6 minute read • published in partnership with CQM Training & Consultancy
Case Study: £1m and counting – How CQM’s lean six sigma training course delivered hard benefits for a soft drinks giant
To support its journey towards operational excellence, Britvic partnered with award-winning business improvement specialists CQM Training and Consultancy. In its first year, the collaboration has the potential to deliver over £4.1m in annual cost savings and embedded a culture of continuous improvement across Britvic’s UK operations.
Founded almost a century ago, Britvic has grown from a small entrepreneurial business into a global giant with nearly 40 brands sold in over 100 countries. Known for family favourites like Fruit Shoot, J2O, Robinsons and Tango, Britvic also exclusively manages PepsiCo brands in Great Britain and Ireland, including 7UP, Lipton Ice Tea and Pepsi MAX.
Headquartered in Hemel Hempstead, Britvic operates factories in Rugby, Beckton and Leeds, with additional centres in Lutterworth, Solihull and Tamworth. It also has production facilities in Ireland, France and Brazil.
A need for structured improvement
As Britvic’s sales continued to rise, the company faced the challenge of boosting capacity while maintaining efficiency and reducing costs. Recognising the need for a more structured approach to improvement and change management, Britvic partnered with CQM Training and Consultancy – a highly-regarded business improvement specialist renowned for delivering practical, real-world training that drives sustainable business change.
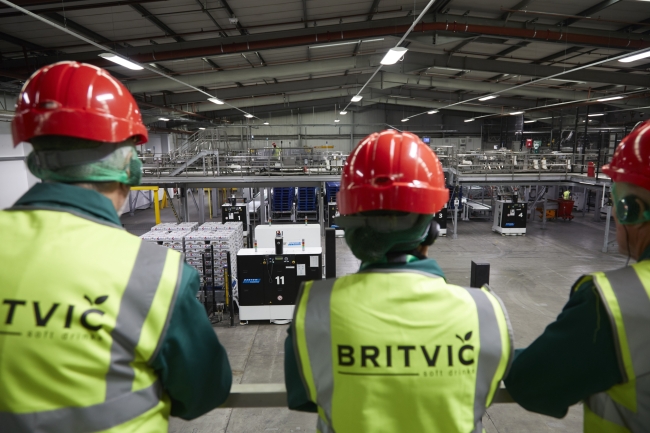
Picture: Britvic
“Two years ago, we identified the need for structured training that could enhance our improvement projects and drive business change across all levels of the organisation,” says Mark Young, Britvic’s Head of Continuous Improvement (CI).
While the CI team had introduced some foundational Six Sigma concepts, Britvic’s growing operational needs required a more focused and scalable approach – one designed not just to teach tools and techniques but to empower employees to effectively solve problems at the root cause, creating a measurable difference. CQM’s Lean Six Sigma Green Belt training course, delivered by expert instructors, was the perfect fit.
“The quality of CQM’s training and their ability to coach it effectively into our teams really set them apart,” explains Mark.
Understanding lean six sigma and the belt system
Lean Six Sigma is a methodology used to drive business process improvement, combining two management techniques: Lean, which focuses on removing waste from any process, and Six Sigma, which improves quality and reduces the likelihood of defects and errors. Six Sigma is structured around five levels of coloured belts, similar to martial arts, indicating the level of expertise:
• White Belts understand basic Six Sigma concepts and can use them to work on problem-solving, but aren’t typically involved in complex projects or data analysis.
• Yellow Belts have a more in-depth understanding of Six Sigma and can support projects by reviewing improvements through data collection and data mapping.
• Green Belts have an intermediate level of knowledge, capable of leading smaller projects and supporting larger ones, driving process improvements within their areas of reasonability.
• Black Belts possess advanced skills in Six Sigma, leading complex projects and mentoring Green Belts. They are proficient in data analysis and statistical methods, often working full-time on Six Sigma initiatives.
