5 minute read • published in partnership with CQM Training & Consultancy
Insight: Foundation for success – the secret to creating a future-ready manufacturing workforce
The level of change and uncertainty in manufacturing makes upskilling workers a vital part of staying competitive. Yet, with limited resources and conflicting priorities, many struggle to identify and implement the right training. Andy Cheshire, managing director at CQM Training and Consultancy, explains how this process can be simplified by aligning workforce development with strategic goals – benefiting manufacturers and employees alike.
Three in four UK manufacturing business leaders (75%) cite skill shortages* as their biggest barrier to growth. This is followed by recruitment (36%) and retention (32%), meaning the top three barriers to growth are all people-related. Even when businesses receive a high volume of applicants, the right skills don’t always follow. As a result, over half of manufacturers (52%) are planning to invest in developing their existing workforce** in the coming year.
Given the ongoing labour shortage, it’s not surprising to see manufacturers looking in-house to find the future-ready skills they need. However, the primary focus is on IT and digital skills – reflecting the ongoing push for automated and connected factories. While raising digital literacy is important, not least in helping companies unlock the potential of their data, manufacturers also need to prioritise foundational skills like continuous improvement, Lean Six Sigma and change management.
These skills apply to every role, at every level, in every organisation, and are the backbone of operational excellence, driving efficiency and innovation across the business. Yet are often overlooked because manufacturers lack a clear strategic vision for workforce development.
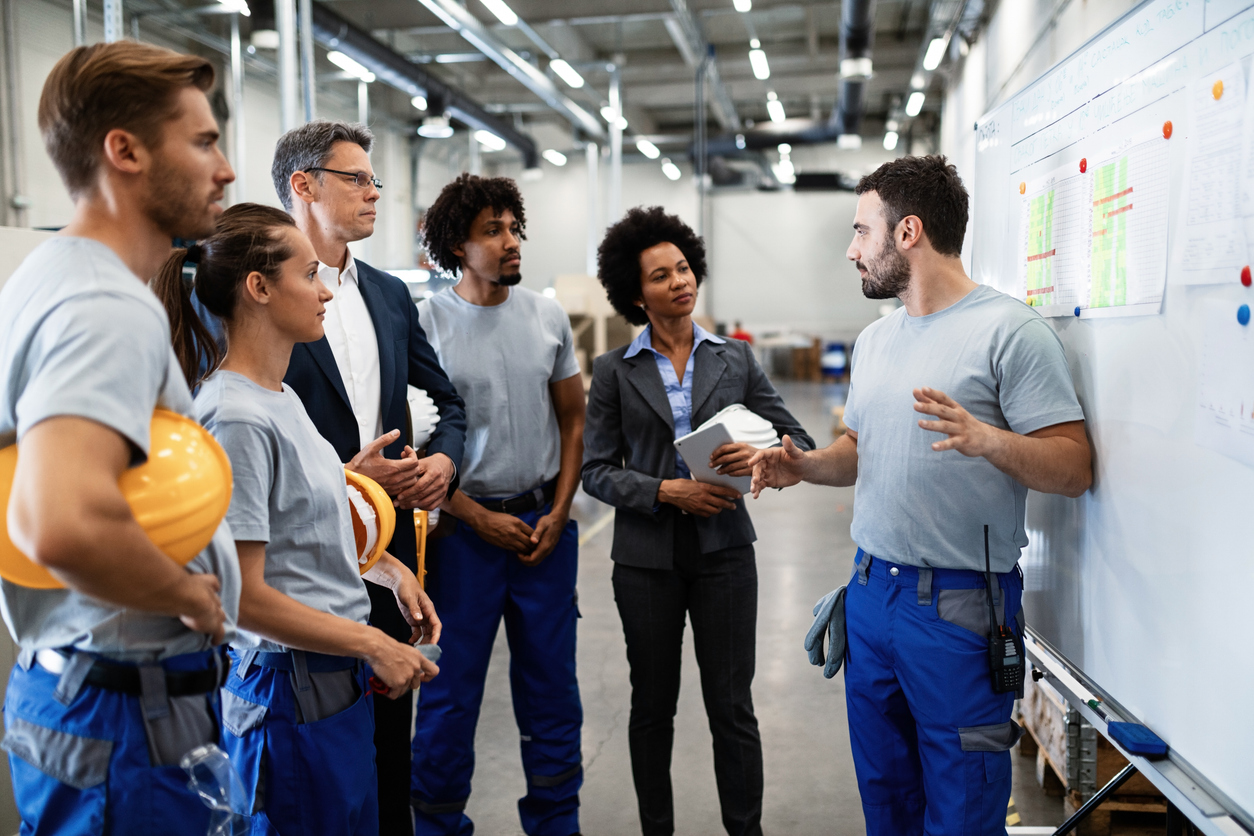
Picture: Getty/iStock
The pitfalls of quick fixes
Manufacturers often find themselves overwhelmed by the sheer volume and variety of technology available today. In their quest to stay competitive, many resort to point solutions designed to fulfil a specific need but offer little beyond that. These quick fixes often fail to integrate with broader systems, resulting in inefficiencies and wasted resources.
