7 minute read • published in partnership with Forterro
Feature: How traceability is a manufacturer’s primary defence against product risk
For midmarket manufacturers, risk comes in many guises. It is a challenging environment, from ongoing attempts to navigate post-Brexit trade complexity and red tape to supply chain vulnerabilities and from talent shortages to the ever-growing cybersecurity threat. Forterro looks at how traceability can be a primary defence against product risk for manufacturers.
There are even risks associated with a manufacturer’s main focus – the design, creation and distribution of products:
• What happens if a problem with a product emerges?
• How easy is it for a manufacturer to know what the source of the problem is?
• Was it a faulty part?
• Was the manufacturing process not followed correctly?
• Did something go wrong in testing?
• Getting to the route of the issue is one thing, but then how many other products are affected?
• How many have been shipped, and what customers have they been sent to?
The level of traceability in your organisation determines the level to which you can answer these questions. This governs how quickly and well you can react to the situation and ultimately mitigates the potential long-term reputational damage that could come with a failure to respond in a timely and effective way.
ERP software or MRP software can play a significant role in helping to mitigate risks of all types. However, not all ERP solutions are the same. Many contain isolated modules where information can only be captured at certain points, but true traceability is something that touches all aspects of a system and some ERP solutions such as 123Insight have traceability interwoven throughout the system as standard. Only these systems can truly provide the confidence to a manufacturer that they are able to manage product risk effectively.
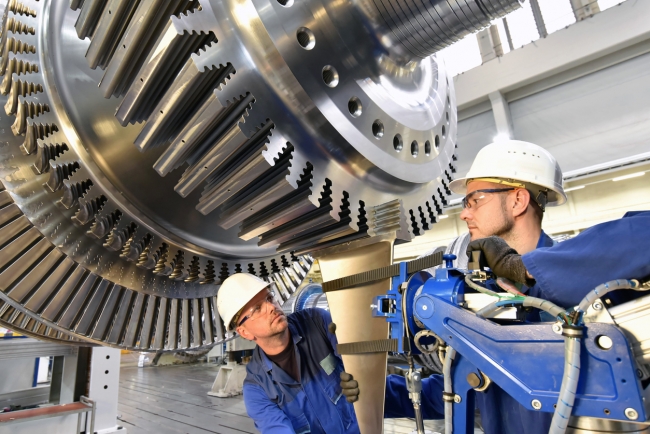
Picture: Getty/iStock
What is traceability?
Traceability is essentially the monitoring, recording and tracking of products, parts, and materials throughout a manufacturer’s end-to-end processes, from initial goods in, through assembly and production and on to final delivery.
It is the ability to look at a part and see where it started its life and where it concluded, and everything that happened to it in-between. But it is also the ability to expand upon that journey to see the associated lifecycle of the parts, tools or materials it has interacted with along the way, such as which test rig was used to test the assembly and when was it last calibrated? What adhesive was used to assemble the part? Who supplied it and when did it expire?
Traceability can range from the very simple to the extremely complex and all-encompassing. Different levels are required depending on the industry, the levels of certification, and the types of customers a manufacturer is working with.
So, why should manufacturers prioritise traceability?
Traceability drives quality
Traceability is key to driving quality. To properly understand what is happening in your business and how manufacturing is performing, you will log, record, and document certain steps and actions. This is traceability in its most simple form.
If you have a product that is failing end of line testing, you will want to isolate the issue down to a particular part, such as a PCB, during that test. However, without proper traceability, you will be unable to link that failure to a specific batch or delivery to investigate if the issue is contained. What if you have more than one supplier for a part? Without traceability you won’t know whether the overall design or specification of the part is wrong or if one of your suppliers has delivered a faulty product.
You may find errors are slipping into your manufacturing process but you don’t know where or why. With proper traceability, you can see which machines and operators were working on the products that contained the errors and identify common trends or opportunities for some retraining or re-education.
Access to real-time information delivers vast efficiency gains and confirms that product quality standards are met. Not only is this much quicker than when these actions are carried out manually, but the chance of human error is all but eliminated. It frees up employee time to be spent elsewhere in the business, and by reducing tedious and monotonous tasks, it can help with job satisfaction and even improve employee retention.
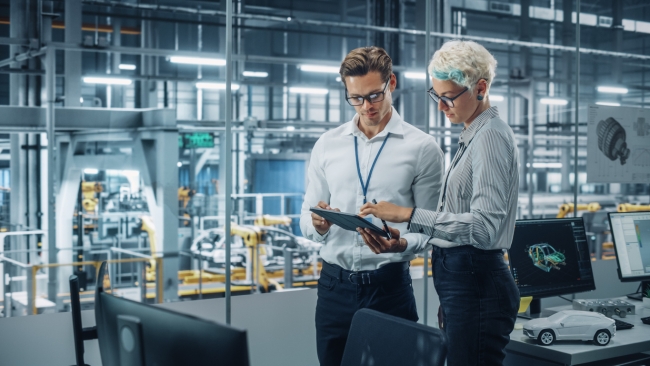
Picture: Getty/iStock
Traceability enables certification
Good and demonstrable traceability is a key requirement to achieve high-quality certification. While ISO9001 is a staple, aerospace and automotive certifications such as AS9100 and IATF 16949 take this further. Having a robust and auditable system is key to achieving product certifications such as ATEX and DNV.
