3 minute read • published in partnership with Stäubli
Insight: Redefining the factory of the future to meet today’s manufacturing challenges
The perception and vision of the “Factory of the Future” continue to evolve with each new generation of technologies, as they in turn achieve the objectives and ambitions of the past. The once generally accepted vision of future manufacturing, that of lights-out, high-volume production, has been achieved to a degree in certain areas. However, the changing demands of markets and customers alike mean that manufacturers must continue to evolve their production processes to keep pace. Simon Jenkins from Stäubli looks at the changes in manufacturing concepts which will address the challenges faced by manufacturers not only today but in the future.
Today we have already surpassed many of the initial ideas of what the factory of the future might look like, as robots and automation continue to find their way into new market sectors and a host of new applications. Companies that invested in these technologies in the past have certainly benefited from the high levels of productivity, consistency, and quality delivered by these systems, however as manufacturing trends continue to shift towards that of high mix and low volume, these systems will eventually lack the capability to remain an integral part of what is fast becoming an increasingly connected manufacturing environment.
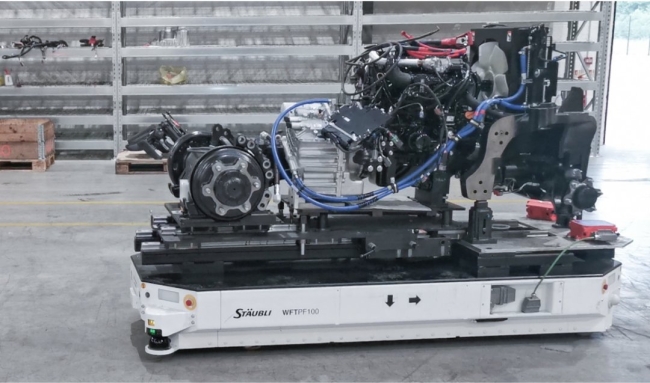
A wide range of technologies are available to companies seeking to embrace flexible manufacturing methods / Picture: Stäubli
Whilst there is always a focus on the new and upcoming developments, which will shape the next incarnation of the factory of the future, it’s important that we don’t lose sight of the technologies which have already emerged, and which make the factory of today possible. These technologies not only address the current shift in manufacturing trends, but they will also be the stepping-stones to the factory of tomorrow for many businesses.
Simon Jenkins explains: “Manufacturers today need to be more agile in the way that they respond to the demands from both their customers and consumers if they are to remain competitive in today’s dynamic marketplace. This can only be achieved if they take advantage of the wide range of manufacturing technologies that are compatible with the principles of Industry 4.0 and the IoT. In some cases, this may mean a comprehensive evaluation of their existing processes and technologies to define a strategy which will embrace all aspects of flexible automated manufacturing.”
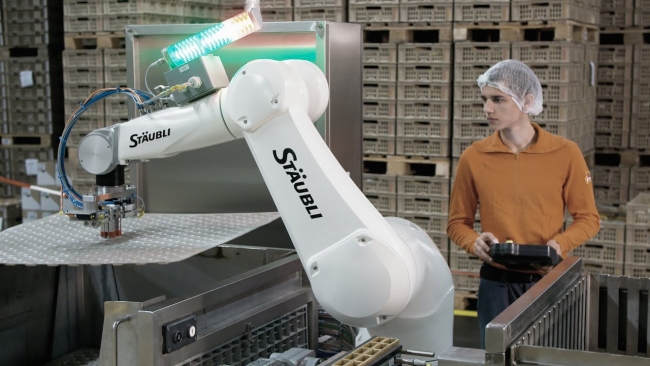
It is important that manufacturers don’t lose sight of the technologies which have already emerged, and which make the factory of today possible / Picture: Stäubli
The established “norms” of manufacturing are in some instances being challenged, as the rapid growth in EV’s and Electromobility have been the catalyst for new and alternative manufacturing methods which support high levels of flexibility and high-mix production. Simon Jenkins continues: “For example, we are beginning to see a significant change in the way in which some electric vehicles will be produced. Flexible and modular methods are set to replace the traditional in-line assembly track, with a series of modular workstations, each of which will carry out specific tasks and be served by AGV’s. This concept of truly flexible production methods is also being seen as an attractive manufacturing strategy for other sectors, where they too can leverage a wide range of technologies, such as the SCARA robots, 6 axis industrial robots, collaborative robots, mobile robot systems and Automated Guided Vehicles (AGV’s) available from Stäubli to help embrace the opportunities presented by Industry 4.0.”
By combining and connecting robots and automation with other technologies, such as a Manufacturing Execution System (MES) that will monitor, track, document, and control manufacturing processes, or an Enterprise Resource Planning (ERP) system to manage scheduling, a significant part of the factory of today can be defined.