5 minute read • published in partnership with Atlas Copco
Feature: Why air compressors are becoming the latest technology with OPC UA capability
OPC UA is the single universal communication protocol for industrial connectivity and control. When machines can communicate and understand each other, processes run more smoothly. But up until recent times, air compressors have not been able to offer OPC UA interconnectivity to other production equipment, with some remaining mostly offline and others using different communication protocols. Atlas Copco explains why this has changed.
This post-pandemic era has seen major changes in working practices and challenging issues in the production environment resulting from the new normal − everything from the ability to shift to remote operations and control, the need for operational resilience and sustainability, to the implementation of cybersecurity protection.
So there has never been a more appropriate time within industrial operations for the standardisation of production equipment connectivity and communication; the need for a single framework for secure interoperability and information exchange and a common technology from cloud service providers to control and process multiple types of production hardware. Put simply, a universal language for connected machines.
Seamless communication is becoming a reality, with the increasing adoption of OPC UA (Open Platform Communications Unified Architecture) machine-to-machine communication protocol developed specifically for industrial automation. It is a universal language for machines in a production environment, enabling them to be connected and run as a more reliable and efficient system. It is a development that is particularly relevant to the integration of air compressor systems.
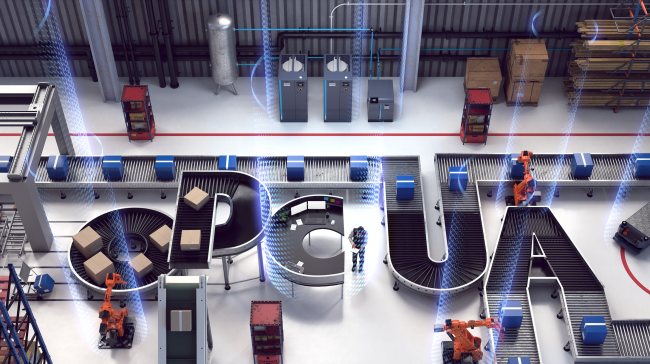
Picture: Atlas Copco
Compressors with OPC UA capability
An increasing number of vendors already offer OPC UA-capable technologies, and more products are being added all the time. For example, the world-leading compressor systems technology developer Atlas Copco has launched its first compressor range.
Atlas Copco is dedicated to the seamless, secure, and optimal integration of compressed air systems into production plants. As an innovation leader in this field, the company is aware that the application of OPC UA communication technology is essential to achieving this goal.
As a Class A member of the OPC Foundation, the company has put theory into practice by being the first to introduce OPC UA-enabled compressors. Because, as the heart of a production process, compressors are too important to not be a part of Industry 4.0.
Atlas Copco’s GA 22-37 VSDS and the GA37+ – 45+ range of oil-injected screw compressors are the first models now available with OPC-UA as an integrated part of the controller, a milestone in compressor integration. Their plug and play installation makes the setup and harmonisation with other equipment extremely easy.
It is intended that these introductory machines will be followed soon by other oil-free and oil-injected compressors, as well as auxiliary equipment that will also incorporate OPC UA technology
How does OPC UA work?
A crucial step in achieving a connected production environment, OPC UA was developed as the successor to the traditional OPC standard. According to the OPC Foundation, it is already the “most widely adopted interoperability standard for secure, reliable and platform-independent information exchange in the world.”
While most technologies are designed for a single application, OPC UA is much more flexible. It offers connectivity benefits throughout an entire production process, i.e., it allows different technologies to “talk” to each other without the risk of miscommunication. This ensures a smoother production environment, especially with regard to automation.
The ultimate objective is to ensure that all business and control information can be based on a single source of relevant data in order that companies can maximise growth, productivity, and profitability. Standardisation, however, is only one benefit of OPC UA technology.
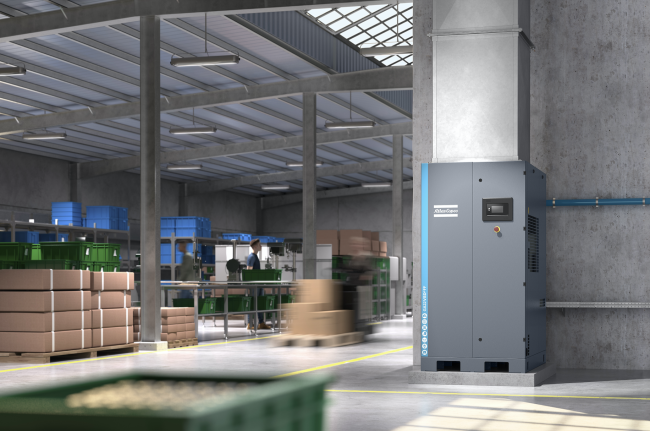
Picture: Atlas Copco
What are the other benefits to be gained from OPC UA?
OPC UA is an important step toward Industry 4.0. It is the standard that solves interoperability challenges and acts as an ecosystem enabler to ensure that multiple open standards, such as Industry 4.0, NAMUR NOA, OPAF and Ethernet APL can work seamlessly together.
Furthermore, the versatility of the platform offers a range of benefits that go far beyond simply standardising machine-to-machine communications:
Security In a world in which hackers get more sophisticated and more and more equipment is connected online, the security of sensitive machines also has to improve to keep ahead of potential threats. OPC UA technology has security built into its design and is a firewall-friendly platform that features a variety of encryption levels, as well as authentication, auditing, and user control.
Platform independence OPC UA is not tied to any specific operating system or programming language. That means it can be used on different hardware platforms, such as PC hardware or cloud-based servers, and is compatible with the majority of Windows, Apple OSX, and Android operating systems, as well as others.
Extensibility While OPC UA has already proved its worth; it is a very future-oriented system that is designed to incorporate the technologies of tomorrow. In other words, it is capable of accommodating technologies yet to be developed while continuing to be backwards compatible for existing products even as it evolves.
Functional equivalence OPC UA is an extension of the original OPC technology, which can still be integrated easily into any new and improved system.
Smart insights and improved productivity
Finally, the application of OPC UA technology will make it much easier for an industry operator to gather data from all of its different machines and to optimise production operations.
Atlas Copco’s OPC UA-enabled compressors can be combined with other innovative systems: Atlas Copco’s well-established SmartLink cloud platform offers insights, dashboards to enhance energy saving, and the possibility to let the system supplier take on total responsibility for a compressed air installation. Together, OPC UA and SmartLink offer the benefits of real-time on-site and remote monitoring, as well as smart insights and improved productivity opportunities, from anywhere in the world.