2 minute read
Capula to strengthen production capabilities with investment programme
Staffordshire-based Capula is investing in its industrial design and manufacturing capability, as it looks to boost volume and strengthen its production facilities.
Designed to deliver significant efficiencies and optimise both capacity and capability at its head office in Stone, this latest programme of investment is aimed at introducing batch production techniques, including the creation of production cells.
The industrial control, instrumentation and automation specialists will be investing even further with a full programme of digitalisation as part of this initiative. This will include the adoption of new technologies and optimisation of production techniques, such as the introduction of a Lean-Lift. The Lean-Lift will allow the production team to more efficiently locate key production components and tooling, simplifying the assembling phase.
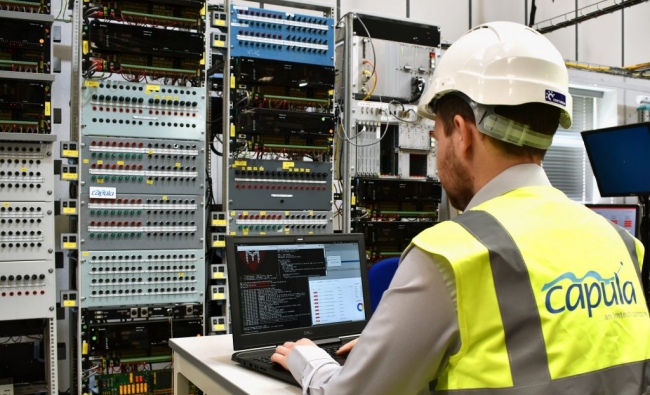
Capula is set to boost volume and strengthen its production facilities in its latest programme of investment / Picture: Capula
Further development will include the deployment of Capula’s very own digital technologies to provide enhanced visibility of the production process, in turn improving the management of the manufacturing process and optimising both efficiency and quality.
This will include a new digital communication capability and tools to support operational efficiency including traceability and expediting of materials, identification of build and test issues, and automated notifications to project teams to ensure on time delivery.
Matt Haubus, head of production and business improvement, said: “Being recently appointed to this critical role, having worked at Capula for over 6 years as engineering and quality manager, I’m really excited to help with our continued drive to optimise our design for manufacturing capability to deliver even greater value to our customers.
“Key to this project is helping us to better design for manufacture, leveraging best practice and more importantly embracing the digital tools and technologies we deploy to our customers across a variety of industries.”
Paul Bayliss, operations director, added: “Our design and manufacturing capability has been placed in high regard by our customers, having supported many critical national infrastructure programmes, some for over five decades. Investing in our facilities is part of our ongoing strategy to ensure we can continue to support major projects across the UK and beyond, with a focus on driving productivity, efficiency and value to our customers.”
This project has an accelerated timeline throughout summer and into autumn, with a prototype production facility to be tested in December.