9 minute read • published in partnership with KUKA
Opinion: Automation and robotics in the medical device, pharmaceutical and biotechnology manufacturing sectors
In recent years there has been an upsurge in the deployment of advanced automation and robotics in medical device manufacturing and to a lesser extent in Pharmaceutical and Biotechnology Manufacturing. The Covid-19 Pandemic has only served to highlight how much more work is still needed to safeguard these critical sectors both in terms of continuity of product supply but also in terms of operational work practices. As many of these companies are developing and implementing social distancing work practises, they are also engaging with automation suppliers to plan for the future of their manufacturing and assembly lines in this rapidly changing world. Brian Cooney, General Manager at KUKA Robotics Ireland explore how automation and robotics are set to be key enablers in the post Covid-19 recovery strategies of forward-thinking companies in the Life Science Sector.
In many respects, Ireland has led the way in building up a network of Automation solution providers and machine builders that specifically target these critical sectors, and with the potential that exists in the United Kingdom, particularly Post Covid-19, perhaps now is the time for the UK to take these learnings and apply them for the benefit of the UK Life Science manufacturing sector.
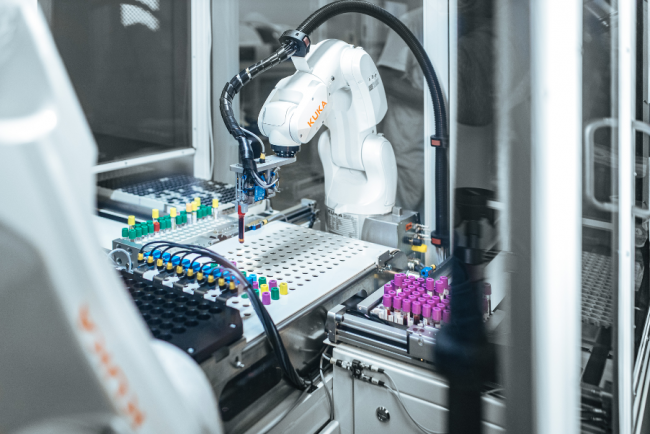
Picture: KUKA Robotics
For many years medical device manufacturing has traditionally been extremely labour intensive, this is due in the main to several factors.
1 – Products are developed by R&D with clinicians and patients in mind, with little or no input by manufacturing engineers on how to scale up manufacture should the product launch be successful, thus automation becomes difficult and the default position is to increase the labour content to cope with the increase in demand.
2 – Profit margins on successful products tend to be very high and well protected by Patents so utilising large amounts of labour has not been a major barrier.
3 – Many countries offer supportive grant aid often closely linked to numbers of people employed.
Primary Pharmaceutical and Biotech manufacturers product tend to be shipped as bulk active ingredients and up to now, outside of plant (DCS) and skid mount (PLC) process control, those manufacturers have shown little interest in automation and robotics. Secondary Pharmaceutical manufacturing is the exception and is well automated in areas such as tableting, vial/bottle filling, leaflet insertion, packing and palletising.
However, more recently there have been many changes to the Medical Device market that have accelerated the use of automation and robotics in this manufacturing sector, including Patent expiry with resultant competition from lower cost countries, falling margins as a result of increased competition, the ever increasing cost of cleanroom real estate and increased competition from competing foreign countries, establishing their own Life science clusters with attractive subsidies for both indigenous and multinational companies.
Mergers and acquisitions among many of the world’s leading manufacturers has also increased internal competition for new product lines making competitiveness ever more important.
These factors, individually or as a collective, have all acted as a catalyst for Life Science manufacturers to review their manufacturing processes and begin their automation journey.
Modern Manufacturing Trends
R&D engineers now engage with their manufacturing engineers from the get-go of product development to ensure that should the product receive regulatory approval and a successful product launch, it can be manufactured and scaled up efficiently and cost effectively.
New production lines are designed to maximise efficiency while minimising footprint thus reducing the cost of cleanroom facilities. Workflow optimisation and reduction of material handling is of paramount importance both to eliminate unnecessary transportation and storage between production stages but also to reduce the levels of human to product contact.
