4 minute read
Additive Manufacturing: It’s all about the chemistry
Ahead of his presentation at Additive International, Virginia Tech’s Christopher Williams talks about concurrent design of materials and additive manufacturing processes and how chemists and mechanical engineers are developing the next generation of printable materials for electronics and space applications.
When it comes to geometric topology and the material composition of products, additive manufacturing provides greater design freedom than other, more traditional manufacturing technologies. It is this freedom that is helping to drive multi-material and multi-functional AM. In spite of these capabilities, AM is still being held back by working with polymers that were created for older processes, such as casting and injection moulding. To fully realise the potential of AM, we need to advance the materials selection and tailor processes specifically for additive.
Just as designers are starting to design more and more with AM in mind from the start of the process, we need to create materials that are specific to AM. We need to be thinking about the 3D printing process from the beginning, matching the chemistry of the materials we use to the kinetics and physics constraints of the additive process. Design for AM needs to be as much about designing materials for printing as it does for geometry.
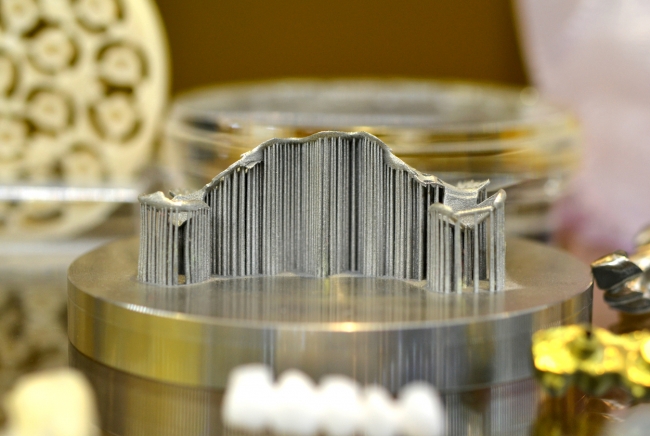
To fully realise the potential of AM, we need to advance the materials selection and tailor processes specifically for additive / Picture: Getty/iStock
Concurrent design: from molecules to manufacturing
This is where the chemistry comes in. As a mechanical engineer, I could only get so far in expanding the materials catalogue to help drive AM to reach its full potential. What I needed was a chemist – someone who understood how to develop materials that could function at higher temperatures, as an example. By putting chemists and mechanical engineers in the same room, you can truly explore the idea of concurrent design of materials, process, and topology, resulting in a huge opportunity to cover the full spectrum of what AM can achieve.
With this in mind, I reached out to an expert in polymer chemistry on campus and we combined our areas of expertise – designing for AM from the beginning, together. We started working on concurrent design: designing the macro molecules for materials, the printer and specific parts all at the same time. We call it ‘molecules to manufacturing’ and the process is making it possible to expand the AM materials catalogue and the processes’ capabilities along with it.
For example, using this principle we were about to find a way to print Kapton, a polyimide known in the electronic and aerospace industries as able to tolerate extreme temperatures (up to 605 degrees C) without degrading. Kapton is also very resistant to chemicals and radiation, which is essential for use on satellites. Previously, it was only available as a film, but we were able to modify it and use it to print 3D structures – opening up a raft of opportunities for use in high temperature polymer components such as 3D printed electronics and structural aerospace applications.
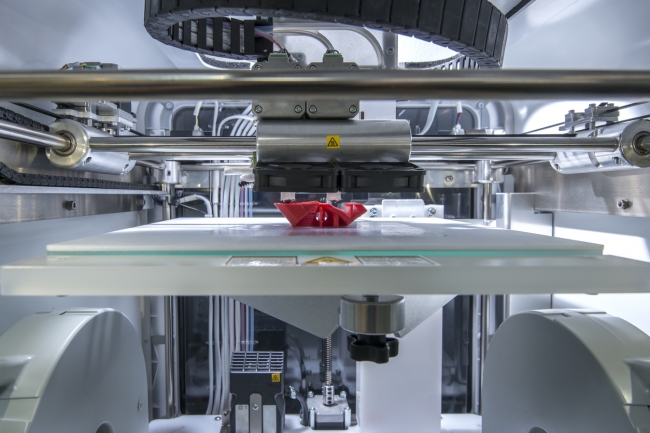
Virginia Tech’s Christopher Williams will be speaking at this year’s Additive International event taking place 10-12 July / Picture: Getty/iStock
A second example of successful concurrent design applications is in the area of drug delivery. We were able to design a material that can be printed at low temperatures and can rapidly dissolve in water. This means that active ingredients in drugs can survive the printing process. We also designed a machine to print at a lower temperature to protect the active ingredients – illustrating that by designing the material, machine and product (the pills themselves) at the same time, we can control and improve the drug delivery process using AM.
From research labs to real world applications
While these examples both took place in controlled laboratories, new materials and concurrent design for AM is not as far away from real world applications as you may think. Businesses are recognising that commercially available materials aren’t meeting their needs and that investment is required to fuel new processes and new chemistry applications to change this.
Both projects were funded through industry partnerships and we’re seeing a lot of businesses interested in how AM can help them, learning that AM can disrupt their current business and manufacturing processes in a positive way, ultimately improving material quality and performance.
You can find out more on the speaker lineup at Additive International by following the link below