The underlying issue is a lack of vision, which forces decision-makers to act instinctively or reactively rather than strategically. Instead of stepping back to define clear objectives and align investments with long-term goals, manufacturers focus on addressing immediate problems. The result is a fragmented approach that undermines sustainable growth and operational excellence.
The same challenge applies to workforce development. Training programmes are often narrowly focused on filling immediate skills gaps or addressing specific technical needs. While this may solve short-term problems, it rarely contributes to long-term capability building. For example, training someone to operate a new machine won’t prepare them to troubleshoot issues or find process improvements. By contrast, equipping employees with problem-solving techniques can be applied to any process, in any area. If you teach someone how to use Microsoft Excel, they’re limited to Excel. But if you teach someone how to visualise data and solve problems, they can tackle issues anywhere.
Empowering employees drives business growth
The right training won’t just benefit the bottom line, it transforms employees into engaged, innovative problem solvers. When businesses take a holistic, long-term approach to training, they build a workforce that’s motivated, capable and invested in the company’s success.
For example, Britvic faced operational challenges that required a more focused and scalable approach to continuous improvement. They turned to CQM Training and Consultancy to deliver practical, real-world training to drive sustainable business change. With the help of CQM, they introduced Lean Six Sigma Green Belt training, focusing on real-world projects that empowered employees to solve problems at the root cause. The impact was immediate:
• Downtime on one bottling line fell from three hours to just 17 minutes,
• Capacity on another line increased by almost 200 hours annually,
• and supply chain optimisation saved the equivalent of 18 cars’ worth of CO2 emissions.
Collectively, these projects are expected to generate more than £4.1m in annual cost savings, while equipping employees with skills and tools to drive further improvements. For Britvic, the right training didn’t just solve a need, it created a culture of innovation and workforce engagement – future-proofing Britvic for years to come.
In 2024 alone, if we look at all the CQM projects delivered through employees at customer sites, we’ve delivered over £100m of annualised savings.