Even in primary pharmaceutical and Biotech manufacturing there has been an increasing awareness of the need to introduce greater levels of Automation and Robotics. Many companies have been looking at means to release highly paid chemists and biotechnologists from mundane nonvalue added tasks such as environmental and product sampling, kitting and to improve the safety for their employees when handling particularly potent, hazardous and toxic chemicals. It is widely accepted that in Biotechnology Manufacturing, as much as 35 -50% of the operating cost is in manual labour.
Additionally, the use of automated robotics laboratories and seed laboratories as well as in warehousing and logistics hold significant potential for improved efficiency and product traceability.
Advances in Technology
Once seen as the stalwart partner of the Automotive, metal fabrication and consumer goods industries with little change in the technology for many years, robotics has really come of age for a new generation of Smart Manufacturing in Life Science Manufacturing.
Small, fast, cleanroom specification robots, sensitive, dexterous Collaborative robots, Autonomous guided robots, Artificial learning and Advanced Vision all combine to provide the necessary technologies to facilitate the widespread rollout of automation across both new product introduction and legacy products.
Data management and product traceability becomes easier to manage with automated and validated manufacturing lines enabling secure audit trails and compliance with the regulatory standards.
It is also worth noting that in addition to our focus on providing robot solutions for the Medical Device, Pharmaceutical and Biotechnology sectors, KUKA have a dedicated Medical Robotics Division specifically for Medical and Operating Theatre robots.
KUKA have recently received the prestigious “Global Company of the Year” Award 2020 for its Medical Robotics division
“Unique, progressive, valuable: The consulting company Frost & Sullivan analysed the medical robotics market, and in doing so recognises KUKA’s LBR Med as one of the most advanced robots in the industry. For the robot and its innovative achievements in the field of medical robotics as a whole, KUKA has received the ‘Company of the Year’ award from Frost & Sullivan.”
The medical robot is the first robot certified for integration into a medical device. It is specially adapted to medical requirements and is used in very different applications such as diagnosis, rehabilitation, aesthetic surgery, or medical treatment in the operating room. Due to the spectrum of possible applications in the demanding field of medical technology, Frost & Sullivan considers the LBR Med to be one of the most advanced robots on the market.
This will evidently be yet another growth market post covid-19 as direct contact is minimised as much as possible.
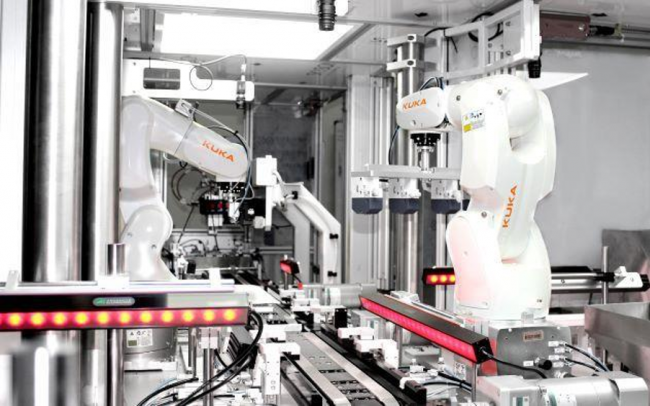
Picture: KUKA Robotics
Leading Adopters
In the Life Sciences sector, several global companies such as Abbott, J&J, Boston Scientific, Medtronic, Hollister and others are seen as the leading adopters of Automation and Robotics and by the nature of the global concentrations of these companies it is natural that robot manufacturers in some countries have a more focused approach to the Life Sciences market.
Ireland is home to 9 out of the worlds top 10 Medical device companies and more than 300 companies in the MedTech sector. KUKA recognised the potential in this market very early on and is one of the most established suppliers of robots into the sector with a strong and loyal Machine Builder System Partner network throughout the country with extensive knowledge of automation, control, vision, robotics and critically the regulatory framework within which the end customer and suppliers must work and conform to.
Similarly, 10 of the top 10 Biotechnology companies in the world have manufacturing plants here and more than 70 pharmaceutical companies also operate in Ireland with several ongoing research projects in sector specific robotic applications in conjunction with Universities, EPC’s and end users ongoing. Many leading global Biotechnology companies had already come together under BPOG (Biophorum Operations Group) to lay out their technology roadmap with significant focus on Automation and Robotics for the future of their industry.
Ireland has been particularly progressive in developing its Life Science clusters with a highly educated, English speaking workforce and excellent University and R&D support system, however Ireland is not unique in this respect and the learnings from Ireland can well be applied elsewhere.
