6 minute read
Energy legislation – a heads up for what’s in store
For manufacturing businesses across the UK, the need to push output up while keeping overheads down is an ongoing challenge. Energy costs are likely to be one of your most significant overheads and many different factors will affect how much you spend each year on energy, as well as on the resources you need to properly manage this essential commodity. Ørsted takes a look at what manufacturers need to know.
Staying up to date with energy legislation is vital. Knowing your compliance and reporting obligations will ensure you avoid any penalties – and understanding regulatory changes can also help you to uncover cost savings opportunities and take advantage of valuable tax breaks. When it comes to energy legislation, knowledge is most certainly power.
Changing regulations for a changing system
If you’re feeling as though energy legislation is changing at a faster pace than ever before, you’re probably right. The pace is being set by our changing energy system. As a nation, we are decarbonising energy production to help us meet the UK’s carbon reduction targets; our better energy future depends on increased use of sustainable power sources such as wind and solar. We’re also decentralising our energy infrastructure, so rather than relying on a handful of coal-fired power plants to provide most of the country’s electricity, many hundreds of assets are contributing – sharing the rewards and spreading the risk.
Business energy customers will be noticing the following effects of this energy evolution:
• The make up of energy bills has changed, with non-commodity costs accounting for an increasing percentage of your costs
• Time-of-use is growing in importance across a wider range of businesses
• New mechanisms have been introduced to incentivise businesses who help to balance the grid through demand side response (DSR)
• New exemptions are becoming available to protect energy intensive industries from rising costs.
With so many factors to consider, and so many opportunities out there for the taking, it’s important that manufacturers stay up to date with energy policy. Here’s an overview of some of the key changes taking place:
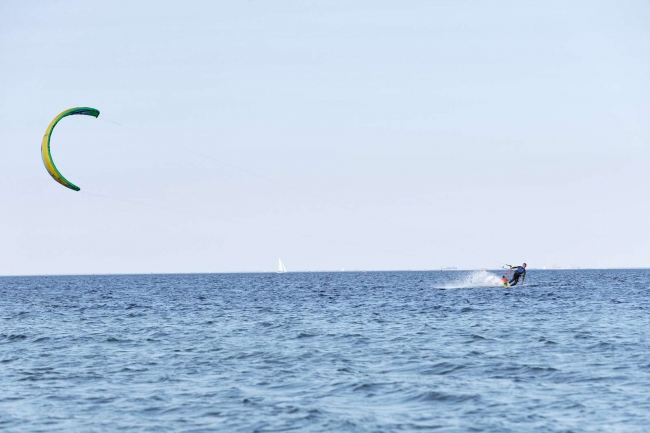
Understanding regulatory changes can help manufacturers to uncover cost savings opportunities and take advantage of valuable tax breaks / Picture: Ørsted
April 2018 – new levies
April is an important month when it comes to energy budgeting, and that’s because several non-commodity charges either change or are reconciled every April.
In 2018, businesses can expect to see increases in Contracts for Difference (CfD) and Capacity Market charges. Both types of charges are designed to ensure that the country always has enough generation available to meet forecasted demand. Within the Capacity Market, demand forecasts are reviewed each year and an auction is held to fill any gaps identified. While there is a cost associated with running this system and holding the auction, the intention is that the competition will keep energy costs down for the consumer.
Feed in Tariff (FiT) and Renewables Obligation (RO) levies are also due to increase. Both are designed to support smaller scale renewable generation, such as domestic solar installations and commercial on-site renewable generation.
Will your DUoS charges increase?
System charges are also updated in April and this year will bring a significant change to Distribution Use of System (DUoS) charges.
DUoS charges contribute to the cost of maintaining the regional networks that transport electricity from local substations to the end user. Up until 1 April 2018, using electricity at peak periods, such as the end of the working day, has been significantly more expensive than consuming at times when demand is much lower – overnight, for example. From April 2018, the charging structure has changed, lessening the gap so that the peak periods are less expensive and the off-peak periods are more expensive. For manufacturers that actively avoid the 4pm – 7pm period, this may mean an overall increase in DUoS costs.
Help for energy intensive industries
Because energy costs have risen in recent years – and this trend is set to continue – there is a recognition that those costs have had an adverse impact on energy intensive industries (EII). As a result, exemptions are available for those businesses most affected. A wide range of sectors are eligible, including iron and steel, plastics manufacture, ceramics, electronic components and chemical manufacturers, to name a few.
Compensation has been available for RO, FiT and CfD charges since 2016, to be replaced by exemptions from this year. Eligible sectors must apply for an exemption, and no backdating is allowed under the scheme rules. BEIS anticipates that those businesses eligible for the full exemption package will be significantly better off under the new scheme, as they will avoid the substantial upfront payments paid previously.
Manufacturers of all sizes are advised to check whether their business qualifies for any exemption and ensure that they have all the details needed available as soon as the exemption process opens. BEIS is also consulting on widening the exemptions to other sectors, making it one to look out for.
