5 minute read • published in partnership with Human Workspace
Insight: Why SMEs are falling behind in technology transformation and what needs to change
Trapped in a cycle of firefighting and quick fixes, small manufacturers are being sold a vision of smart connected factories that doesn’t address their unique challenges. For SMEs, this cookie-cutter approach to digital manufacturing simply doesn’t work.
UK manufacturing faces many shortages – chief among them, greater acknowledgement and support from those outside the sector. But one thing it has in abundance is resources – playbooks, infographics, case studies and webinars – all designed to steer manufacturers toward ‘Industry 4.0’.
While industrial digital technologies offer countless advantages, many of these guides fall short for the businesses that need them most: SMEs. Too often, they’re geared towards large-scale, mass production operations and promote the latest tech trends, rather than addressing the high complexity, low volume challenges small manufacturers face.
SMEs don’t need to know how a multi-billion-pound corporation built the world’s most advanced production facility. They need practical, scalable solutions that maximise process efficiency and profitability – solutions that match their size and budget. Whether it’s reducing machine downtime, automating key processes, improving quality or streamlining worker training, SMEs need guidance that speaks to their specific operational needs, not solutions tailored to someone else’s ideal.
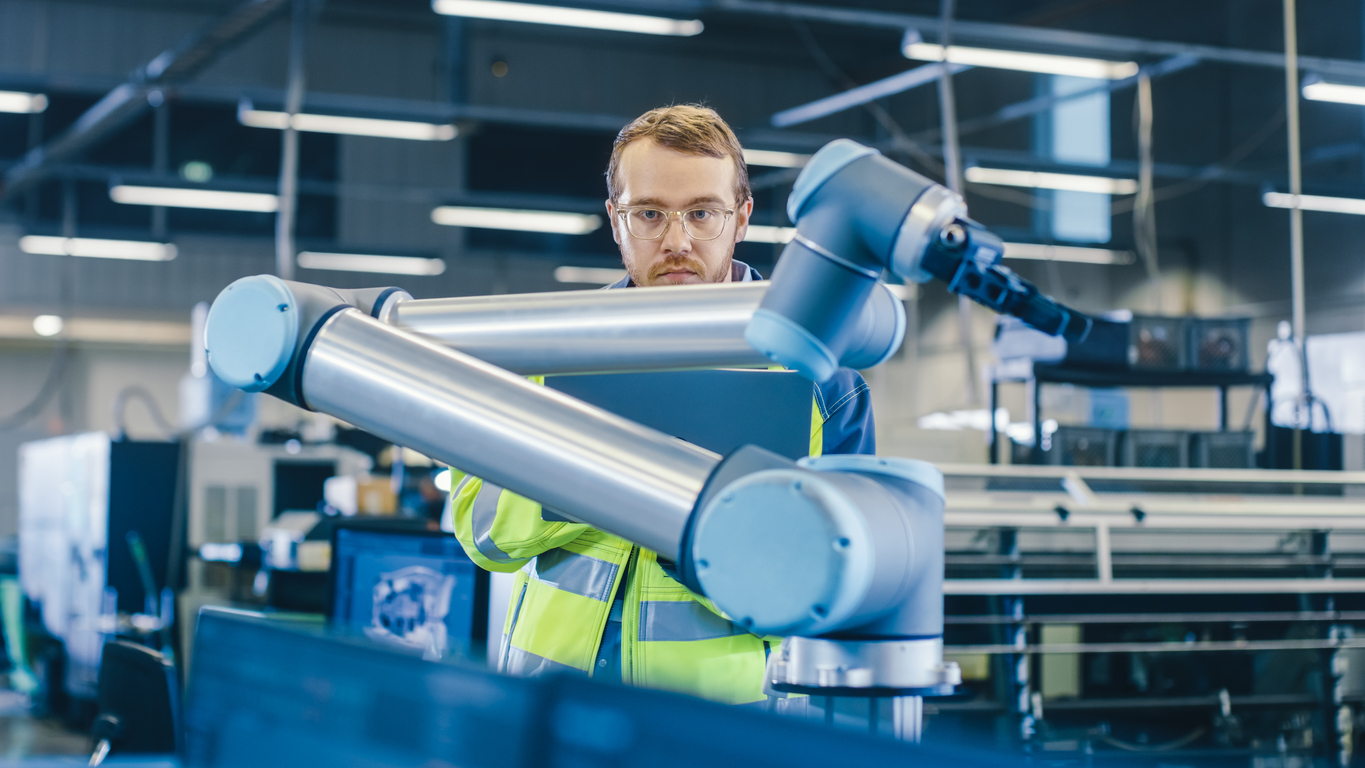
Picture: Getty/iStock
“One of the biggest issues in manufacturing today is the critical mismatch between the actual needs of SMEs and the technologies being sold to them,” says Mark Burletson, managing director of Human Workspace – a process optimisation specialist that combines physical infrastructure with smart manufacturing systems to boost performance.
