2 minute read • published in partnership with igus
From e-chains to Storm Boards: the igus circular product lifecycle
Energy chains or e-chains are used to protect and guide moving cables and hoses, ensuring reliable power and data supply for moving machinery. They can be found in hundreds of industrial applications from offshore oil platforms to machine tools, from cranes to theatres, from elevators, to vehicle doors.
e-chains made by motion plastics specialist igus are designed to last millions of movement cycles, for example 10 million movements or three years’ service life are guaranteed in most cases. But at the end of their lives, these technical and durable plastic products are typically not recycled but scrapped.
igus has now launched a programme called “chainge” so that customers can return these used chains, and indeed energy chains from any manufacturer, for recycling. The first batches of customer e-chain returns have now been recycled in a circular way allowing igus to reuse them for construction hoardings and exhibition stands. Over 22 tonnes of e-chains, sourced from any energy chain manufacturer, have now been collected for recycling by igus Germany and more than three tonnes in the UK.
The first customer e-chain returns in the UK came from an airport elevator and a large-scale metal component machining site. These were sent to igus’s recycling partner, MyWaste in Hull, where they are remanufactured into Storm Boards – a proprietary name for versatile structural plastic boards.
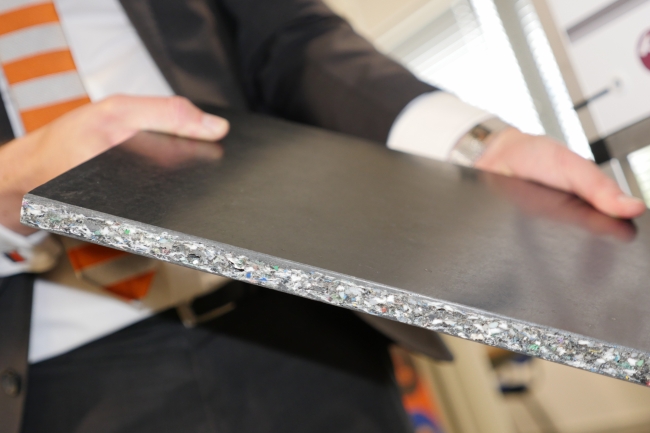
The igus chainge programme allows energy chains to be recycled and remanufactured into Storm Boards / Picture: igus
The recycling process comprises several stages. The first stage is size reduction, using a shredder to reduce the size of the parts to around 20mm. The plastic pieces then enter a granulator, further reducing the material size to make it suitable for blending. The e-chain material is now fed into a mixer where it is blended with single-use plastics like mixed packaging to make the perfect homogenous material for the board production.
The board production stage is essentially like a giant waffle-making machine with hot plates that melt and cure the board mixture. Firstly, a skin of finely ground, single polymer plastic is spread over the plates. Then the mixed material, including the e-chain polymer, is evenly spread across the plate, which provides the board’s core. The system is closed and heated and once cured it is removed, trimmed, cooled and quality checked.
Storm Boards have a variety of uses from making furniture and shop fittings to any area in construction where timber products would have been used. “We see it as an eco-alternative to wood and it has provided a new use for plastic materials that are not currently recycled,” says Mike Derbyshire, MY Group Site Manager.
igus offers customers free display stands which are installed at their premises and come with a range of igus product samples for them to test. In the past the panels and shelves on these were made from energy intensive aluminium but are now made from Storm Boards containing the recycled energy chains. In this way the life of the product becomes circular, saving resources and costs.
You can find out more about the chainge programme here.