7 minute read • published in partnership with PP Control & Automation
The talent gap and leadership transformation should urge UK manufacturers to rethink strategies
Malcolm Condon, HR people partner at PP Control and Automation (PP C&A), is a firm believer that, in order for UK manufacturers to remain competitive, they will need to rethink strategies for bridging the talent gap and transforming leadership. Zenoot finds out more…
On one hand, the UK manufacturing sector is grappling with significant skills shortages, a challenge that has only been exacerbated by rapid technological changes. On the other, the need for dynamic leadership to guide companies through periods of disruption and innovation is more pressing than ever.
This ‘talent gap’ represents a dual challenge for companies – attracting and retaining skilled workers, whilst cultivating a new generation of leaders who can embrace digitalisation and sustainability.
The growing talent crisis
The skills crisis in the UK manufacturing sector is no secret. According to Make UK’s annual report, the sector currently supports 2.6 million jobs and contributed £217 billion to the economy in 2023, but a significant portion of its workforce is nearing retirement age.
This has led to widespread concerns about the availability of skilled workers, with the added emphasis on attracting talent in technical areas such as automation, advanced manufacturing, and AI integration. A worrying scenario that is further complicated by the rapid evolution of manufacturing technologies, which require a different skill set than those traditionally associated with the industry.
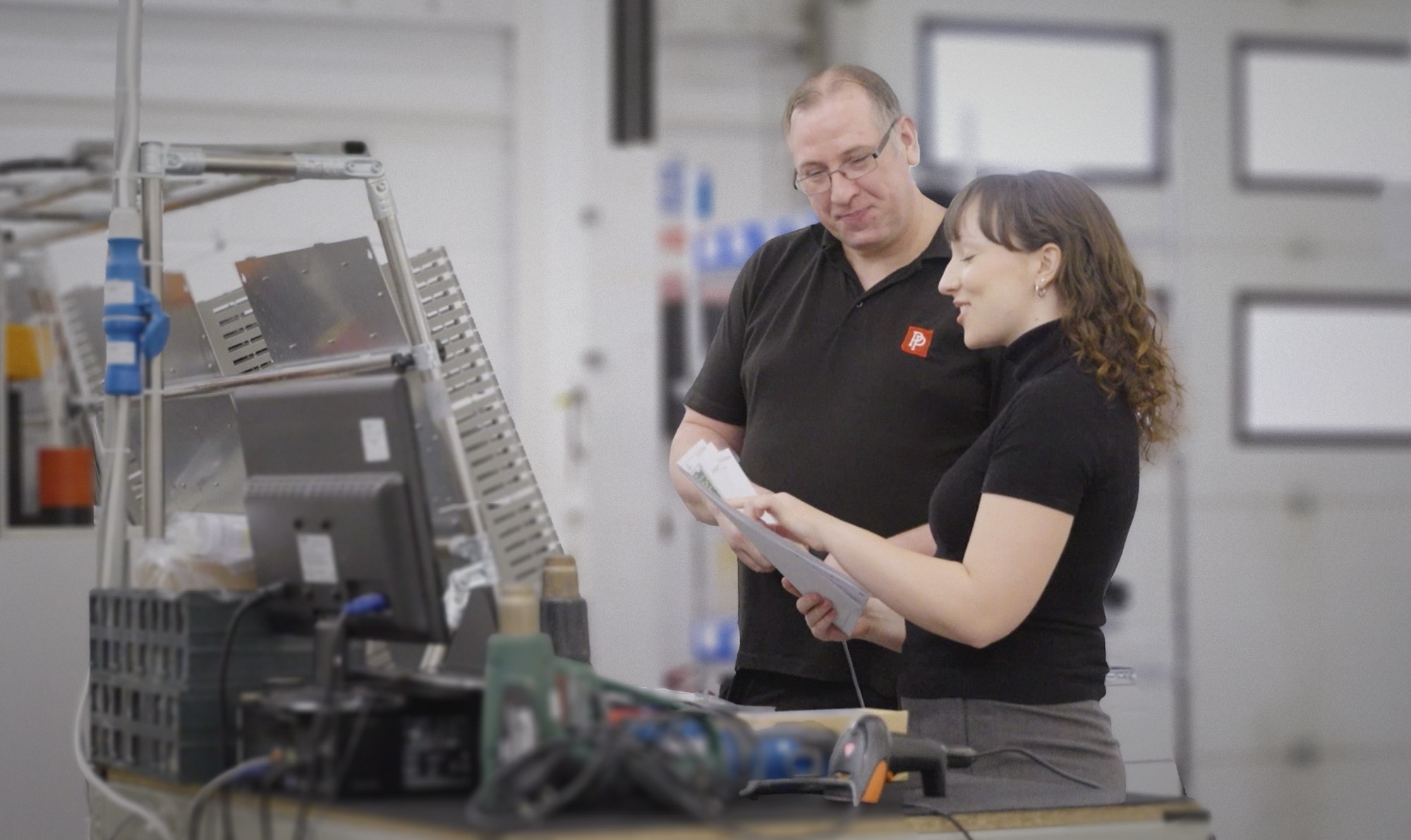
Picture: PP Control & Automation
Automation, robotics, and artificial intelligence (AI) have become synonymous with modern industry, but the workforce has struggled to keep pace with innovation. A 2024 report by Berwick Partners highlights how this transition is leading to acute shortages of talent, particularly in leadership positions.
