6 minute read - 13th September 2022
£25m funding for electric vehicle technology projects
The Advanced Propulsion Centre (APC) has announced the winning projects that are set to receive a share of around £25m in government grants. The funding will be used to assess if projects are ready for scale-up and to support the growth and expansion of businesses in the UK automotive supply chain.
The funding has been awarded to 22 projects, comprising 35 UK-based companies and research organisations, which will receive a range of grants, up to £2m each, through the APC’s Scale-up Readiness Validation (SuRV) competition.
The grants are awarded as part of the Automotive Transformation Fund (ATF), a programme created to support large-scale industrialisation. Up to £1bn of funding is being invested through the ATF in developing a high-value end-to-end electrified automotive supply chain in the UK. The fund has already been used to develop the UK’s battery gigafactories and supply of critical materials through large capital financing.
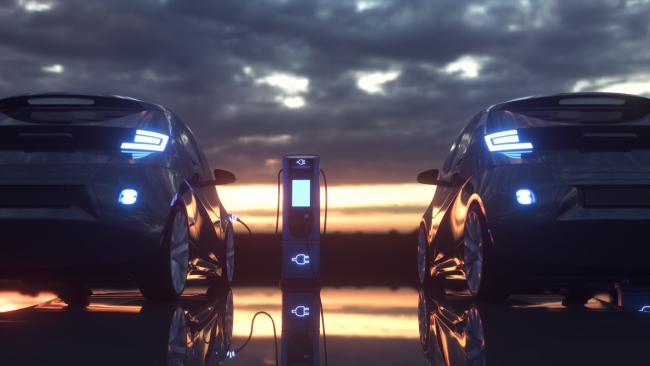
The Advanced Propulsion Centre has announced the winners sharing around £25m of government investment to support the scale-up of electric vehicle technology / Picture: Getty/iStock
SuRV was launched after insight showed there is often a need to validate products or processes to de-risk the making of key decisions for much greater investment. The APC says the announcement supports this ambition with recipients located around the UK, working on a range of processes and pilot lines that could grow to be large-scale manufacturing of technologies, including power electronics and motors, batteries and fuel cells.
Ian Constance, APC chief executive, said: “I am pleased the APC has announced £25 million of funding to 22 projects from our Scale-up Readiness Validation competition. These successful projects will support the UK automotive industry, by increasing confidence in large-scale manufacturing investments and building electrified supply chains. It is vital in the transition to net zero that the automotive sector seizes the opportunity to grow the industry, create or safeguard jobs and build on the expertise anchored here in the UK.”
Julian Hetherington, APC automotive transformation director, added: “This announcement underlines the commitment to support the automotive sector, one of the UK’s strategically important industries, as it makes an unprecedented transition towards net zero. I am proud of the role the Automotive Transformation Fund is playing in unlocking opportunities for investment, and the projects chosen here all have real potential to scale-up to something significant. Through our support, we aim to encourage and de-risk subsequent private investment by demonstrating that these innovative products and technologies work at scale.”
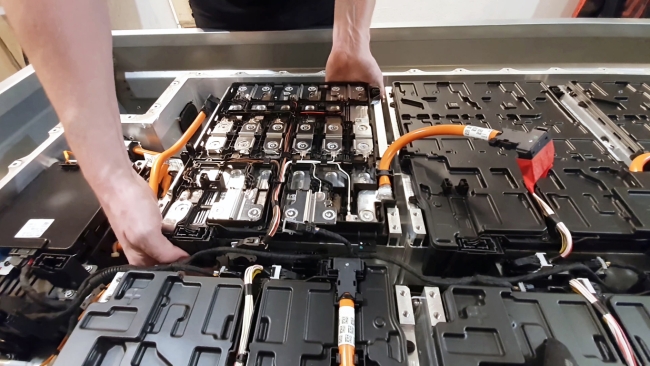
22 projects, comprising 35 UK-based companies and research organisations, will receive up to £2 million each / Picture: Getty/iStock
Projects and companies funded through SuRV
Batteries
Nexeon
A project to install a larger scale manufacturing facility in the UK, supporting the advanced silicon anode material volumes needed for battery cells in the UK automotive industry.
Avocet Battery Materials
The project will help establish a localised supply chain of critical battery components in the UK and wider European Li-ion battery industry.
