3 minute read • published in partnership with FANUC
Case study: How FANUC CNC ‘made the cut’ for Holroyd Precision
When a UK manufacturer of ultra-precise rotor milling machines required a CNC system for one of its multi-million-pound technologies, it needed to work with a trusted CNC supplier with global recognition. Holroyd Precision was tasked to deliver a rotor milling machine, with internationally-recognised controls which could perform high precision cutting for a leading Chinese manufacturer of refrigeration equipment.
The complex machine required a CNC solution that would be easy for operators to use. Holroyd turned to FANUC UK for support, where it provided its CNC services to the UK manufacturer.
Internationally recognised manufacturing
With 160 years of experience, Holroyd Precision specialises in the design, build and supply of high-precision rotor milling and rotor grinding machine tools. The company’s founder designed and patented a unique thread milling process that utilised a rotating cutter with multiple blades. This machine was ultimately exhibited at the British Science Museum.
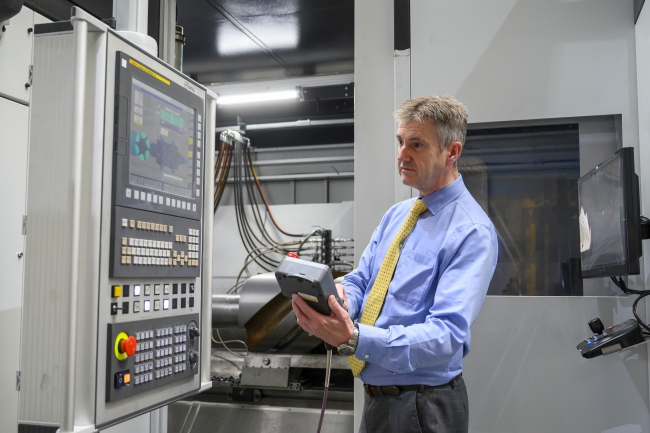
FANUC partnered with Holroyd to provide a CNC system for one of its rotor milling machines / Picture: FANUC
Fast forward to now and Steven Benn, Regional Sales Director at Holroyd, explains how the company prides itself on delivering high precision: “Our grinding and milling machines produce some of the world’s most accurate rotors, gears and threads, which are used in a range of applications, including refrigeration, air compression and gas processors. All built to order, Holroyd machines feature uncompromising levels of innovation and build quality as standard.
“Over the decades, we have established ourselves as a trusted global manufacturer, supplying a number of industries. The Holroyd 8EX, as purchased by our Chinese customer, for example, is essentially a large helical profile milling machine, which uses carbide insert roughing cutters to create a full-depth groove by traversing the cutting tool through a material at the relevant helix angle. Simultaneously, the machine rotates the component in the C-axis, which allows customers to manufacture rotors to a high standard in a timely manner.”
What is the role of the CNC?
The choice of CNC has a big impact on the performance of the machines. Having worked with FANUC since the 1990s, Holroyd Precision contacted the team to see if they could provide a suitable CNC solution for this latest 8EX build project.
FANUC recommended the use of its 31i-MODEL B CNC for the Holroyd 8EX, thanks to its ability to manage highly complex machines with multiple axes, multi-path and high-speed, high-precision machining requirements. Providing the highest performance, accuracy and surface quality, the CNC is partnered with Holroyd’s specially developed human machine interface (HMI).
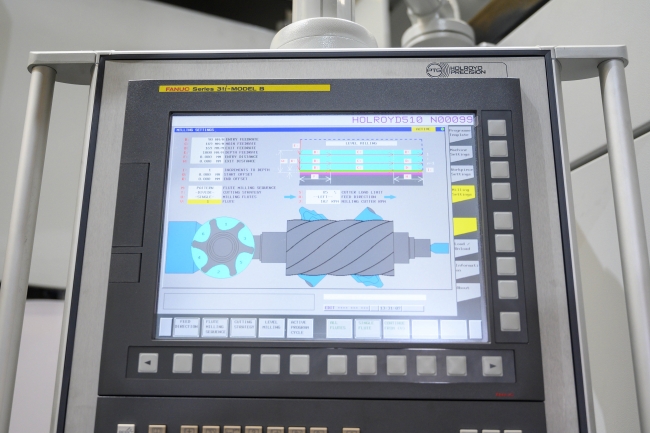
Holroyd Precision was tasked to deliver a rotor milling machine, with internationally-recognised controls which could perform high precision cutting for a leading Chinese manufacturer of refrigeration equipment / Picture: FANUC
The 8EX machine has a special function which requires the linear axis to be linked to the rotary axis. This is achieved through a flexible synchronous drive, which FANUC is able to supply.
Steven Benn continues: “We produce what appears to be quite a complex component. It is in essence a series of helical grooves around a cast iron body, but is actually relatively simple to program. The FANUC CNC, with the specialised HMI, actually allows the programming of that component in a few simple steps. The operation that we have developed with FANUC makes the whole system easy to manage for the operator.”
Holroyd has created a unique probe feedback system for all of its grinding technologies, which scans the ground profile. Working with its unique software to feed any deviations back into the CNC, the machine can then automatically correct the grinding wheel, providing a high precision rotor at a high speed, while simultaneously reducing the number of set-ups required on the machine.
Why customer service is key for Holroyd
Steven Benn concludes: “In today’s production dominated environment, where pressures are there to keep machines running 24/7, we often have to agree our service timescales with the customer. One of the advantages of working with FANUC is that, as a worldwide company, it has service centres around the world meaning the team can support Holroyd in many ways. This, in turn, means we can support our customers in a timely manner.
“When you marry the reliability of the FANUC CNC with the service the team offers, it creates a perfect match. We are really pleased with the final product and look forward to working on our next project with FANUC.”