Additionally, the manufacturing sector has not always been successful in attracting younger workers. Many up-and-coming professionals view manufacturing as a traditional, labour-intensive field, when, in reality, it offers exciting opportunities in fields like digital engineering, data science, and smart factory management.
And not only that, but we must also attract a much more eco-conscious generation, so we should be promoting the need for the skills that will bolster our emerging markets and technologies, technologies that are answering some of the world’s biggest questions – how do we generate energy? How do we move around? How do we grow produce? How do we design circularity? Changing perceptions and promoting our emerging landscape is essential if the sector is to bridge its talent gap and future-proof its workforce.
Leadership in transition
The leadership gap in UK manufacturing is as stark as the skills shortage. Moving from legacy to digital pioneers, it is clear that a new generation of leaders is needed to guide the sector through its next phase of growth.
However, the transition to digital-first leadership has proven slow. Traditionally, industry bosses have risen through the ranks based on technical expertise or operational management skills. Whilst these qualities are still extremely valuable, today’s leaders must also be adept at strategic thinking, digital transformation, and managing the imperatives of ESG and innovation.
Succession management has become a major theme, with many companies recognising the need for fresh leadership perspectives. According to Berwick Partners, a wave of new talent is slowly taking leadership roles, bringing with them a revitalised focus on innovation and sustainability. However, these transitions are not happening at the same pace as the scale of change we are seeing on the ground.
Many current manufacturing leaders grew their careers in an era when operational efficiency and cost control were the primary markers of success. Whilst these qualities remain important, today’s manufacturing landscape requires leaders who are comfortable navigating the complexities of Industry 4.0, sustainable manufacturing practices, and digital integration. Without this shift, the sector risks falling further behind in an increasingly competitive global market.
