5 minute read • published in partnership with KUKA
Case Study: The company using KUKA robots to recycle LCDs faster and more safely
An advanced machine made by a University of Limerick spin-out company is using KUKA robots to accelerate the recycling of LCDs that must be depolluted to meet European Union regulations.
About 200 million LCDs (Liquid Crystal Displays) are sold every year in televisions and computer monitors. While they contain products that can be reclaimed for reuse, under the European Union’s WEEE directive for the disposal of electrical goods, LCDs cannot go to landfill and must be recycled. This is messy and hazardous manual work, exposing workers to broken glass and hazardous chemicals, so LCDs must be “depolluted” in the recycling process.
A fourth-generation machine made by Votechnik in Ireland, can automate LCD recycling, making it cleaner and much faster than manual processing. The ALR4000 is the latest version of a “plug-and-play” machine, described as an enabling technology for specialist recycling companies who, hitherto, had struggled with LCD disposal. The machine’s predecessors were originally developed by the University of Limerick with funding from the Environmental Protection Agency. The technology that was patented and then spun-out into Votechnik, which was launched as a new company. The EPA support was secured partly because of the machine’s environmental compliance with the WEEE directive.
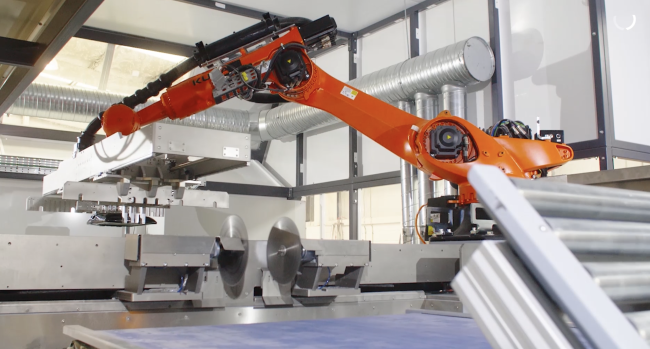
Picture: Votechnik
The ALR4000 is part-funded by a European Commission project that helps bring new inventions to market readiness. It uses a KUKA KR QUANTEC robot to handle the screens through the recycling process and is designed to offer recyclers a turnkey solution.
“A 100% self-contained mini plant is what we wanted; something very simple to operate and that removes any danger or risk to the operator,” says Dr Lisa O’Donoghue, CEO of Votechnik. “During development, we constantly looked at this from the point of view of SMEs, the backbone of Europe, asking the question: how we can help them?” The plant can process up to 60 LCDs per hour, which is more than 10 times the typical manual rate. The work is unpleasant: breaking LCDs creates broken glass, their small fluorescent tubes contain traces of mercury which, along with the liquid crystal content between two glass sheets, must be removed and disposed of in an approved manner. “The previous manual process was very slow, with just three to five screens processed per worker per hour, and staff are exposed to everything from broken glass fractions to contact with mercury,” says Lisa.
A key feature is the machine’s ability to handle variation. LCDs vary enormously in make, size, depth, number of screws and ancillary features like DVD players. Previous attempts to automate their recycling found this a barrier. Votechnik’s latest machine has been designed to process infinite variations.
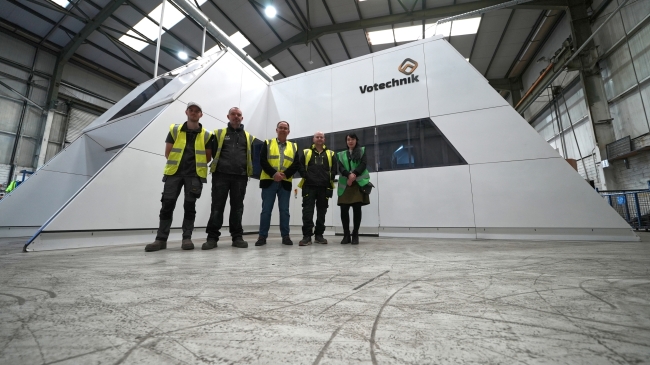
Picture: Votechnik
The process
The LCDs are assessed on entry to the machine using a laser scanning system. The KUKA robot picks up the LCD representing it to a station where the LCD glass front is cleanly removed with a twin cutting saw, the glass panel comes out on one conveyor and can be stacked. the robot then presents the LCD to a second station where the CCFL (cold cathode fluorescent lamp) tubes are removed, and are placed in a sealable container. Negative air extraction over the machine removes any harmful gases; the bad air extracted is cleaned with active carbon filtration built into the machine. The LCD is now depolluted; as the components containing the hazardous material have been removed.
LCDs can now rejoin the normal waste stream at a recycling facility and no longer have to be segregated. “Once LCDs have been through our machine and the hazardous material isolated, PCBs and all of the remainder can rejoin the main waste stream and be shred. Our system allows LCDs to be depolluted quickly and it gives a plant optimization of materials flow,” Lisa says.
KUKA is an essential partner for Votechnik. “Having a robot that can grip the unit securely and move it through the process is absolutely key for us because it can best manage the variation in the system.” This is a big step forward. An early ALR system required LCDs to be manually pushed through the process, because adapting to product variation could not be automated. The KUKA QUANTEC and Votechnik’s process control has solved that. By coincidence, QUANTEC is KUKA’s “greenest robot”, in that the range typically has the highest concentration of recycled parts.
Different designs of grippers can be fitted if specific monitors and TVs are regularly processed, giving the system further flexibility. The size range varies from 12inch to 90inch screens; the latter is more popular in the US market, where screens are much bigger.
The ALR4000 is fitted with remote monitoring, so Votechnik can see how each machine is operating and diagnose faults. “An average recycling facility will not have a team of engineers in-house. Remote monitoring means that we can monitor problems and advise the customer or even fix them remotely,” Lisa says. Its first ALR4000 customers are in Ireland and the company is building out another two demonstrators, one for mainland Europe and another destined for the USA.
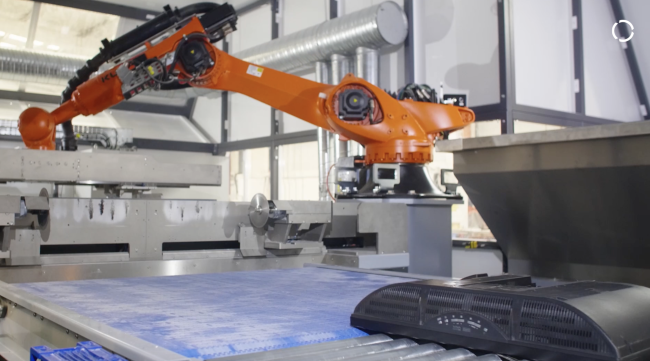
Picture: Votechnik
Unisex industrial design helps
Support is essential to a new, high-tech company as its presence grows abroad. KUKA’s international network provides access to high-end technical services in many countries and gives added confidence. “We are super-focused on great service for the machine, maintaining uptime and keeping happy customers.” KUKA’s market presence and technical abilities was also a major factor.
An interesting point in Votechnik’s product development is the link between robots and the European Commission’s focus on gender equality in awarding funding. Robotics tend to make an industrial process unisex-friendly, removing the physical barriers for female operators, such as heavy lifting. An added feature of the ALR4000 design, is that it can demonstrate that female workers were not disadvantaged in the operation.