4 minute read • published in partnership with ITI Group
Insight: How to build an effective asset maintenance strategy in manufacturing
High maintenance costs from unplanned downtime, equipment faults, breakdowns and lost production due to issues with quality, time or speed are common pain points. Unplanned maintenance often results in lost production, higher part costs, and longer repair times – costing significantly more than planned maintenance. With businesses under extreme pressure to improve efficiency and do more with less, ensuring maximum equipment availability to increase production capacity and efficiency is vital. Nik Tankard from ITI Group shares his insight on why maintenance, when managed correctly, offers great value to manufacturers.
Regular equipment maintenance is not only important for ensuring uptime but also plays a critical role in overall workplace safety. ‘Maintenance’ covers many activities such as inspection, testing, measurement, replacement, and adjustment, and is carried out across all sectors and workplaces.
Proper maintenance significantly reduces the risks associated with workplace hazards, contributing to safer and healthier working environments. Equally, insufficient or inadequate maintenance can lead to serious, and potentially fatal, accidents or long-term health issues. According to PUWER (The Provision and Use of Work Equipment Regulations 1998), all work equipment must be “maintained in an efficient state, in efficient order, and in good repair.”
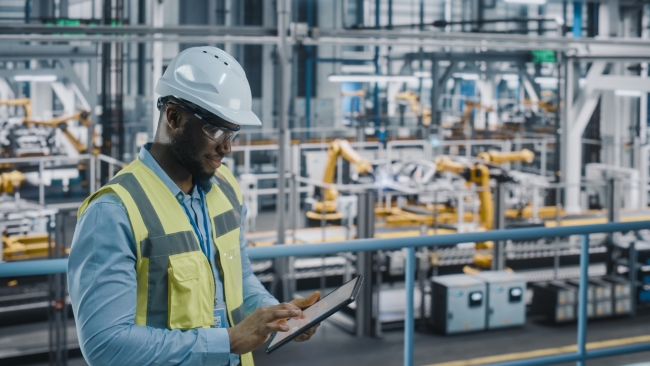
Picture: Getty/iStock
But is meeting the bare minimum regulatory compliance enough? Is it cost-effective, and can exceeding these requirements offer additional benefits?
Maintenance strategies in manufacturing
There are several maintenance strategies employed in manufacturing. The choice of strategy depends on factors such as the type of equipment, the production process, and the specific goals of the facility.
1 – Reactive Maintenance: Also known as “run-to-failure” maintenance, this strategy involves repairing or replacing equipment only after it has failed. While this approach can save costs in the short term by avoiding unnecessary maintenance, it is generally not recommended for critical assets in manufacturing due to the high costs associated with unplanned downtime and potential safety risks.
2 – Preventive Maintenance: Preventive maintenance is a proactive approach that involves regularly scheduled inspections, servicing, and repairs to prevent equipment failures. By adhering to a maintenance schedule based on time intervals or usage metrics, manufacturers can catch issues early and address them before they cause significant problems. This approach helps extend the lifespan of equipment and reduce the likelihood of unexpected breakdowns.
3 – Predictive Maintenance: Predictive maintenance leverages data analytics, sensors, and machine learning to predict when equipment is likely to fail. By monitoring key performance indicators (KPIs) such as vibration, temperature, and pressure in real time, predictive maintenance allows manufacturers to identify potential issues and schedule maintenance only when necessary. This strategy minimises downtime, reduces maintenance costs, and optimizes the use of resources.
4 – Condition-Based Maintenance: Similar to predictive maintenance, condition-based maintenance focuses on the actual condition of the equipment rather than relying solely on time-based schedules. This approach involves continuous monitoring of equipment health using sensors and diagnostic tools. Maintenance is performed only when specific indicators show signs of deterioration, making it a more efficient and cost-effective approach.
The benefits of preventive maintenance
Preventive maintenance involves regular, proactive servicing of equipment to catch potential issues before they lead to failure. By following a consistent maintenance strategy, businesses can catch potential problems before they occur, preventing equipment failure. But with so many other competing priorities, is now the right time to invest?
Well, in my experience, implementing strategic maintenance and ensuring equipment availability will not only boost confidence but also enhance corporate reputation. While the initial costs of preventive maintenance may seem high, the long-term benefits far outweigh the costs. In the long run, preventive maintenance extends the lifespan of equipment, reduces maintenance costs, and minimises the risk of unexpected failures – making it a valuable investment.
Improving OEE within a production line by just 1% through implementing preventive maintenance can result in significant financial returns when considering factoring such as:
• Equipment costs
• Repair costs
• Depreciation
• Energy usage
• Labour costs
• Increased productivity
• Higher yield
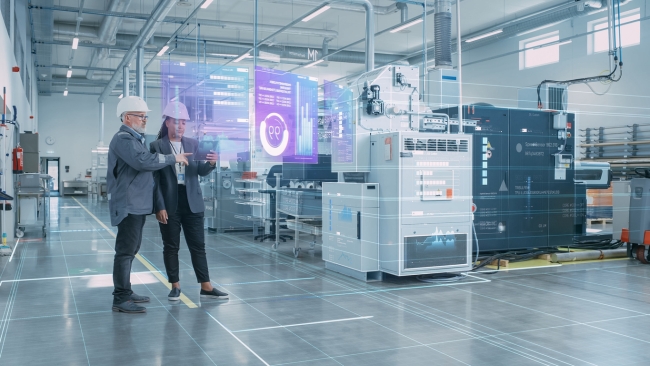
Picture: Getty/iStock
How do you know whether your maintenance is effective?
Does your maintenance support increased productivity? Generally, there are a few KPI’s recognised across the industry, but the process starts with benchmarking. No matter how effective your exisiting system feels, there is always scope for improvement. By benchmarking KPIs such as MTBF (Mean Time Between Failure) and MTTR (Mean Time to Respond) you can ask yourselves 3 questions:
• Where are we now?
• Where do we want to be?
• What do we need to do to get there?
By monitoring these benchmark KPIs when implementing strategic maintenance, results can be very quickly visualised and quantified, providing insight into the effectiveness of your efforts.
The role of technology in asset maintenance
Digitalisation and real-time data are becoming increasingly essential across all sectors of manufacturing. As a result, digital technology is playing an ever-growing role in maintenance processes. With advancements such as remote digital connectivity (IoT sensors), Digital Twins, Data Analytics, Artificial Intelligence (AI), Computerised Maintenance Management Systems (CMMS), and Enterprise Asset Management (EAM), maintenance operations are becoming significantly more efficient and adaptable to the evolving demands of modern manufacturing.
Effective asset maintenance management is key to the success of any manufacturing operation. By implementing effective maintenance strategies and utilising modern technologies, manufacturers can reduce maintenance costs, maximise asset value, minimise downtime, improve equipment performance, and ensure safer, more efficient operations.
To find out more on how you can build an effective asset management strategy visit: ITI Consulting