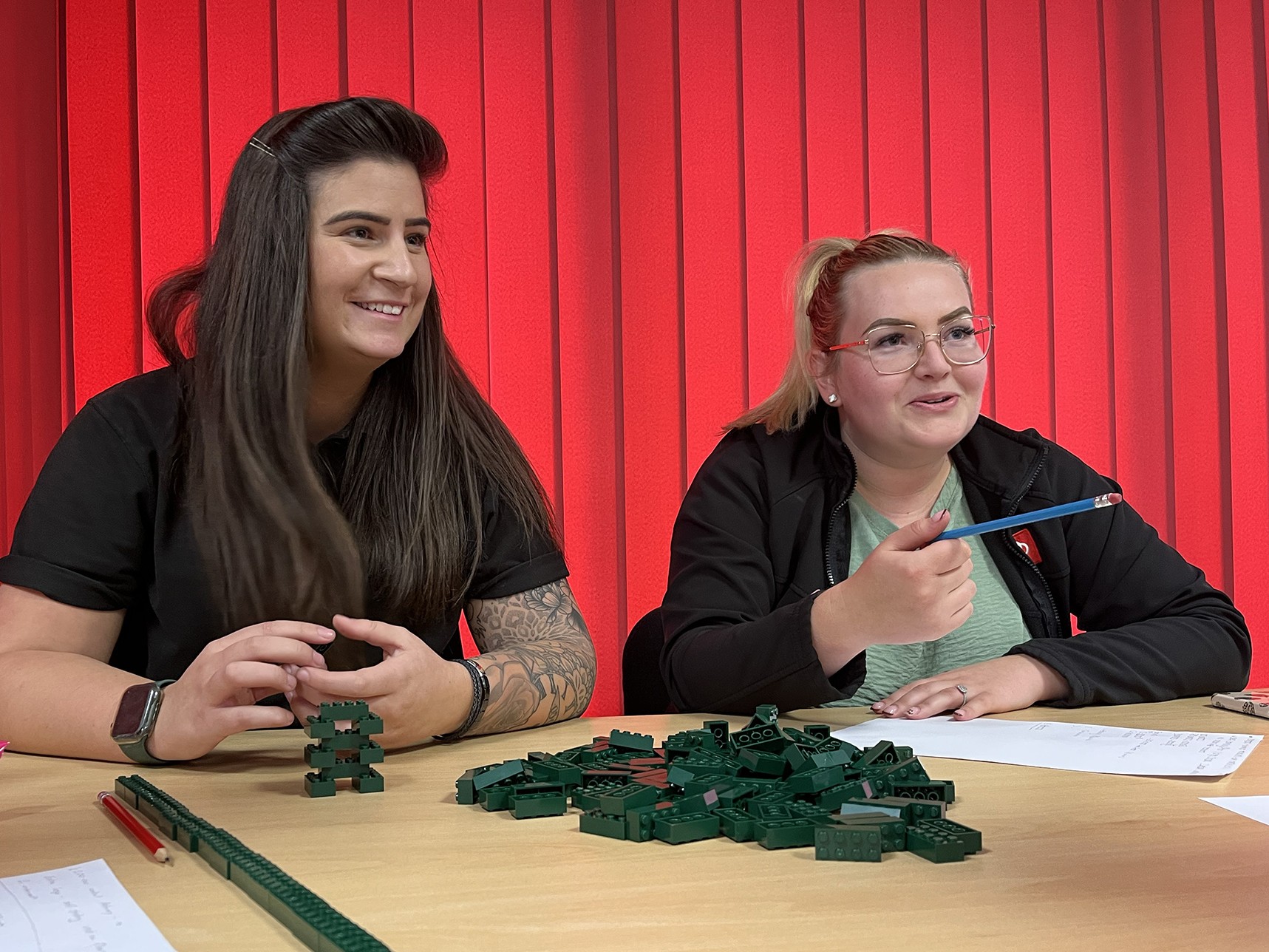
Picture: PP Control & Automation
Upskilling and diversifying
To address both the talent and leadership gaps, UK manufacturers must rethink how they approach upskilling and leadership development. Several strategies can help address these issues.
Digital literacy and proficiency in new manufacturing technologies, such as AI, machine learning, and advanced automation, should be at the forefront of training programmes. This can be done through partnerships with educational institutions, offering apprenticeship schemes, and on-the-job training that focuses on digital competencies.
We’re tackling challenges like these currently at PP C&A. With the growth we have experienced in recent years, we now employ around 200 people at our facility in Cheslyn Hay, each one of them an important cog in how we continually meet the daily requirements of 20+ of the world’s largest machinery builders.
But how do we retain these skills with the volatility of the labour market and competition from major employers nearby, such as JLR, JCB and Collins Aerospace? We always prefer a proactive approach to difficult situations, and this is no different. Rather than hope for the best like so many firms do, we have one of industry’s most progressive cultures that places personal development, wellbeing and creativity at its heart.
