4 minute read • published in partnership with L2L
Insight: How can manufacturers set realistic digital transformation goals and milestones?
By today’s standards, Digital Transformation (DT) is no longer just a luxury – it’s necessary for companies to adapt to business demands and keep up with the competition. However, with all the urgency to get a strategy in place, it is easy for companies to find themselves ending with results lower than initial expectations. Eric Whitley from L2L shares some key areas to consider to ensure that you are setting realistic DT goals and milestones.
Understanding value
An essential part of setting goals is understanding where the value lies. After all, digital transformation is a business decision that aims to accomplish long-term objectives and meet the demands of the enterprise.
From a manufacturing standpoint, value relates to improving production processes. The benefits of digitalization can manifest themselves through cost-effectiveness, increased quality, and higher productivity. Recent times have highlighted other timely advantages such as adaptability, flexibility, and business continuity.
For instance, a company that sees the value in productivity may focus on utilizing digital tools to achieve a set target. A project as straightforward as real-time staff availability monitoring can quantitatively increase productivity. An aerospace company demonstrates this practice by first identifying scheduling as the root cause of wasted time. After recognizing the potential value from unused time, leveraging digital tools to track utilization allowed them to achieve a 20% increase in productivity.
Early adopters of newly available technologies can showcase the real-world benefits of digitalization. The first step is acknowledging that there are areas in the current process that can be improved. Digitalization then comes in to build upon and intensify the potential sources of value.
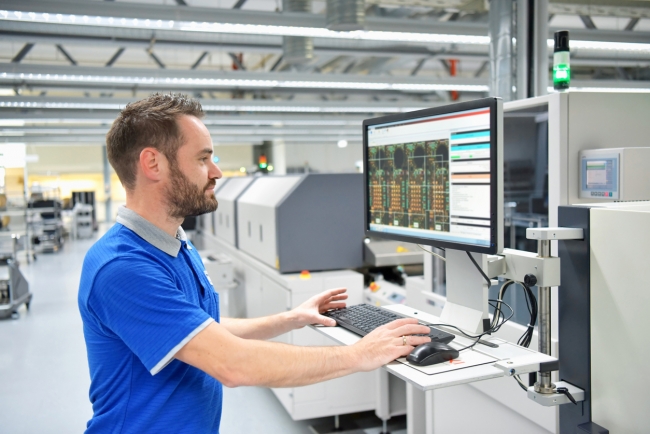
Picture: Getty/iStock
Identify opportunities for improvement
Setting realistic goals and milestones starts with an objective assessment of the current state of the business, particularly the digital maturity of a company. Companies need to evaluate how far they need to take their DT journey before the benefits materialize. Identifying opportunities for improvement requires adept planning by assessing the present situation and the infrastructure and process changes to achieve success. Throughout the process, data is consistently a driver for making decisions.
Depending on the size of operations, manufacturing companies can have a vast array of machines and operating processes to comb through when searching for an opening for improvement. While this sounds like a tedious endeavour, the good news is that modern tools are not limited to execution but go as far as data analysis and collection.
A practical start in any digital transformation would be to deploy a comprehensive manufacturing platform that allows information sharing between assets. Today’s “smart” solutions include applications that can capture real-time data that lends itself to analysis and valuable insights.
Examples of applications that can collect massive amounts of data include Computerized Maintenance Management Software (CMMS), Enterprise Asset Management (EAM) software, and Smart Manufacturing Platforms. By installing sensors throughout a facility and allowing a program to gather and analyze data, companies can report more easily on areas that can benefit from digitalization. Opportunities for robotic automation, predictive maintenance, or even AI-driven inspections can arise from looking into the data.
Set expectations and priorities
Companies are bound to have expectations of what they think are the benefits of digital transformation in manufacturing. These expectations can form a spectrum of optimistic views and rather conservative projections, combined.
Positive expectations include those that relate to the potential advantages of digitalization. For instance, out of survey respondents, 50% of manufacturers are looking forward to reduced costs through DT, while 35% anticipate reliability improvement.
On the other hand, there are expectations from companies engaging in DT that tend to underestimate the capacity of the initiative. For instance, more than a third of respondents from the same survey anticipate that it would take more than two years from implementation to achieve success. In contrast, only 10% believe that results can emerge within six months. While DT incorporates a lot of high-tech innovations that can be technically intense, taking years for implementation is not necessary.
When setting expectations and priorities, it pays to take a data-driven approach. It is in the best interest of companies to set their focus according to the assurance of the returns. For instance, with competing projects that require substantial resources for execution, prioritization needs to take place. Judgment dictates that a strategy with a clear return on investment takes priority. Again, this can only be possible with sufficient data points and proper analysis.
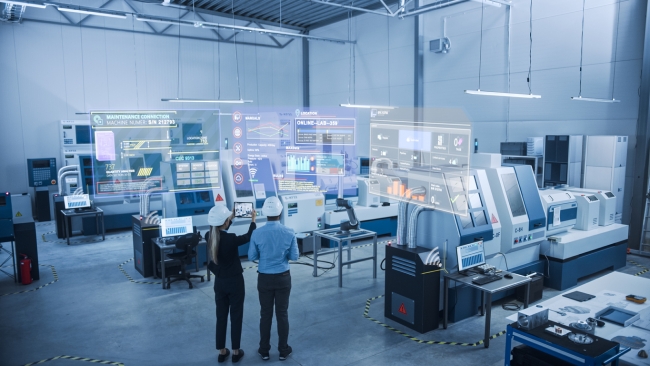
Picture: Getty/iStock
Invest in the right systems and talent
Whatever benefits companies are looking to get out of DT will require the right tools and processes to be in place. Of course, to generate value, companies need to maximize the returns of what they spend.
Remember that new and innovative infrastructures need to go hand-in-hand with the proper skills and talents required. Complex systems that can handle intricate tasks may require more specialized talent. Additional training or even outsourced help are viable options to address these gaps.
Benchmarking is a practical start in identifying the right amount of resources according to the size of the company’s operations. By comparing similar plants and manufacturing processes, companies can gauge the platforms and levels of service that make sense.
Conclusion
Different companies will have varying degrees of maturity in their DT journey. It is, therefore, crucial to take an objective approach in assessing the current and future states of the enterprise. Whatever stage companies find themselves in DT, you can never go wrong by taking a data-driven strategy.