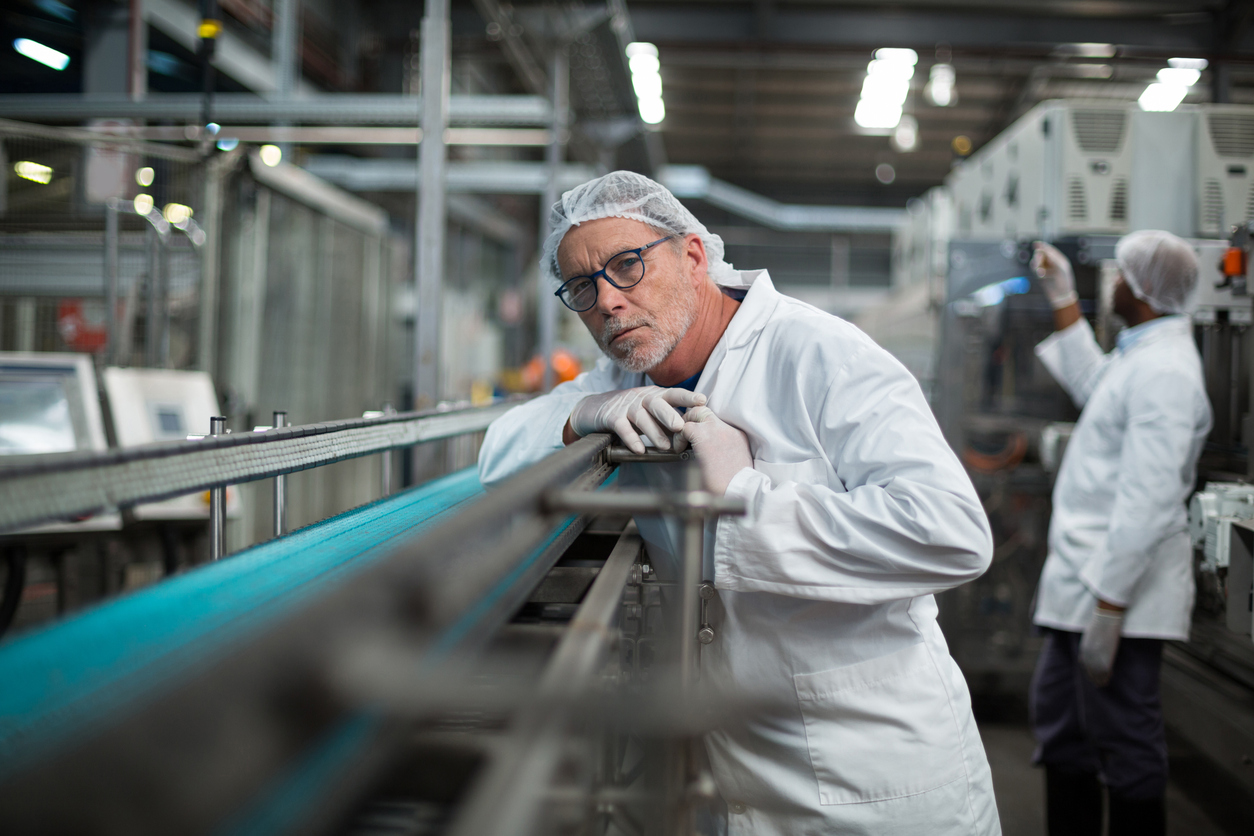
Picture: Getty/iStock
A broader vision for workforce development
The need for manufacturers to adopt a broader, more integrated approach to training has never been greater. Rather than reacting to immediate needs, training should align with long-term business objectives and support employees in building meaningful careers.
When organisations combine technical training with leadership development and continuous improvement, they create pathways for progression that motivates employees to stay and grow. This holistic approach creates a workforce equipped not only to handle today’s challenges but to anticipate and overcome tomorrow’s as well.
CQM removes the guesswork from workforce development, providing clarity and confidence in choosing the right training. Here’s how we do it:
• Collaborative Assessment: We take the time to understand your organisation’s needs, challenges and strategic objectives.
• Tailored Development Plans: Our courses and programmes are flexible and personalised, ensuring they align with your operational goals and existing initiatives.
• Seamless Integration: Development is designed to complement your broader business priorities, enabling smoother implementation and faster results.
• Practical Focus: Our programmes emphasise real-world application, equipping employees with the skills needed to solve problems, embrace change, inspire others and drive continuous improvement.