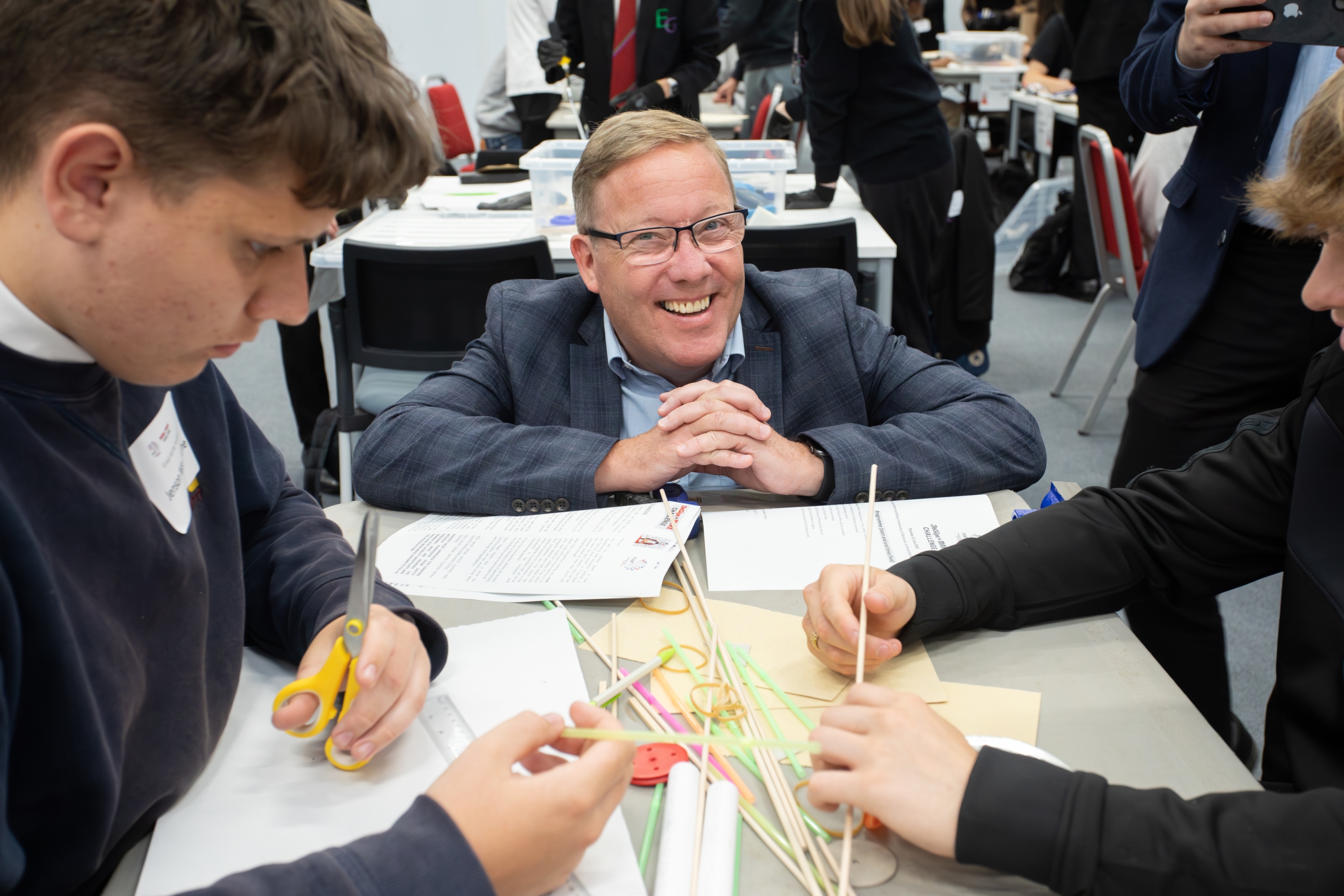
Picture: PP Control & Automation
Something that has stuck with me since joining the business is something I heard from our CEO, a firm believer in getting the most out of people. He always refers to one of his favourite sayings when asked if some of the money we invest in people is wasted when they leave. The stock response is ‘well what happens if we didn’t train them, and they stayed?’