Mark and his team have seen the pitfalls of vendors presenting narrow, competing visions of smart manufacturing. A vendor insisting their singular solutions are the key to revolutionising tasks frequently backfires. Business owners, dazzled by the pitch, invest in such technologies without a clear strategic plan. As a result, the equipment sits idle, gathering dust because it wasn’t relevant to their needs or broader goals.
More worrying, these failed investments can discourage SMEs from embracing new technologies precisely when doing so is essential for survival. “Few companies can afford to throw money away, yet standing still is simply not an option,” says Mark. “It’s never been more vital to eliminate waste, increase efficiency and become more data-driven. We need to reverse this trend by helping SMEs strategically invest in and leverage the right technologies to stay competitive.
“UK manufacturing stands at a crossroads. Global trends shifting towards localised production and reduced reliance on far-flung supply chains present a unique opportunity for British manufacturers. To seize this moment, factories must become more efficient, innovative and released from everyday distractions.”
From firefighting to future-proofing
The key to achieving this is shifting from quick fixes to proactive, strategic investments. Many small manufacturers, constrained by time and resources, address problems as they arise instead of focusing on long-term solutions.While a quick fix may provide temporary relief, it doesn’t resolve the underlying issue. This reactive mindset not only drains resources and impedes continuous improvement but also exacerbates inefficiencies as managers remain preoccupied with immediate crises.