Covid-19 and the New Norm for Manufacturing
If ever an unfortunate event proved to remind us that an over reliance on scarce manual resources and impractical overcrowded working conditions is unsustainable for the security of our supply chain and survival of our manufacturing industries, the Covid-19 Pandemic has just surpassed it.
When, eventually, our manufacturing sectors can return to work, the landscape will have completely changed. We must maintain social distancing within the workplace for the foreseeable future or until a Vaccine is rolled out across the globe, even then, social distancing within the workplace may become the “New Norm”. This will be just as applicable to the Life Science Manufacturing Sector as to other sectors.
Critical finished good manufacturing and supply chain has come under scrutiny during this pandemic and many of the flaws in low cost manufacturing in far flung continents has come to the fore with serious shortages in finished goods and raw materials arising. As a result, reshoring of manufacturing is inevitable with many countries governments already issuing policy statements encouraging companies to reshore their manufacturing and supply chain with several countries already offering substantial financial enticements for companies to do so, however while this will undoubtedly be welcome news, cost competitiveness will be even more important, and automation and robotics is fundamental to maintaining cost competitiveness.
Automation and Robotics is also set to become the “New Norm” with increased focus on reducing the concentrations of workers in close proximity to one another and providing continuity of production even in the event of another major interruption to manufacturing and supply chain.
Sensitive and dexterous Collaborative robots with small footprints will increasingly become our “Co-Workers”.
Research will be accelerated to develop “new” applications for robotics, faster deployment, flexible and easy to use.
Autonomous mobile robotics will become commonplace, not only in warehousing and logistics but also in testing, sampling and media preparation.
Cleanliness and hygiene will take on a whole new importance in the workplace and while automated robotic sanitising in hospital environments is in early development, it may become necessary to consider similar technologies in manufacturing facilities.
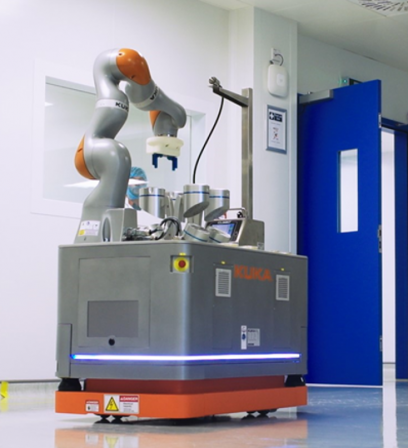
Picture: KUKA Robotics
Challenges
There are many challenges to be overcome in this “New Norm” which requires collaboration and initiatives across all invested parties including the End User, Regulatory Authorities (eg ISO/FDA), Government Bodies, Research Institutions, Universities, Machine Builders and Automation/Robot Suppliers, including but not limited to,
• Funded research, essential to develop new technologies.
• Skills Gap, already a critical shortage exists of automation and robotics engineers across a range of skills levels from apprentice to Master’s degree. This needs urgent addressing across our educational facilities, both for skilling and reskilling.
• Workplace culture and operator acceptance of robot technology
• Brownfield Plant Design is not always suited to deployment of automation, for the deployment of mobile robotics
• Government investment support programs, particularly for smaller manufacturing companies and solution providers
• Agile Innovation funding
• Working capital loan schemes
In summary, Covid-19 is wreaking pain and suffering on our families, communities, individuals, health services and the world economies, but the impact does stop there. Our entire way of doing business, working, communicating, commuting, socialising has already changed and much of that change is here to stay.
Manufacturing will have to adapt and change or disappear by failing to do so. It will no longer be acceptable for crowded working conditions with high risk of disease transmission to continue, automation and robotics is a key enabler to minimise overcrowding and establish clearly defined workspace and task separation in compliance with social distancing regulations.
Reshoring will be a welcome boost to many suffering economies, but it should be remembered that offshoring in the first place was a means to reduce costs and manufacture cheaper goods, so cost competitiveness utilising automation and robotics is critical to the success of any reshoring program.
There are many challenges facing manufacturing as economies try to get back to some degree of stability post Covid-19, financial constraints, changes to working environments, cultural change and acceptance, skill gaps and market changes to name a few, these challenges apply equally to the Life Science sector and for many companies this will require a step-change in how they design and manufacture their goods under the new manufacturing norm and Automation and Robotics is set to be centre stage of the changes.