It certainly makes sense the more you think about it and perhaps explains why so much importance is placed on Bright Sparks, our in-house training school. This is designed to ignite the flames of curiosity and empower people to embrace lifelong learning by developing technical expertise and leadership skills through a combination of online learning, external courses and on-the-job shadowing. We didn’t stop there, quickly introducing Bright Sparks University that champions diverse learning pathways, technical excellence, leadership and continuous improvement.
There has been government support too. For example, the launch of initiatives like the Green Industries Growth Accelerator (GIGA), which aims to support the development of low-carbon manufacturing skills, and the Aerospace Technology Institute (ATI), which provides funding for R&D projects and skills development in aerospace.
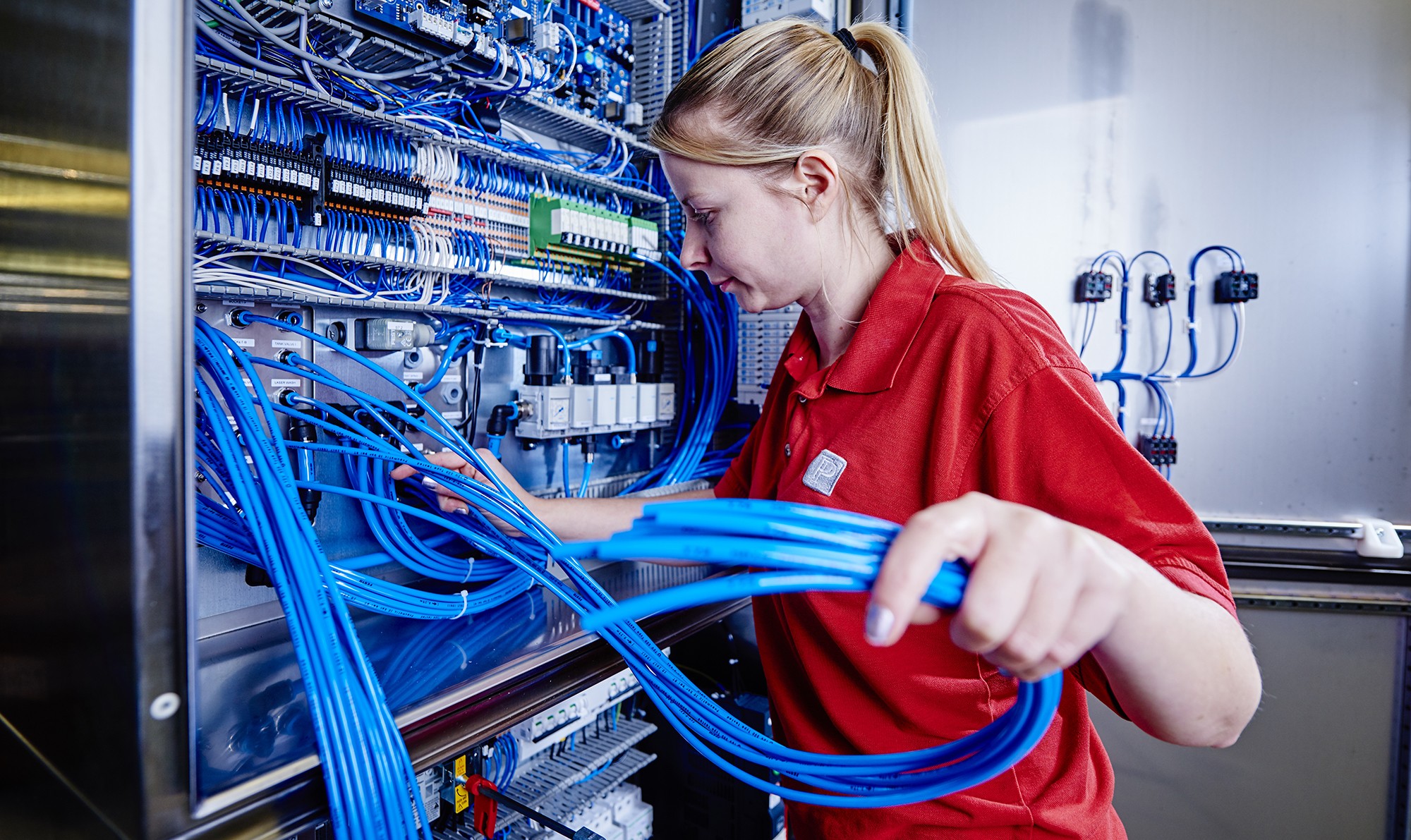
Picture: PP Control & Automation
Apprenticeships remain one of the most effective ways to develop skills in manufacturing. A study from PwC emphasises that investing in young talent through apprenticeships, particularly in advanced manufacturing roles such as electrical engineers, robotics engineers, AI technicians, and data analysts, will be key to solving the talent shortage.
