4 minute read
Hochiki Europe: A manufacturer supplying the world’s safety systems from Gillingham
Alarms, detectors and emergency lighting are incredibly important in today’s built environment, as recent events have tragically made all too clear. Fire safety is at the forefront of people’s minds and it’s being increasingly recognised that today’s products need to not only meet, but also exceed building regulations. Jay Oliver, Production Manager at leading manufacturer of life safety systems, Hochiki Europe, shares how careful planning and innovative production processes ensure the highest quality fire and emergency lighting products are manufactured as efficiently as possible.
When Hochiki Corporation was founded 100 years ago, some of the company’s first fire alarm devices – considered innovative at the time – were simple, button operated, streetlamp-style call points. Over the decades, our insight and knowledge of the way fire spreads in buildings has advanced vastly, and so too have the safety systems we develop to protect occupants.
Hochiki Europe is one of the world’s leading manufacturers of life safety technology and has operated in the UK for over 25 years. The innovative products we create from our European HQ in Gillingham, Kent, are installed in premises around the globe, helping to safeguard building occupants in an array of sectors, with many different legislative requirements.
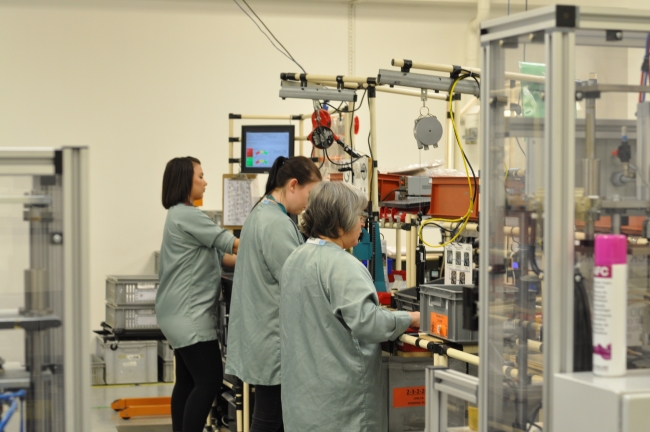
Hochiki employ 135 staff at their European headquarters in Gillingham / Picture: Hochiki Europe
Over the last two decades, our customers – made up of facilities managers, installers, distributors, architects, consultants, building owners and others responsible for fire safety – have come to expect an unparalleled level of service. Central to our offering is the promise of a fast, reliable and transparent product supply chain, which means our Production and Production Engineering departments are continually working hard to support this.
These two divisions, which I oversee, are responsible for the manufacture and assembly of our innovative products. Maintaining the incredibly high-tech manufacturing machinery and ensuring the right resources are always available to meet orders on a global scale are central to our operations.
Like most manufacturers, our schedule of production is mainly led by sales, with products being manufactured in-line with customer demand. At the same time, we also keep reserve stocks of some our most popular products so our customers can continue to get the level of service they expect, even in peak periods. Having production forecasts in place to maintain this reserve stock of products is key and helps us meet our next day delivery policy.
When it comes to bringing new products and systems into our production schedule, we operate a lean manufacturing process, ensuring every stage on the lines is ultra-efficient. Departments from across the business, including design and technical, work together to understand how we can manufacture high-quality products in a timely and cost-effective way. Once a plan is in place, a product will go into pre-production and a set number of units will be built. This process will then be reviewed to check for ways to improve productivity before mass production. By understanding the different elements of the production process, we are able to constantly review and adapt our practices, so we can continually improve as a manufacturer.
This level of review also feeds into our day to day working within our Production division, and real-time feedback is shared with staff via personal screens on the factory floor. These screens allow our employees and their supervisors to see where they can optimise efficiency or make changes to improve workflow via colour code messages. In the past, this kind of process was done with paper systems which did not always provide the most current data, and consequently, production was not adequately adjusted to meet targets.
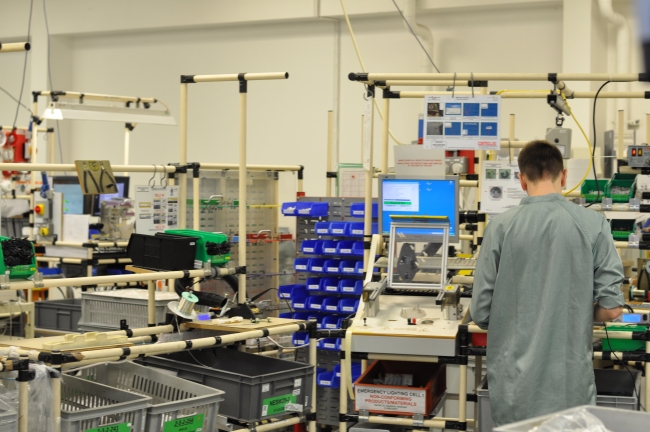
Real-time feedback is shared with staff via personal screens on the factory floor to optimise efficiency or make changes to improve workflow / Picture: Hochiki Europe
Another part of our production that sets us apart from other life safety manufacturers is our solid smoke testing procedure. In this instance, artificial smoke is created and used to calibrate our detectors in as few as 15 seconds. This saves us a significant amount of time during the testing process, when compared to the traditional method of testing using real smoke.
Our production capabilities have grown exponentially in recent years, and our manufacturing output now extends beyond traditional fire detection equipment to accessories, modules and emergency lighting. We’ve also been making the most of our existing efficiencies when developing new products. Earlier this year, we shipped our ACC production line from our Japanese factory to our Gillingham site, to improve efficiency. It is processes like this that make Hochiki Europe and our ways of working so unique.
Looking ahead to the next 100 years of operation, we will be expanding our production capabilities and increasing our production capacity. As fire safety technology becomes more advanced, the individual components within them are getting smaller. Some of the parts we work with are smaller than the size of a pin head so we’re having to amend and invest in our machinery to keep up with current component technology.
Technology is getting smarter and at Hochiki Europe, we are working to find ways to stay ahead of the curve. By continuing with our rigorous continuous improvement process, we can continue to deliver the most robust and dependable life safety solutions promptly, efficiently and effectively.
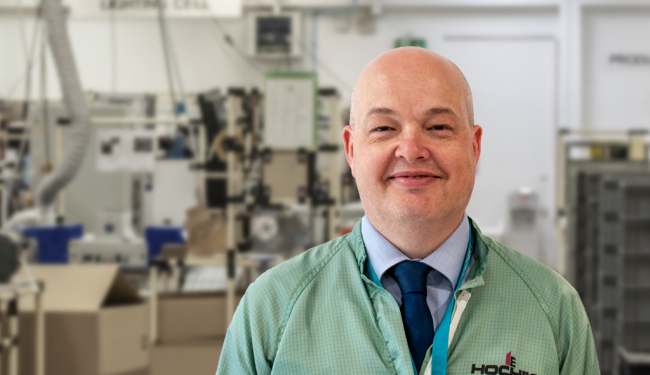
Jay Oliver, Production Manager at Hochiki / Picture: Hochiki Europe