Half-hourly meters
From 1 April 2018, a new regulation will be introduced, affecting all businesses with half-hourly (HH) metered electricity – which, in practice, is most large businesses. Known as DCP161, it will bring in new penalties for those businesses that exceed their pre-agreed electricity capacity limits for their site (also known as Maximum Import Capacity). With this in mind, it’s important for manufacturers to check their capacity limit with their supplier and determine whether that limit might need to be changed to avoid excess capacity charges, based on usual business activity and future requirements.
The Climate Change Levy
The Climate Change Levy (CCL) is also due to be rebalanced between electricity and gas, reflecting the changing fuel mix in the UK. Essentially, this means that the cost of gas will rise slightly as CCL for gas goes up. The Carbon Reduction Commitment Energy Efficiency Scheme (CRC) will be abolished from 2019, and CCL rates will rise to recoup the lost tax revenues from CRC, whilst relieving the reporting burden associated with the scheme. CCL rates for 2020 – 2022 will be set in Budget 2018, providing useful insight for those responsible for planning energy budgets.
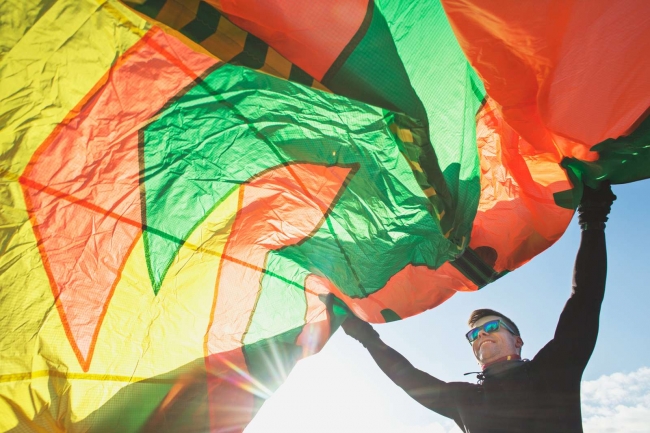
With some forward thinking and a little help from industry experts, manufacturers may be able to make the changes in the system work to their advantage, clearing the path to a more sustainable and cost-efficient energy future / Picture: Ørsted
What are your next steps?
There is certainly a lot for businesses to consider when it comes to managing energy budgets, and one thing is certain: electricity and gas prices will continue to go up. Exemptions for energy intensive industries provide some welcome relief, but to really push overheads down, a carefully devised strategy is what’s needed.
Flexible purchasing:
Commodity costs may form a diminishing proportion of the energy bill, but they are still significant. Opting for a flexible purchasing strategy can give your business a price advantage when commodity costs are lower, so may provide a better option than paying a premium to have a fixed unit cost throughout the year. Our trading team helps customers to devise strategies suitable for their business activities and their attitude to risk. They have a proven track record of reducing overall energy costs.
Checking schedules:
Reviewing your approach to scheduling can also make a big difference to your energy bill. By reducing consumption and – where possible – switching to on-site generation during peak periods, you can really lower your costs. Kodak Alaris used our Site Optimisation tool to identify commercially optimal run schedules at their plant, resulting in an 11% reduction in energy costs. [link to case study]
Flexibility solutions:
DSR schemes pay businesses to reduce their usage during periods of high consumption, to help balance the electricity system. In return, the business receives a payment. With flexible business consumption playing an increasingly vital part in our evolving energy system, why not see how your business could tap into this revenue opportunity?
Energy reduction:
Using less energy is core to any energy management strategy. Many businesses will have already implemented the simple measures with guidance from their 2015 Energy Savings Opportunity Scheme (ESOS) assessment report, indicating where they can achieve the most significant savings. With enhanced capital allowances available for some energy-saving technologies, it’s worth taking another look to see whether your business could benefit.
Complete solutions:
Undoubtedly, the best results will come from a multi-faceted energy strategy, but this can feel daunting, particularly when the focus needs to be centred on core business operations. In recognition of this, we have launched new solution: Energy as a Service. This new solution from Ørsted will take on energy management on behalf of organisations. The team works with businesses to identify an appropriate strategy, before going on to implement it for them.
Energy as a Service will cover a full range of initiatives including commodity purchasing, installation of energy saving technology and embedded generation. We know that finding CAPEX can be an issue, so we can also provide upfront investment for a period up to 20 years, to help businesses work smarter and ultimately reduce their consumption, as well as their costs.
Ask for help
For busy manufacturers, it may seem as though there are ever-increasing pressures and not enough hours in the day to really get to grips with energy legislation. However, with some forward thinking and a little help from industry experts, you may be able to make the changes in the system work to your advantage, clearing your path to a more sustainable and cost-efficient energy future.
If you want to read more on the latest industry news and regulation, read Ørsted’s update here