We should also be acutely aware of diversity, equity, and inclusion (DEI). In leadership, it is being cited as a social imperative and business necessity. Research consistently shows that diverse teams outperform their less diverse counterparts, particularly when it comes to innovation and problem-solving. Manufacturing leadership remains largely homogeneous, and this lack of diversity can limit the sector’s ability to innovate and adapt.
Companies need to actively recruit leaders from diverse backgrounds, particularly those who bring new perspectives on technology, sustainability, and business strategy. This might involve looking beyond traditional talent pools to attract leaders from adjacent industries, such as technology or data-driven sectors, where skills in AI, digital transformation, and data analytics are more prevalent and already attained.
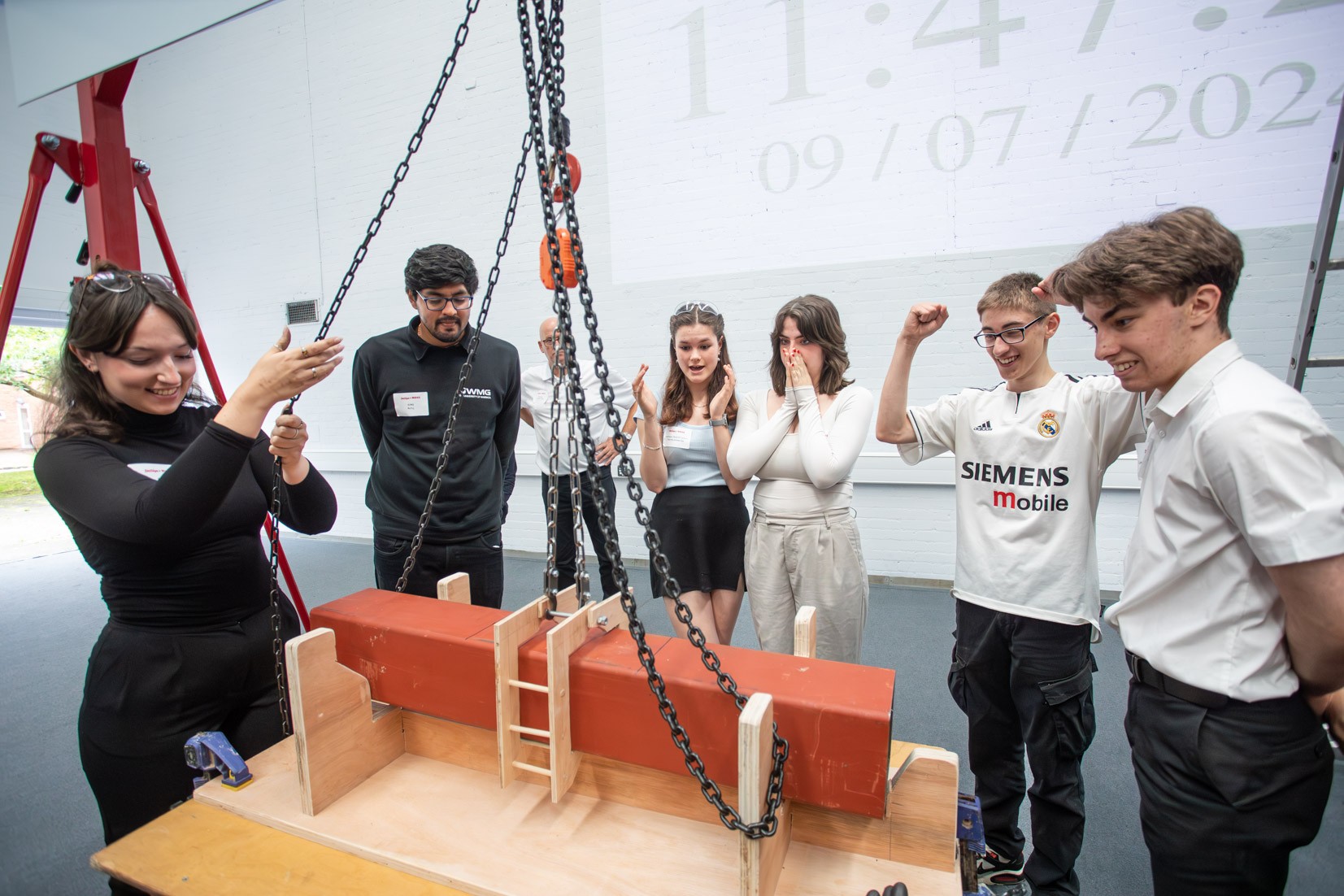
Picture: PP Control & Automation
No one of us is better than all of us
Leadership in manufacturing needs to move beyond traditional top-down management styles and cultivate an environment where innovation is encouraged at all levels of the organisation.
This is something embedded into the core values of PP C&A and requires a shift in leadership philosophy, from command-and-control structures to collaborative and inclusive approaches that empower teams to innovate and give them the frameworks to engage easily in continuous improvement.
Manufacturers should also encourage cross-disciplinary collaboration, bringing together teams from engineering, IT, HR, operations, and marketing to solve complex challenges. Leaders should act as facilitators of innovation, creating the conditions in which new ideas can thrive. In our experience, collaboration is also a proven approach to attracting the next generation of engineers. Alongside our Manufacturing Assembly Network (MAN) partners, we’ve launched one of the largest STEM events in the country.