Human Workspace recognises that any change can be daunting, particularly when it involves new technologies. “Embracing technology change can seem overwhelming, especially for SMEs already stretched thin. However, with the right partners and tools, small manufacturers can become more efficient, increase yields and maximise profit without getting lost in the hype,” explains Mark.
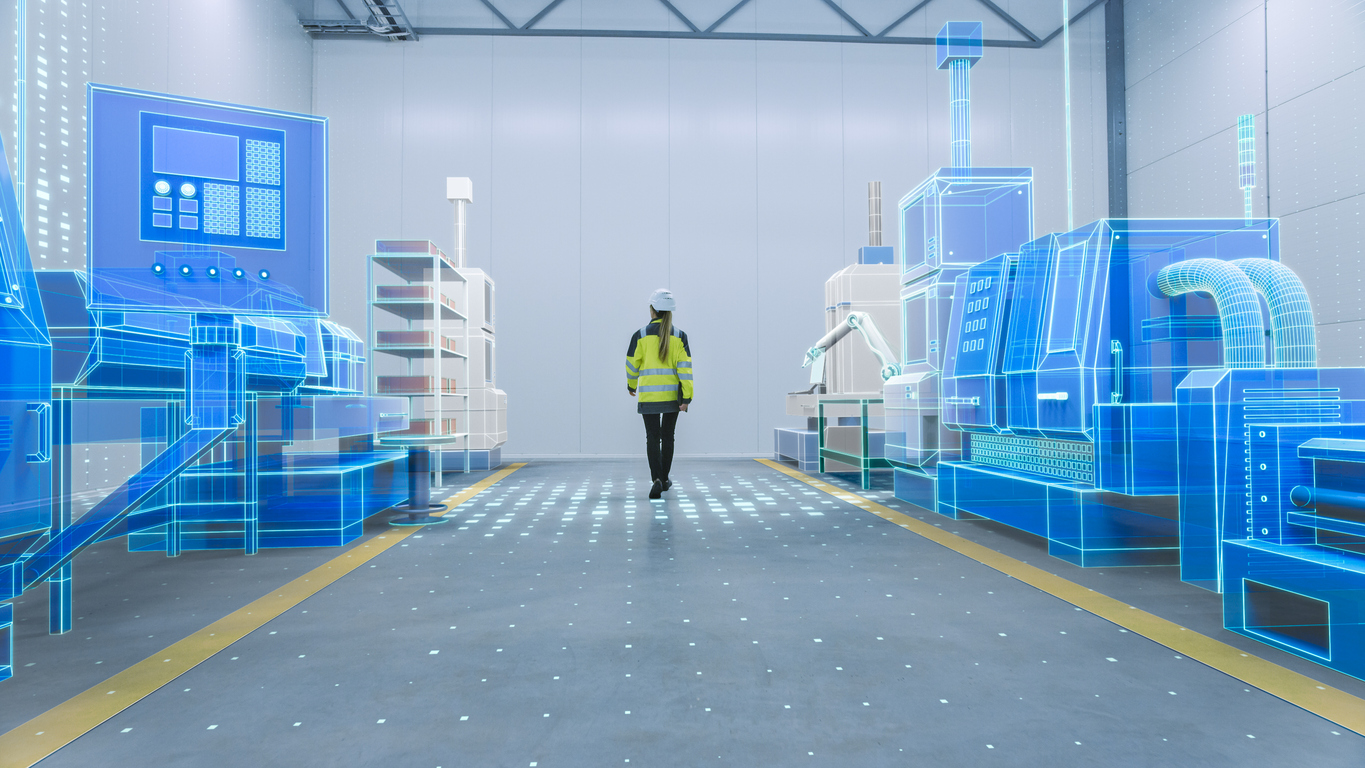
Picture: Getty/iStock
Building on 20 years of experience helping manufacturers optimise their processes, Human Workspace demystifies smart manufacturing and supports SMEs in introducing the systems they need to stay competitive – from ergonomic workspace design and automation to monitoring and control software.
“Every manufacturing facility is different but we see common challenges time and again: a lack of time and resources, a misunderstanding of what’s actually required, and an overwhelming array of options that leave decision-makers paralysed,” says Mark. “What’s needed is a clear, accessible roadmap that addresses these challenges and offers actionable steps tailored to SMEs. We want to ensure decision-makers are as well-informed as possible about the technologies available, what they can do for their business and what’s involved in adopting them.”
A no-nonsense road map
Recognising that most SMEs don’t have the luxury of trial and error, Mark and his team have distilled their extensive experience into a practical, no-nonsense roadmap. This plan offers straightforward, actionable guidance without jargon or hidden fees. It’s freely available and has already proven beneficial to numerous small manufacturers.
The roadmap covers every stage of a successful smart manufacturing journey, starting from understanding your vision, budget planning and gaining buy-in, all the way through assessing readiness, finding use cases, launching pilot projects and scaling proven solutions. At each stage, Human Workspace can assist SMEs in gathering and connecting data, analysing processes, simulating changes and implementing improvements that drive real-world results.
