3 minute read
The trials and tribulations of manufacturing a mechanical watch under 6mm high
Just how do you produce a mechanical watch that is less than 6mm high? Well, Adrian Buchmann, Senior Designer at British timepiece manufacturer Christopher Ward explains all.
Creating a new watch is no mean feat. From the exterior materials and design to the intricate mechanisms and components under the hood, every element must sing together in perfect harmony. Just the tiniest design or manufacturing flaw (we’re talking tenths of a millimetre), and the entire function of the piece can be compromised.
So, when Mike France, the co-founder of Christopher Ward – the British watch company for whom I am the Chief Designer – boldly set the design and manufacturing teams the task of designing a watch less than 6mm thick, you could have heard a pin drop.
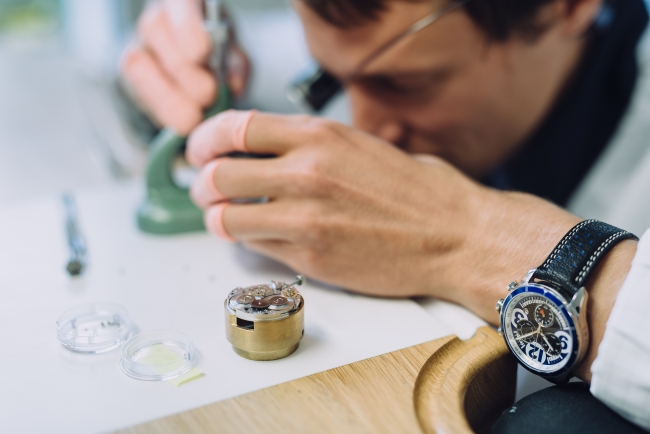
Picture: Christopher Ward
To put this in context, this would be one of the slimmest watches in the world; you could probably count the number of watches slimmer than this on one hand. The difference between a 6mm case and say a more common 8mm case might not sound a lot, but in the world of watchmaking a few millimetres is the equivalent to a few miles. We were essentially being asked to drive a Lamborghini into a garage designed for a Fiat 500.
The design challenges
The first challenge concerned the case: in some of the world’s slimmest watches, the case is effectively part of the movement. But with our new watch, we wanted to stay traditional and keep the case and movement completely separate. The next step was to establish what type of movement would be most suitable, and given the watch’s requirements and specifications, a mechanical movement made the most sense.

Picture: Christopher Ward
As we also learnt, the slimmer the watch, the higher the likelihood of components breaking – primarily because you’ve got much less room to manoeuvre, but also because slighter components are more fragile. We therefore had to achieve the perfect balance of space efficiency and durability, all whilst keeping the costs sensible and the design beautiful.
Bringing the manufacturers onboard
For our manufacturing suppliers, this was unchartered territory too.
One of the greatest challenges was persuading them that this watch, and the specialist components we needed exactly to our specifications, were genuinely possible to produce. Given that each component – the case, the dial, the hands etc. – are supplied by different manufacturers, everyone had to be onboard. Once we were all in agreement, they all rose to the occasion and handled the pressure brilliantly – even if it understandably took them longer than usual to put everything together because of our very specific requirements.
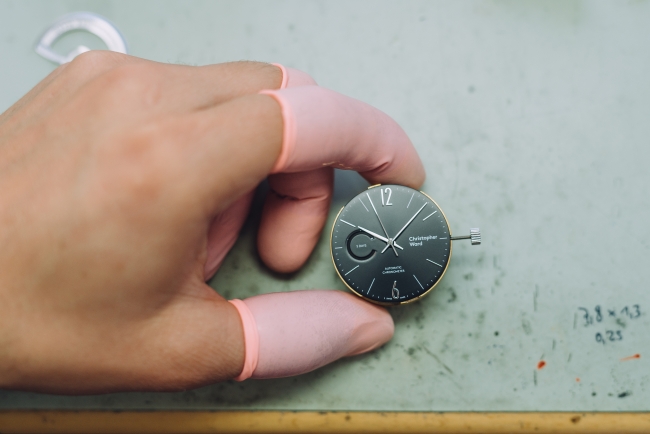
Picture: Christopher Ward
The whole process requires endless testing and back and forth – both internally within the design and technical team, and then between the design team and the various manufacturers. Prototypes get assessed in labs, components get tested and retested, and the nature of the tiny parts means a higher chance of rejection in the quality control stage.
The importance of collaboration
The importance of all of us – the designers and manufacturers – pulling in the same direction cannot be overstated. Constant dialogue, staying positive and the sharing of expertise was imperative to the project succeeding. At all times we maintained the attitude that it was never a question of whether the project would succeed, but when.
Anything new is technically more risky – naturally it is always easier to do what you usually do. But through perseverance we have been able to break new ground, and push the boundaries of what we thought was possible. The knowledge we have picked up along the way will prove invaluable for the future.
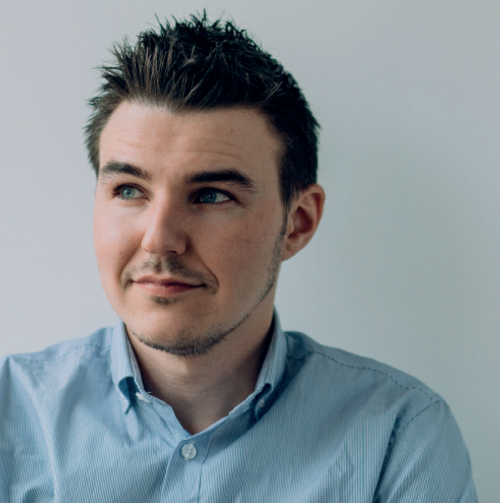
Adrian Buchmann, Senior Designer at Christopher Ward / Picture: Christopher Ward