3 minute read
Case Study: All types of bodywork repaired as new
When a car is involved in a violent impact, the first concern is obviously for the safety of its passengers. However, after the initial scare, the focus inevitably shifts to the car itself. It is hoped that it can also be restored to its former condition, with the same aesthetic and functional characteristics as when it was brand new from the factory.
This is where Spanesi – one of the world’s leading companies specialized in providing a comprehensive range of equipment and tools for automotive repair shops – comes into its own. One of the key products Spanesi offers is Touch, an electronic measuring instrument with geometric coordinates used by repair shops to verify that the body and structural parts of the repaired vehicle are within the tolerance limits specified by the manufacturer so that they can continue to guarantee its safety on the road, just as when the vehicle was new.
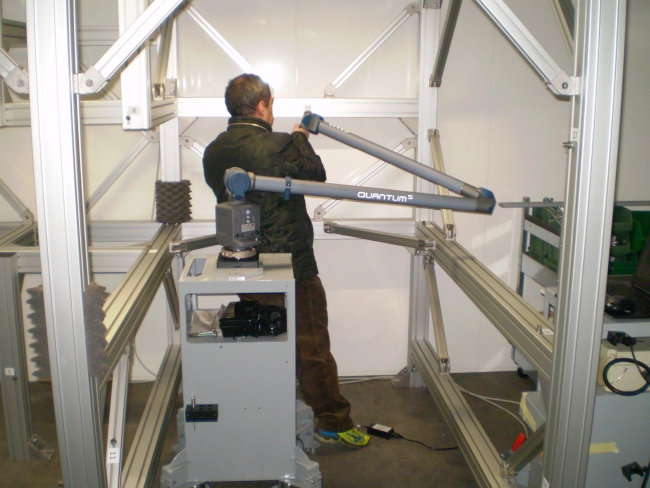
Spanesi has reduced the calibration time of its bodywork measuring instrument Touch from 4 hours to just 30 minutes using the FARO QuantumS Arm and CAM2 Measure 10 / Picture: FARO
Spanesi certifies the quality and accuracy of its measuring instruments as required by ISO 10360, but the traditional calibration procedure used to comply with the criteria laid down by the standards was quite long and laborious, before adopting an innovative solution using the FARO QuantumS Arm.
Andrea Siviero, Data Quality Controller at Spanesi, said: “To ensure the accuracy of our measuring instruments, we used a factory calibration procedure based on gauge blocks. Although sufficient to ensure compliance with regulations and the necessary accuracy characteristics, it was a very laborious and time-consuming process as it took about half a day to obtain the approximately 1,400 measurement points with gauges and process the results. Producing on average around 800 measuring instruments a year, this involved a significant effort, so we created a completely new calibration procedure, setting two objectives: to drastically reduce the time required for calibration and to expand the calibrated geometric space, extending it beyond the approximately 1.5 m we obtained using the gauge blocks.”
The Spanesi development team designed an innovative solution consisting of a cage-shaped aluminium structure with dimensions similar to those of a typical car, mounted with 18 fixed reference cones. The absolute coordinates of the 18 reference points mounted on the cage are measured by Spanesi using the FARO QuantumS Arm, which guarantees optimal metrological accuracy, and are then processed using the CAM2 Measure 10 software, which guides the operator, allowing them to take measurements quickly and easily.
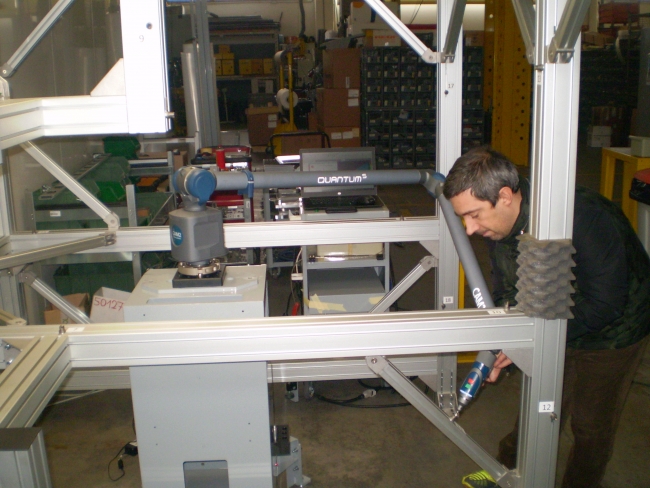
Spanesi is now able offer the calibration of its instruments much more quickly and easily to its customers all over the world / Picture: FARO
Finally, to calibrate its coordinate measuring instrument, Spanesi compares the absolute position of the 18 reference points on the cage previously measured using the FARO QuantumS Arm with those measured by its measuring instrument. The 5508 results obtained by combining the distances between the 18 reference points and reworked using the customized software allow Spanesi to calibrate the operating parameters of its measuring instruments and thus guarantee to repair shops the accuracy required to comply with the quality parameters imposed by manufacturers and applicable regulations.
“By using the calibrated aluminium cage and the FARO QuantumS Arm, we have cut our calibration time from 4 hours to just 30 minutes. That’s not all. Now we can guarantee the calibration of our instrument over a much larger area, corresponding to the typical dimensions of a car,” confirms Siviero.
Thanks to the new calibration approach, Spanesi is now able offer the calibration of its instruments much more quickly and easily to its customers all over the world – they just need to contact their local distributor, who is equipped with the new calibration cage. Spanesi’s attention to quality and customer service is perfectly matched with the metrological characteristics and ease of use of FARO’s products, so much so that the laboratories of the Italian company are already studying new solutions based on laser measurement technologies, which will further enhance the solutions offered to the bodywork industry.