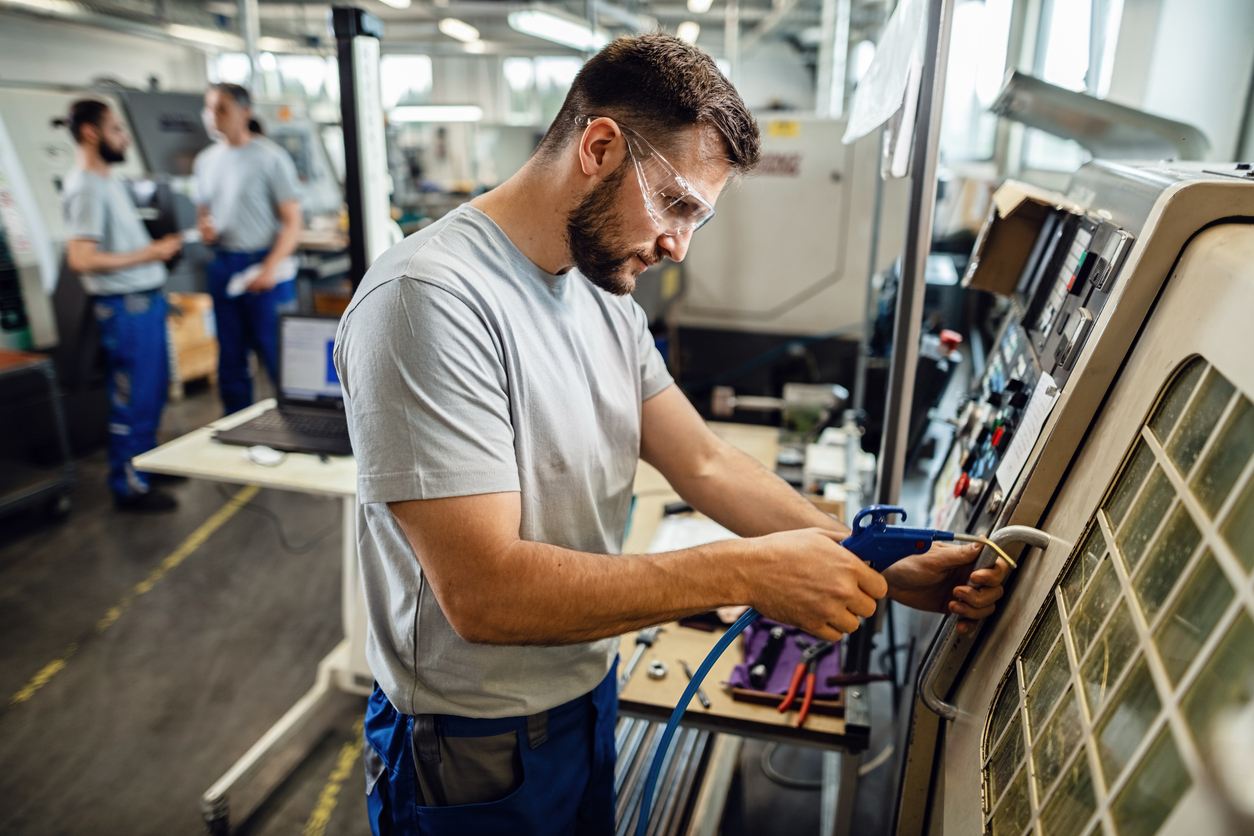
Picture: Getty/iStock
The time to act is now
Training isn’t just a solution to today’s problems; it’s the foundation for tomorrow’s success. With a clear, forward-looking strategy, manufacturers risk falling behind in an industry that’s evolving faster than ever.
The right training isn’t a “nice to have” perk or a box-ticking exercise – it’s a business-critical investment. It equips employees with the skills and confidence to drive meaningful change, turning challenges into opportunities and unlocking untapped potential across the workforce.
At CQM, we partner with manufacturers to identify skills gaps, prioritise strategic goals and craft tailored training roadmaps that deliver practical, business-focused outcomes. By focusing on real-world application and measurable results, we help businesses embed a culture of continuous improvement that fuels innovation, growth and resilience.
The future of manufacturing will be built by those who invest in their people with the right training. With 52% of manufacturing already planning to upskill their workforce in 2025, the question is: will you join them, or risk being left behind?