Without high levels of traceability in your manufacturing process, these standards are impossible to meet and certifications are not achievable. But with good traceability built into a reliable system, they can allow you to compete in new and international markets and provide assurance to your customers that you are a credible and trustworthy partner.
Traceability reduces the impact of product recalls
A product recall is something no manufacturer wants to face. They can be hugely expensive, both in terms of the immediate recovery and correction of the issue but also the long-term impact, fallout and reputational damage.
It is true that good traceability often leads to improvements in the quality of your products but should the day come when a product recall is needed, a manufacturer has to ensure they can act quickly and accurately but also with as minimal impact as possible. This is where the level of traceability you have in your manufacturing operations becomes paramount. If you identify a faulty process or part but have limited traceability, you will likely only be able to identify when you may have been producing a group of faulty products.
Some ERP systems provide the ability to enable batch number traceability which would allow you to hopefully focus even further, both in identifying which batch a faulty component part came from, and also which subsequent batches of product the parts were used in. However, using an ERP system with traceability at the forefront, such as 123Insight, batch traceability is automatically built into the system throughout. Furthermore, it has multiple serialisation options and Advanced Serial Tracking, enabling you to really focus and identify exactly which end products are affected.
If you can isolate your end product down to a certain few serial numbers rather than one large batch or only those products produced between two points in time, suddenly the scale of the product recall becomes much smaller. The cost and its lasting impact is much more manageable and ultimately could be the difference in whether you keep or lose customers.
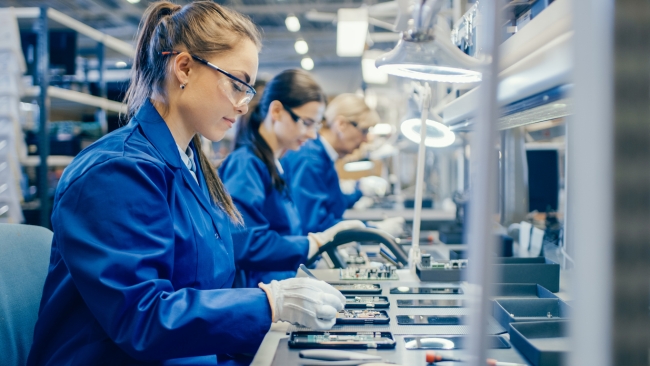
Picture: Getty/iStock
ERP and MRP software and traceability
Traceability is not something that has only existed since the introduction of ERP or MRP systems. Manufacturers have always recorded information, captured results, and stored that information. Traceability has always been there, but not necessarily fully connected end-to-end traceability and not easily attainable. This is one of the key benefits of an ERP system.
All the information that needs recording and logging is stored in one place. For the most part, information can be tracked directly in the software, certainly the issuing of components to production and the logging of production activity. Even when it comes to the information outside of your control, suppliers’ delivery notes or test results for example or perhaps engineering drawings, these can all be added to the system.
This was especially useful to 123Insight customer Inoplas Technology Ltd, which provides plastic injection moulding and over-moulding manufacturing services. The ability to link any type of document within 123Insight was hugely beneficial, according to Managing Director, Jon Brooks:
“The ability to have sales orders, purchase orders, despatch notes, engineering drawings, etc., tied into part numbers and then available throughout the system is very useful for interdepartmental knowledge transfer and cooperation.”
Another way an ERP system helps with traceability is by automatically capturing and linking information together. By performing processes using the system, the ERP software links everything behind the scenes. When you need to investigate and look at the details, it is all easily and quickly available.
But it goes further than that. A good ERP system can control each step of your process, ensuring that production can’t move forward without all the correct parts being issued. Such controls mean that not only do you have the inherent underlying traceability a system like 123Insight provides, but you also have high-quality and detailed information throughout.
Get the right traceability level for your business
Traceability has undoubted benefits to the business but it’s the level of traceability that requires careful consideration. Deeper and more thorough traceability ensures a cohesive system of control and puts your manufacturing in the best possible position to shine when an auditor comes knocking or minimises the impact when navigating a product recall. However, you don’t want to create a system that is unnecessarily overcomplicated or admin-heavy to maintain.
A good ERP system should support whatever level of traceability you need in your business and do so in a way that saves time and reduces admin overhead. 123Insight has been designed with traceability at its core so that parts are effortlessly tracked through their entire journey, logging where the part was used, which machine and operator handled it, the exact date that it happened and where it ended up. It’s also easy to access any paperwork, purchase orders, or invoicing relating to that part.
Traceability helps you remain compliant, be more efficient, and minimise the operational risk and potential long-term reputational damage associated with product recalls but can also help deliver a competitive advantage.