• Master Black Belts are experts who oversee the strategic use of Six Sigma across an organisation, mentoring Black Belts and ensuring improvement projects align with wider business goals.
Central to Six Sigma is the DMAIC framework, a structured approach guiding teams through problem-solving that leads to sustainable improvements:
• Define: Identify the problem or process that needs improvement.
• Measure: Collect and analyse data to understand current performance.
• Analyse: Determine the root cause of issues or inefficiencies.
• Improve: Implement solutions to address the root causes.
• Control: Monitor the changes to ensure they deliver sustained benefits
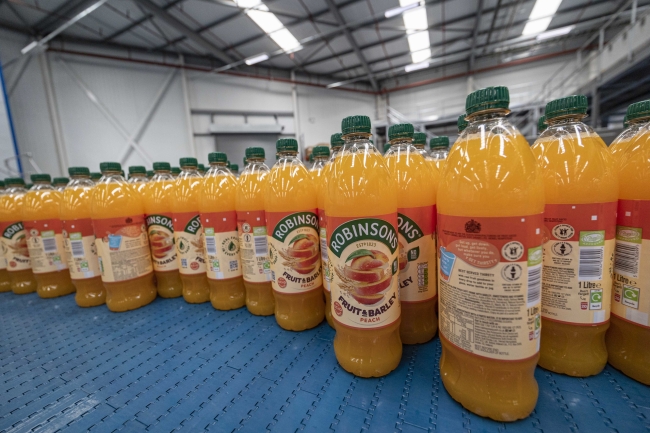
Picture: Britvic
Transformative benefits
The first cohort to receive Lean Six Sigma Green Belt certification comprised nine individuals, each leading an improvement project tailored to their role and guided by CQM’s instructor. Collectively, the projects have the potential to deliver more than £4.1m in annual cost savings, addressing critical operational challenges from reducing downtime and process loss to improving overall equipment effectiveness (OEE).
The results were nothing short of transformative. Downtime on one bottling line was reduced from three hours to just 17 minutes, capacity on another line increased by almost 200 hours annually, and zero waste was achieved on one line’s de-palletiser. Annual cost savings from these projects ranged from tens of thousands to millions of pounds, with the learnings and successes now being replicated across other lines and processes.
Equally important, it has equipped existing employees with skills and techniques that are now being further developed and applied across the organisation, fostering a culture of continuous improvement that will future-proof Britvic’s operations for years to come.
One standout project was led by Louise Rewcastle-Adams, Britvic’s Customer Operations Manager. Her project tackled inefficiencies with a major supermarket chain whose systems weren’t aligned with Britvic’s production sites. This misalignment caused excessive and avoidable internal stock moves, resulting in substantial cost, labour and environmental implications.
By implementing a more systemised approach to order creation, Louise’s project reduced unnecessary stock moves and manual intervention, creating availability for additional sales.
“Through the project, we increased our vehicle utilisation, reduced CO2 emissions and slashed the average miles travelled per pallet substantially. The amount of CO2 we saved is equivalent to charging more than 6 million smartphones or taking 11 cars off the road for a year,” Louise explains.
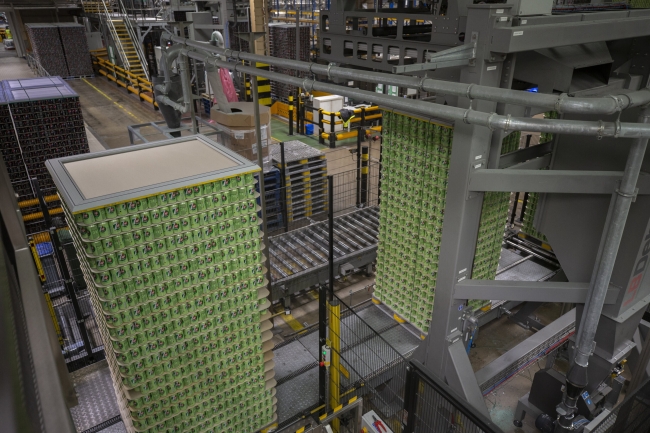
Picture: Britvic
“The annual savings came to just under £1m, but what really sold the changes to the customer was the sustainability aspect. They quickly bought into the idea because we had all the data and insights to show it was the right thing to do.”
