5 minute read • published in partnership with NoMuda
Insight: Why is data democratization important to manufacturers?
The last 20 years have seen a significant sprint towards data. As manufacturers, you all provide monumental amounts of data every day. It is incredibly valuable in manufacturing, and the importance of real time data analytics continues to grow as the industry becomes more data-driven and technologically advanced. NoMuda VisualFactory explores how data democratization streamlines and simplifies the way that manufacturers collect data, improving data integrity, and giving manufacturers the confidence and ability to make better informed decisions based on the data available to them.
Are you able to accurately identify bottlenecks in your manufacturing processes? According to a recent study from ‘London Daily News’, over 44% of respondents estimated their company loses more than 10% of their annual revenue due to poor quality data. This is often due to the lack of a structured and effective data monitoring process. NoMuda’s MES (Manufacturing Execution System) VisualFactory gives manufacturers the ability to empower employees at all levels to access, analyze and leverage data to make informed decisions that have a positive impact on the overall manufacturing process.
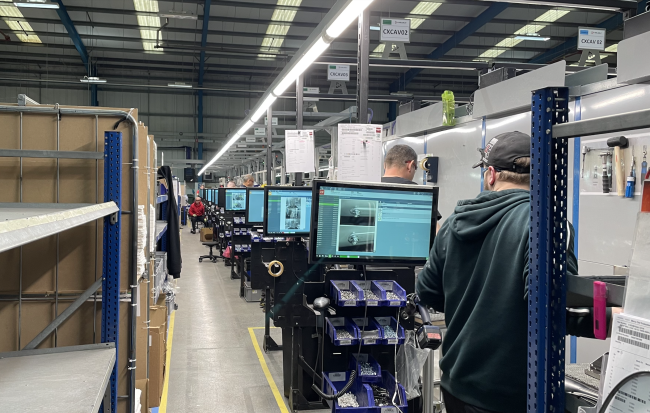
Picture: NoMuda
Data Ownership, Data Distribution and Real-Time Monitoring
Data Ownership
Data Ownership, Data Distribution, and access to Real-Time Data Analytics are the 3 pillars that manufacturers should aim to prioritize when looking to achieve Data Democratization. Cleaning up your data is the first step to establishing employee accountability and compliance within your manufacturing facility. NoMuda VisualFactory ensures that employees are accountable for the accuracy, security, and integrity of your organizations data – allowing your team to take full ownership of the decisions that they make. This accountability helps to prevent data breaches, errors, and misuse.
Remove the pressure from your security and compliance teams by promoting data ownership within your manufacturing facilities. Data ownership includes safeguarding data from unauthorized access, theft, or cyber-attacks. Data integrity is an area that is particularly important within manufacturing, where sensitive information about processes, products and intellectual property is often stored. On top of that, many manufacturing facilities are subject to highly strict security and compliance requirements (e.g., ISO Standards and FDA Regulations). Data ownership ensures that sensitive data is managed in accordance with these different regulations, highly reducing the risk of legal and financial penalties
Data Distribution
The next area that manufacturers need to consider is the distribution of data. Distributing data to the right people at the right time ensures that processes run smoothly. Managers, Supervisors, Operators, and many other faculties can access data related to their responsibilities, giving them the ability to monitor and control operations effectively. The key decision makers within a manufacturing facility will need to consider how they allocate resources within their respective departments. These resources might consist of labor, equipment, and materials. Distributing data on resource utilization and availability helps to optimize resources for efficient production.
Real Time Monitoring
Finally, real-time monitoring or ‘real-time data analytics’ is a valuable asset that many manufacturers still don’t take advantage of. Making decisions on the fly, detecting issues faster and allocating resources more efficiently. These are just a few of the benefits that manufacturers could take advantage of after implementing NoMuda VisualFactory on the manufacturing shop floor. Think about how much you could reduce your downtime by having access to real-time data that can detect issues, as well as improve response times.
Using NoMuda VisualFactory, your maintenance teams will be alerted to equipment problems promptly, reducing unplanned downtime and propelling the move towards Data Democratization. Real-time monitoring also helps to improve your quality control by identifying bottlenecks or deviations from specifications as soon as they happen! This allows manufacturers to implement corrective actions much quicker, reducing the likelihood of a defective product.
