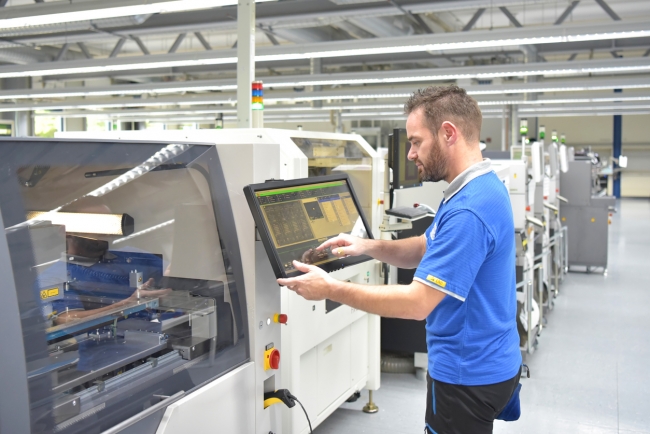
Picture: Getty/iStock
Cutting through the jargon
Confidence in your factory and workforce is one thing, but how do you gain confidence in choosing the right technology? There is an overwhelming array of solutions on offer, from automation and collaborative robots to smart tooling and operator guidance systems.
“The challenge for SMEs lies in making sense of the noise. Buzzwords like ‘Industry 4.0’ and ‘Digital Transformation’ are everywhere, but how do you know what will actually work for your business?” says Nick.
Investing in the wrong solution can be costly, and navigating the crowded tech marketplace can be daunting. This is where the right partner becomes crucial – one motivated not by quick sales but by taking the time to understand your operation and provide practical, tailored solutions.
“The last thing owners need is to get distracted by flashy tech trends and marketing hype. They need help identifying opportunities that align with their unique needs. Technology is more intuitive and accessible than ever, but without clear guidance and support, you risk wasting time and money on solutions that don’t deliver,” Clive explains.
The confidence to compete and win
Human Workspace helps manufacturers optimise their processes by demystifying smart manufacturing and implementing the systems they need to stay competitive. The team’s hands-on support ensures SMEs can make informed decisions and avoid common pitfalls, offering personalised advice, ongoing support and actionable strategies that lead to measurable gains.
Whether it’s ergonomic workstations, automation or control software, Human Workspace focuses on solutions that make a lasting impact, not quick fixes that fizzle out. This mission is supported by their ecosystem of trusted suppliers offering proven, compatible solutions, connecting manufacturers with the right hardware and software for their work environment.
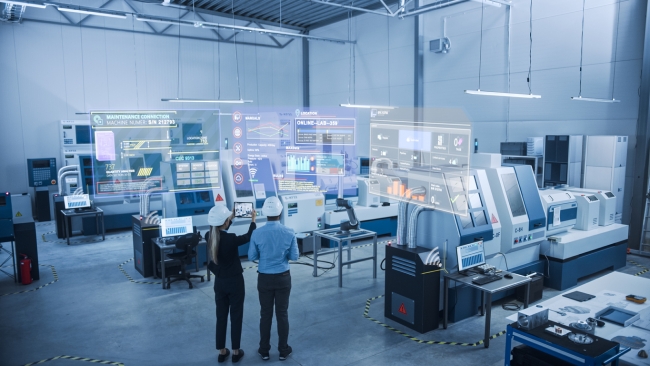
Picture: Getty/iStock
“We’ve distilled our 20 years of experience into a no-nonsense roadmap designed to give SMEs the clarity and confidence they’re on the right path and their factories are prepared for the future. It’s practical guidance without the jargon. A clear, step-by-step plan that walks you through assessing your current operations, identifying improvement opportunities and implementing change,” says Nick.
“Our roadmap is more than just a guide, it’s a confidence-building tool that allows you to move forward with certainty, knowing Human Workspace is by your side step of the way,” adds Clive. “It’s time to stop doing what you’ve always done. The key to success is understanding where to start and choosing what will deliver results, not just what sounds good on paper.
“By leveraging our roadmap and supplier ecosystem, leaders can navigate the changing manufacturing landscape with confidence, knowing they have the right systems in place to solve today’s problems and position themselves for success in the years to come.”
Confident leaders act – and their factories thrive
Human Workspace takes the time to understand what will help your operation and, best of all, our advice is free. From purchasing to installation and project management, we help you implement the right systems, streamlining your processes while you keep production on track. Read the Human Workspace no-nonsense roadmap for practical answers without the marketing guff.