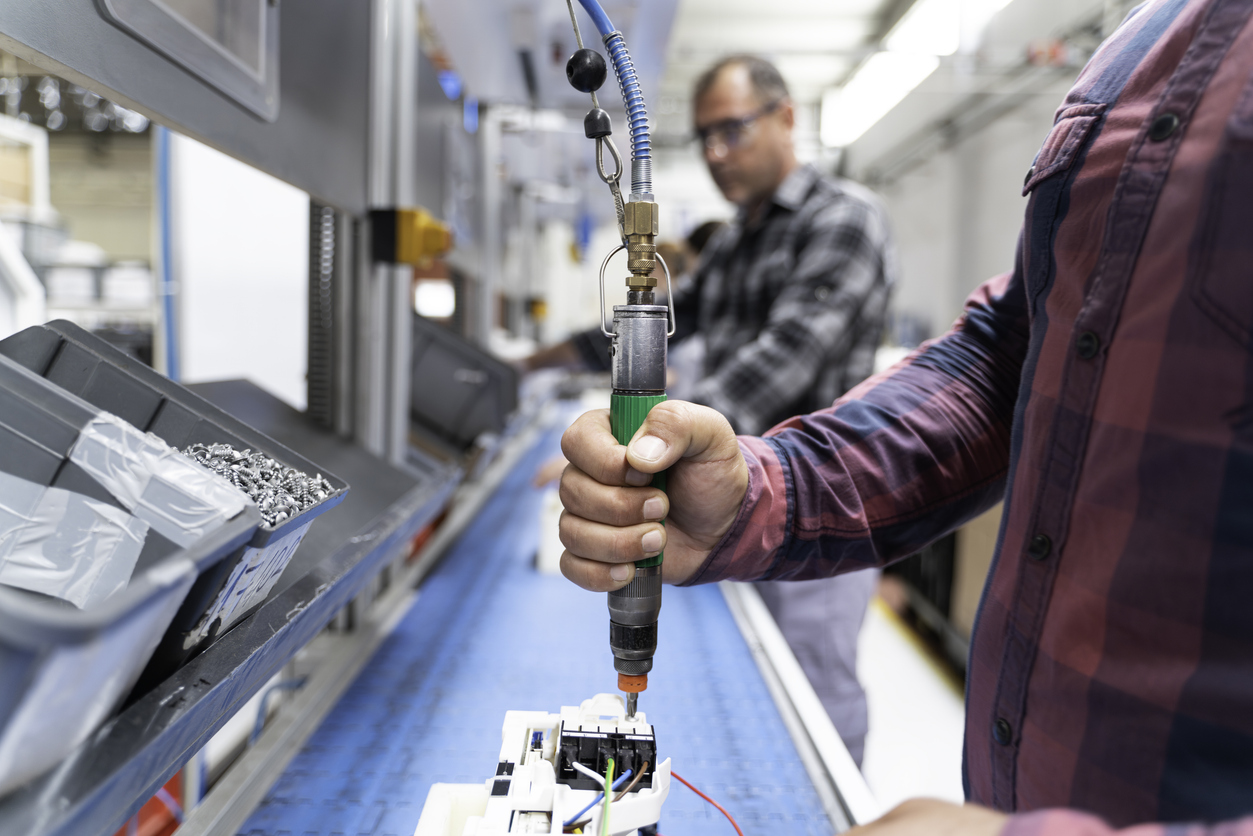
Picture: Getty/iStock
“Technology solutions that were once out of reach for most SMEs are now more affordable and accessible,” says Mark, explaining the timing. “Five years ago, only a small percentage could afford an advanced technology like a cobot [collaborative robot] or automated warehouse. Today, most could consider such solutions, if they’re the right fit.”
Cobots and stores automation are just two aspects of Human Workspace’s ecosystem of trusted suppliers offering proven, compatible solutions. “We work closely with suppliers we trust to connect manufacturers with the right hardware and software for their work environment,” Mark continues.
“From analytics to vision systems, we’ve identified and vetted the best companies in their field, all of whom share our commitment to helping companies get the most out of their workspace. Through our supplier ecosystem and no-nonsense road map, we can act as your guide to the various technologies and tools that are changing the very nature of manufacturing and help you develop a reliable and integrated technology strategy.”
“It’s time for SMEs to address their productivity challenges head-on. For too long, manufacturers have felt trapped by a lack of time, limited resources and an endless list of options,” Mark concludes. “But you’re not alone. Our smart manufacturing roadmap cuts through the confusion, giving you a clear, practical strategy to align your efforts, improve efficiency and make informed decisions that directly impact your bottom line.”