Reaction Engines
Reaction Engines’ technology improves thermal management and safety of battery cells and packs. This project will prove out volume production of its HxLife Foils battery thermal management technology through a dedicated pilot line.
Deregallera
To boost confidence in scaling up manufacturing of electric powertrains, this project will include pilot production using lean manufacturing techniques and establish the battery cell layout, proving scalable production viability. A quantity of units will be produced for validation.
Ilika Technologies
Ilika is developing an automotive solid state battery cell alongside a scalable process for manufacturing. To further de-risk its industrialisation plan, the project will enable Ilika to work with UK-based supply chain to validate its scale-up activities by conducting trials using representative volume manufacturing equipment.
Nyobolt
Nyobolt and Koura are partnering to scale and validate the purification and finishing of fast charging battery materials. This aims to reduce vehicle charging times to just minutes and develop UK supply chain capability.
AMTE Power
MegaPower: High power cell development for AMTE’s Megafactory.
Battery critical materials
Research By British Lithium
British Lithium is developing an integrated hard rock quarry, beneficiation plant and lithium refinery producing 20,800 tpa of battery-grade lithium carbonate. This project will partly-fund the readiness assessment and validate the pilot plant whilst making commercial samples for end customers.
Cornish Lithium
The SuRV grant will be used to construct the hydrometallurgical section of a demonstration scale processing plant at the Trelavour Lithium Project in Cornwall. The plant will produce samples of battery grade lithium hydroxide for evaluation by battery producers and automotive OEMs.
Recycling
Altilium Metals
Producing production samples of cathode metals for testing by Imperial College, to support the case for a commercial plant recycling battery waste from 20,000 electric vehicles.
Fuel cells
Ultima Forma
This project will bring a key hydrogen barrier containment technology closer to market, by funding the installation of an electroforming pilot line for the manufacture of thin, lightweight metallic liners for pressurised hydrogen storage vessels.
Bramble Energy
Bramble Energy will develop a semi-automated pilot-scale assembly line for fuel cell stacks. This will demonstrate the simplified and low-cost manufacturing route and assembly process of Bramble’s trademarked printed circuit board fuel cell and the roadmap to scale up manufacturing in the UK.
ZF Automotive UK
Project partners will produce a series of fully functional air compressor prototypes for commercial vehicle hydrogen fuel cell applications, with a clear roadmap toward high-volume production.
Adelan
This project will assess the feasibility of manufacturing a fuel cell range extender at scale. It builds on work by Adelan to establish UK fuel cell manufacturing using Midlands partners for component manufacture and assembly. It will create automated solutions to support UK suppliers to manufacture at volume to achieve economies of scale.
Kingspan Water & Energy
The project will produce a high performing, cost effective, and light weight hydrogen storage solution, with improved environmental credentials. The novel manufacturing method developed will allow bespoke storage solutions and enable rapid commercialisation.
Motors and drives
Electrified Automation
This project will demonstrate scalability of innovative manufacturing processes for radial flux concentrated wound electric motors.
Depe Gear Company
The project is designed to help develop the UK supply chain into the volume manufacture of high precision gear and transmission components cost effectively.
Saietta Group
Saietta will on-shore and scale-up the production of heavy-duty e-drive products in Sunderland – investing in people; prototypes; processes and equipment to deliver and commission a Pilot Line.
Motor critical materials
Seren Technologies
Commercialising rare earth separation and refining technology, developed at Queens University Belfast. The innovative technology is being applied to magnet recycling for the chemical extraction of rare earths from spent magnets, refined to high purity oxides for making new environmentally-friendly magnets for EVs and wind turbines.
Power electronics
Magnetic Systems Technology
Securing this SuRV funding allows Magtec to industrialise its controller systems using automation best practices, redesigning products and developing supply-chains for volume manufacture. This will result in the ability to demonstrate next-generation controller production through a pilot-line, de-risk production and secure further investment to support growing demand.
SGA Technologies
This project brings together expertise in power electronics, power modules and packaging with SGA, CIL and MTC working together to create a UK source of advanced ceramic heat dissipative substrates. The latest laser manufacturing methods are used, designed for the electric vehicle market, providing security of supply in the UK.
Strip Tinning
Cell contacting and management system (CCMS) is an integral part of the power electronics in electric vehicles, monitoring the performance and safety of batteries. This project facilitates scale-up to support collaborations with OEM clients, intended for new BEV models in the next 2-5 years.