3 minute read
Bosch Rexroth makes significant investment in new service centre
Automation expert Bosch Rexroth has recently made a significant investment in its UK service and repair centre, resulting in a facility with higher capacity, faster throughput and state of the art technology. The new workshop, which specialises in the repair of hydraulic products, is based at the company’s UK headquarters in Cambridgeshire.
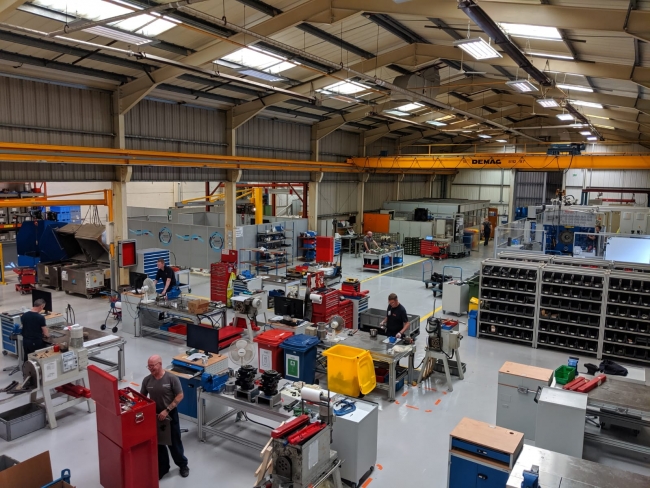
Bosch Rexroth has recently made a significant investment in its UK service and repair centre / Picture: Bosch Rexroth
Richard Bates, Service Operations Manager at Bosch Rexroth, said: “We’ve had a repair workshop in St.Neots since the company moved here in 1971. As big believers in continuous improvement, we’ve updated and tweaked our offering along the way to keep it up to date with the latest technologies and best practices and to mirror the assembly and test processes used in the manufacturing plants. However, with an increase in demand for Rexroth products, as well as many businesses opting to extend the lifecycle of their products rather than make big capital investments, we made a decision to completely overhaul our systems to meet market demand. The project has resulted in substantial investment in the facility.”
Including planning phases, the project has taken two years. From the outset, the Bosch Rexroth team has taken a consultative approach, working with its in-house experts and analysing extensive customer data to identify process improvements, quantify market demand and streamline the layout, the facility and the processes used. The team then went on to look at how the material flow could be improved and what high-value investment was required to optimise throughput. The culmination of this planning process is the opening of a new facility which will double both the size and the repair capacity of the previous workshop.
Richard added: “The jewel in the crown of the facility is a new hydraulic test station. This new equipment has made up a significant part of the overall investment, with a price tag in seven figures. For customers, the investment gives the peace of mind that equipment has been fully tested on a state-of-the-art bespoke test rig. In short, it guarantees that it has been repaired and rebuilt to an as-new condition. This conforms to our ‘Back to New’ programme, which guarantees repairs to original factory standards with a full ‘as new’ warranty. St Neots is certified by each of our manufacturing plants as a Centre of Competence for repair and test. This investment reinforces that.”
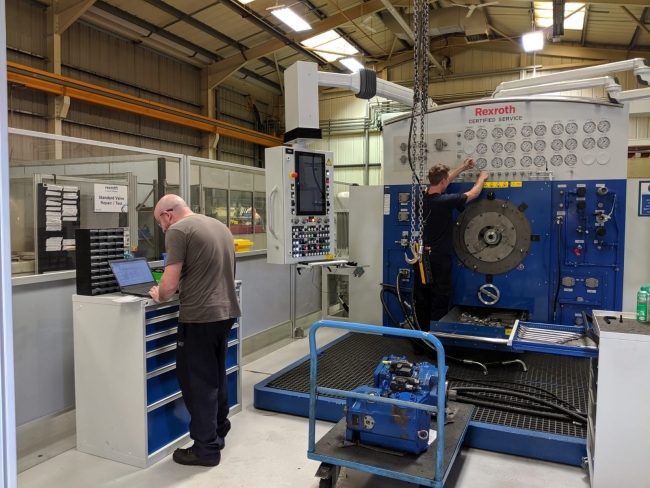
The new facility provides Bosch Rexroth with higher capacity, faster throughput and state of the art technology / Picture: Bosch Rexroth
Designed and manufactured by Bosch Rexroth to the same specification as the rigs in the manufacturing plants, the test rig offers the quality, repeatability and Industry 4.0 connectivity that customers have come to expect from the company – particularly in light of its commitment to preparing customers for the Factory of the Future. The unit links to the company’s global manufacturing plants, allowing engineers to input model and serial numbers and get the data required to test the equipment against its precise original specification.
Screens on the shop-floor visualise test data and how work is prioritised, helping to manage KPIs such as target repair times and customer SLAs. In addition, the workshop layout has been completely updated, new technologies have been introduced, additional wash-stations and lifting rigs for equipment have been implemented and new, ergonomic workstations fitted. All of this has been done using the Bosch Production System – a philosophy which focuses on designing facilities to create the optimum workflow and deliver process improvements to help meet changing customer demand.
“This investment is all about making ourselves and our customers fit for the future. Our existing reputation for quality and speed of repair regularly sees us receiving Rexroth product for repair from all over the world, mostly from ships in harbours in exotic locations with a non-negotiable departure date. We’ve got an ambitious growth strategy which is focused on building partnerships and key accounts – it is absolutely vital that we’re able to meet the growing demand both in terms of the manufacture of Bosch Rexroth products and ongoing technical support.”