Design & Make Challenge is an annual event and in 2024 we attracted nearly 100 pupils from 15 schools. Year 10, Year 11 and Year 12 students split up into teams of four to design, test and build a solution to a new problem each year, working closely with apprentices from the eight MAN companies and graduate engineers from WMG’s SME Group.
You can see firsthand how our young attendees respond to the event, and it is heartwarming to see that we’re having an impact on how the next generation’s perception of manufacturing shifts, and equally, how we’re giving them pause for thought on the career paths they can take.
One of the apprentices on hand at the event was our very own Sophie Young, and I see her as an excellent role model for how apprentices today can influence the ones of tomorrow. She has picked up several industry awards during her time at PP C&A and is also actively taking part in industry events, school visits, and keynote addresses to play out her success story and express her excitement for a future in manufacturing.
Sophie’s latest keynote was part of an event hosted by the newly formed Future of Work, an organisation who have designed a series of conferences that seek to educate parents, teachers, students and careers advisors on roles in industry. Again, evidence that there are lots of people doing positive work to engage new talent.
Address the twin challenges now
The future of UK manufacturing depends on its ability to address the twin challenges of the talent gap and leadership transformation. It is no longer enough to simply manage manufacturing operations efficiently. The next generation of engineers and leaders must be visionary, tech-savvy, and committed to sustainability.
In doing so, they will create a manufacturing sector that is not just resilient, but one that thrives in the face of global competition, technological disruption, and environmental challenges.
For UK manufacturers, the talent gap has been a wake-up call – but also, I believe, an excellent opportunity to redefine what industry will look like in years to come.