This success was particularly significant as previous attempts to address the issue had failed. “The breakthrough we achieved was a direct result of the quality of training from CQM and how we presented the data to the customer. It’s phenomenal what we’ve been able to accomplish, and we owe a lot of that success to the insights and hands-on guidance from CQM,” says Louise.
The positive impact of Louise’s project didn’t stop there – other customers are now seeking her advice to improve their own supply chains. “This course has not only enhanced Britvic’s credibility with customers but also strengthened our internal supply network. It proves that the right tools and training can unlock dramatic improvements.”
Unlock the power of your people
Beyond the immediate financial benefits, Britvic’s partnership with CQM has had a profound impact on staff morale, teamwork and career development. The Green Belt provided practical, actionable skills that have empowered employees to take ownership of improvement initiatives and advance their careers.
Since becoming a certified Green Belt, Louise has sponsored several of her team members through Yellow Belt training, ensuring they too can contribute to Britvic’s ongoing success. She has recently been promoted to Category Demand Planning Manager and credits the Lean Six Sigma Green Belt training course as a key factor in her career development;
“The course not only equipped me to drive meaningful change but also gave me the confidence and skills to take on more strategic roles within the company. It’s been a game-changer for my professional development and has opened up new growth opportunities.”
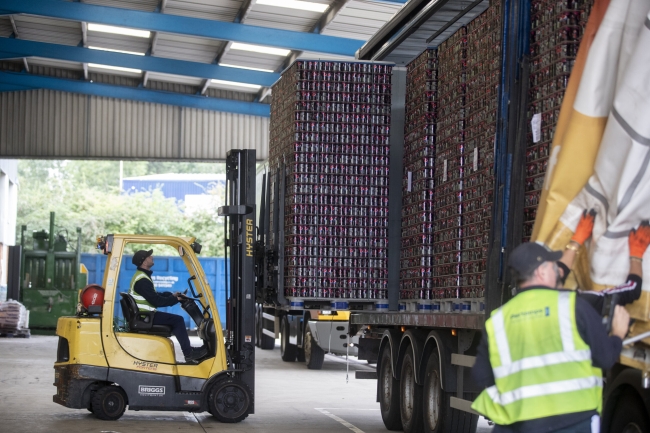
Picture: Britvic
The diverse makeup of her Green Belt cohort was another key to its success, adds Louise;
“Having a team with different skill sets and roles was a real unlock for us. Breaking down siloes and working with people from different parts of the business allowed us to see problems from new perspectives and come up with innovative solutions. This cross-pollination of ideas has been invaluable, and I still reach out to many of those who were on the course with me.”
“The transformation in how our teams now approach their work has been incredible,” says Louise. “CQM’s training didn’t just help us hit target or boost outputs; it fundamentally changed the way people think and feel about their roles. The techniques gained through the course have empowered us to step back, see the bigger picture and make real, impactful improvements. This shift in mindset is massive – not just for individuals but for Britvic as a whole.”
“Having certified continuous improvement champions in every department is a competitive advantage for any business,” says Mark. “Thanks to CQM, we’ve moved to a more disciplined, root cause analysis approach that’s transforming how we tackle challenges. The more people we equip with these practical skills, the better equipped they are to drive meaningful change and the more resilient Britvic becomes.”
The success of the first cohort has sparked widespread interest within Britvic, with the investment in training paying for itself many times over, Mark adds. Now the word is out, the workforce is engaged, with many eager to participate in future cohorts – so much so, that moving forward Britvic plans to put two cohorts through CQM’s Lean Six Sigma Green Belt training each year.