4 minute read • published in partnership with KUKA
Waste not, want not – Robotics in recycling
The reuse and recycling of products is a huge consideration today as business owners and consumers alike embrace sustainability, as topics such as global warming and the depletion of the earth’s natural resources continue to dominate the headlines. KUKA Robotics take a look at the solutions robotics provide.
As the global population continues to grow and more and more products are produced, more waste is produced and the need to manage this waste, efficiently and cost effectively, is crucial. The management of this waste by manual means only is not possible, simply because of the volume and diversity of waste in question.
The automation of such processes, through the introduction of robotic applications, is driving the future of waste management across a number of sectors. Recycling facilities are increasingly embracing technology as a means to drive operational throughput and increase efficiency, with key considerations such as contamination minimisation; environmental impact and economical profitability; maintaining competitive advantage – strategic considerations for business owners.
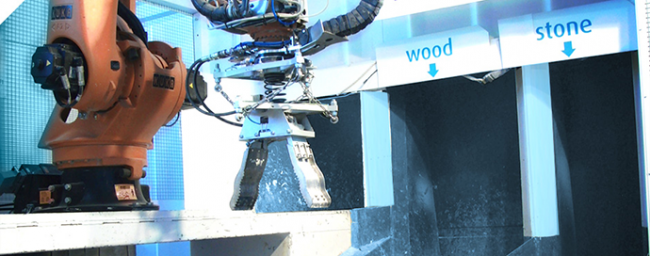
Recycling facilities are increasingly embracing technology as a means to drive operational throughput and increase efficiency / Picture: ZenRobotics / KUKA
There exist a plethora of materials that can be recycled. From low risk household products such as paper and cardboard, plastics and glass to hazardous industrial waste such as chemicals and solvents, paints and sludge to potentially lethal special hazardous waste products such as radioactive waste. When we consider the latter, it is easy to see just why automated robotics feature more and more within waste materials handling applications.
Automated robotics can be implemented upon a scalable basis, allowing an operation to grow as productivity increases and a better recyclate is achieved. A unique selling point that draws any customer regardless of industry – the manufacturer’s ability to provide an efficient and cost effective solution.
Adopting automated robotics as a means to compliment an existing process means there are no costly infrastructure investments. Robotic cells can be strategically placed, and moved, according to the needs of the business.
Whilst manual intervention is being reduced, it is by no means being phased out of waste materials handling completely. There do still exist some areas within the recycling process that still require the need for skilled operatives. Consider municipal waste that is destined for incineration. This needs to be manually sorted to filter out any valuable waste products, such as plastic or glass, items that will eventually go on to be recycled. For this, we still need to utilise the human eye. Vision guided automated robotics may feature further downstream, though these processes will purely be complimentary.
Working in and around municipal household waste is by no means pleasant, though as packaging solutions are evolving to conform to new stringent guidelines, aligned with government targets, more and more material can be recycled as opposed to being sent to landfill.
Radioactive waste, compared to municipal household waste, presents a whole new dynamic however when it comes to recycling and/or storage. The implementation of automated robotics is done so as the nuclear decommissioning tasks and activities that are currently being carried out across the UK, are simply deemed too dangerous for humans to undertake. Such tasks can include, but are not limited to; handling and sorting of waste products, size reduction, box encapsulation, lidding and swabbing.
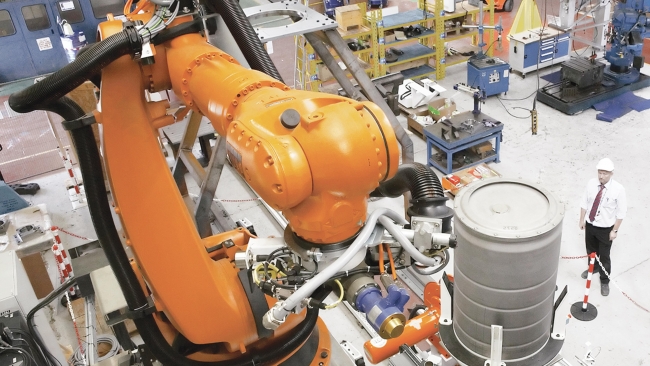
Automated robotics are used for nuclear decommissioning tasks and activities that are simply deemed too dangerous for humans to undertake / Picture: KUKA
Remote operations and robotic systems play an integral part in reducing the exposure of humans to dangerous ionizing radiation. The decommissioning of some of Europe’s oldest nuclear facilities means that huge amounts of radioactive waste have to be handled, so autonomous nuclear waste management is the only viable solution. The containers into which the radioactive waste is placed are simply too large for a human to manage, from both a filling and movement perspective, not to mention again the harmful nature of their contents. But we are not yet at such an advanced stage that the robots are independently autonomous. Manual intervention, from a control perspective, is still required.
Consider the KUKA patented joystick control. A unique solution within the nuclear decommissioning market. It has been developed to seamlessly interface with the KUKA industrial robot allowing an operator to use a KUKA robot remotely, placed well away from any harmful radiation. It is particularly suited for complex jobs such as nuclear waste retrieval, sorting and levelling.
Nuclear decommissioning is the most extreme environment that exists within the realms of waste materials management, but not the only that poses a risk to recycling workers. Moving vehicles and/or machinery, respiratory challenges (dust etc) conveyors and compactors; these are all elements that exist within the recycling industry and present risks and dangers to recycling workers on a daily basis. Whilst they play a critical role in the supply of quality feedstock (raw materials) business owners should embrace automated robotics, not only as a means to protect human workers by assigning non-ergonomic, dangerous tasks to technology but to retain market share and remain competitive in what is becoming a competitive market, as the need for quality recycled material increases.