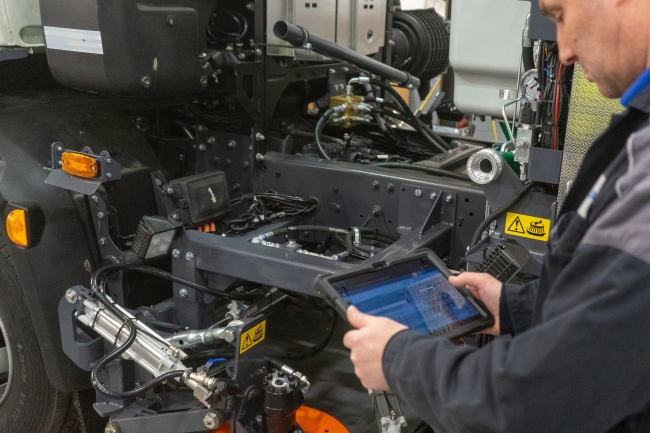
Picture: NoMuda
The risks of using ‘Dirty Data’
Using Dirty Data (incomplete, inaccurate, or low-quality data) when trying to make informed decisions is a recipe for disruption to your manufacturing processes. The following risks can negatively affect many different areas within your manufacturing facility, as well as negatively impact overall business performance:
#1 Misinformed Decision-making:
Misinformed decision-making is often the outcome of using Dirty Data and can harm many areas within a manufacturing facility. For example, resource allocation, inventory management and production scheduling can all be affected due to a lack of data integrity. This can often result in problems with overstocking, production bottlenecks and increased operating costs. Using NoMuda VisualFactory manufacturers get access to real-time data analytics, giving operators, supervisors, and managers the ability to make informed decisions quickly.
#2 Issues with Quality:
Quality issues can often stem from the use of Dirty Data. ComplianceQuest highlights 6 common quality issues within the manufacturing industry:
1 – Lack of standardized SOPs
2 – Siloed approach to Quality Assurance
3 – Inefficient Supplier Quality Management
4 – Improper Equipment Management
5 – High Cost of Quality
6 – Manual Training
These issues can often cause a ripple effect throughout a manufacturing facility, resulting in product defects or variations from the original specifications, causing compromised product quality and safety. This can lead to recalls which can often damage a company’s reputation. NoMuda VisualFactory is the solution when looking to achieve first-time quality throughout your production line. VisualFactory ensures that your tools and equipment receive the scheduled maintenance and repairs needed with its vTools and vMRO (Maintenance, Repair and Overhaul) modules.
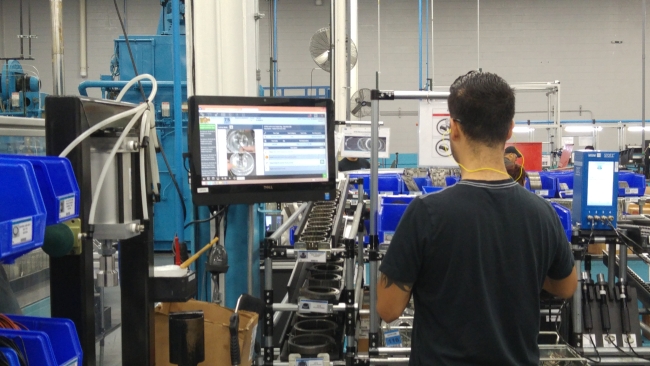
Picture: NoMuda
#3 Rework and Waste:
The impact that Dirty Data can have on material waste and product rework is immense. Incorrect material usage often leads to waste and increased costs. On top of this, defects that are caused by a lack of data integrity may require rework or scrap, increasing costs even further. NoMuda VisualFactory’s vRework Module allows you to rework damaged parts or products and locate production issues, minimizing effects on production line efficiency and reducing the need for rework.
#4 Excessive Downtime:
As previously mentioned, using inaccurate data to assess equipment performance and maintenance schedules can often result in manufacturing equipment not receiving the servicing required at a specific date and time. This leads to unplanned equipment downtime, which reduces productivity and causes a disruption to production. VisualFactory’s vMRO Module allows operators to track and manage products through the entire lifecycle, linking information from the build, to determine why failures have occurred during operation. This gives employees the ability to analyze the data and determine the correct actions to take in order to avoid excessive downtime in the future.
#5 Higher Operating Costs:
The immense effort required to clean and rectify inaccurate data can be resource-intensive and costly for manufacturers. This expenditure is avoidable by implementing an effective data capture system that improves overall data integrity. VisualFactory ensures that you always have the right data at the right time.
#6 Missed Opportunities:
Last but not least, Dirty Data will often obscure vital insights and trends that could lead to new opportunities for cost reduction, efficiency gains, or innovation. Can you imagine how many organizations miss out on opportunities due to a lack of reliable data?