4 minute read • published in partnership with CQM Training & Consultancy
Your guide to choosing the best lean six sigma training for your business
Choosing the right Lean Six Sigma or Continuous Improvement training for your organisation requires careful consideration of various factors. After all, you are investing time and money into individual and organisational development. The same thought process is applicable for individuals considering Lean Six Sigma training too. CQM Training & Consultancy looks at five things your should consider.
To help you decide we have created a simple, five step guide to choosing the right Lean Six Sigma training.
1 – Assess Your Needs
• Identify the specific goals and objectives you have for implementing Lean Six Sigma/Continuous Improvement in your organisation. To reaffirm your thought process why not visit our recent “What is Lean Six Sigma and its importance” blog.
• Determine the level of training needed for the individuals and what the organisation is trying to achieve. This might be basic lean awareness, or a specific area such as 5S or value stream mapping. It could also be more comprehensive with yellow belt, green belt, black belt, or master black belt (or a combination).
• Identify your preferred route – funded apprenticeships or commercial training.
• Do you have the necessary structure and support from key stakeholders? Can you embed the learning to continue to drive results afterwards?
• Consider whether you prefer face to face in-house training, virtual delivery or a combination. If you have smaller numbers have you considered what options are out there?
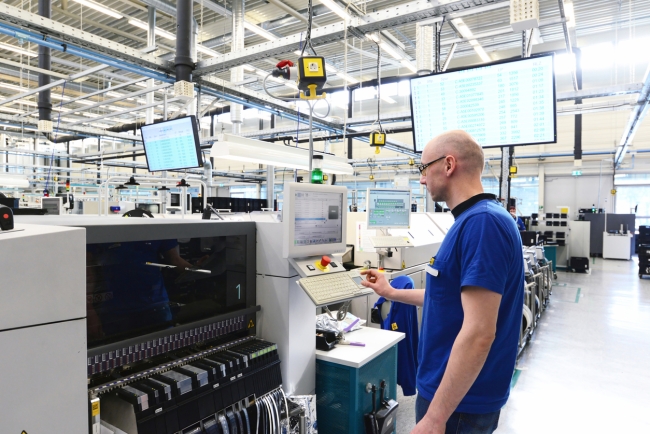
Choosing the right training provider is important to the long-term success of your lean six sigma or continuous improvement projects / Picture: Getty/iStock
2 – Research Training Providers
• Look for reputable training providers that offer Lean Six Sigma courses. As an example, you could download the apprenticeship provider and assessment register (APAR) here.
• Consider the price and length of the course versus what you expect to get back in return. Note online short courses will not provide the in-depth knowledge, practical application and wider embedding of behaviours that will generate the true returns Lean Six Sigma can create.
• Check for the provider’s pedigree by looking at recent reviews and success stories. These are a good barometer for successful outcomes and how they work with organisations just like yours.
• Make sure you check the awarding body for any accreditation. Here are a couple of examples of well-known and respected accreditors. Instructus Skills and IASSC (International Association for Six Sigma Certification).
3 – Organisational Fit
• If looking at in-house delivery to larger groups, consider how it can be tailored to suit your organisation and people. It should incorporate relevant examples, values and terminology as a flexible approach to suit your organisation and individual needs.
• If looking at an open programme, for individuals or smaller groups, consider the types of similar organisations that have used this method of delivery and the outcomes. This is also useful when considering the benefits of networking and sharing best practice.
4 – Programme Content and Delivery
• Consider the format of training that best suits your organisation and individual needs. The best options include in-person workshops, online instructor-led training, or a combination. Self-paced online options tend to be light on theory and do not provide practical elements that are required for genuine accreditation.
• Review the content of the training programme so you understand what is going to be delivered. This should be available for you to review. Don’t be afraid to ask to speak with the experts if you’re unsure of anything, as it is important you understand what is involved in the training and the expected outcomes.
• Verify the qualifications and experience of the tutors who will be delivering the training. They should have a solid background in Lean Six Sigma and practical industry experience as well as being a qualified trainer.
5 – Cost and Return on Investment
• Compare the costs of different training programmes, keeping in mind the potential return on investment (ROI) from improved processes and reduced waste.
• Training should provide a tangible return on investment, so consider how this will be demonstrated. Individual and group projects should be very clear in their outcomes, such as in a comprehensive report or profit improvement plan.
• Consider how the learning will be embedded post programme, through continuous improvement, innovation and advocacy. Are you trying to build a wider company culture that embraces this, and how does that feed into talent management and progression.