Insight: Digital manufacturing 101 – future-proofing your operations in an era of constant change
Digital solutions are transforming how manufacturers operate. By leveraging real-time insights, optimised workflows and adaptive systems, companies can gain unparalleled visibility, efficiency and agility. The technology may seem daunting, but it’s more accessible and important than ever. Dr Fadi Assad, Lecturer at Cranfield University, explains how digital manufacturing can help you secure a competitive edge.
Manufacturing has continuously evolved over the centuries, from early steam-powered machines to the precision of modern robotics. Yet, the pace and scope of today’s paradigm shift set it apart from past revolutions. Rather than simply automating processes or increasing production speeds, digital manufacturing redefines how goods are designed, produced and delivered.
From mechanisation to digitalisation
It’s crucial to understand the historical trajectory of manufacturing because current advances build directly on past innovations.
The First Industrial Revolution (1760 – 1840) introduced steam engines, mechanised textile looms and early factory systems, marking the transition from small-scale, manual crafts to machine-based manufacturing.
The Second Industrial Revolution (1870 – 1914) brought electrification, the moving assembly line and mass production.
The Third Industrial Revolution (1950s – 2000s) saw the integration of electronics and programmable logic controllers (PLCs), with lean manufacturing methodologies reshaping factory floors.
The Fourth Industrial Revolution (2010s – Present) – digital manufacturing – is fusing the physical and digital world to create an interconnected ecosystem where data flows seamlessly from the shop floor to the boardroom.
This connectivity delivers the operational visibility needed to drive meaningful change. With enhanced visibility, manufacturers can monitor every aspect of production in real-time, spot potential issues before they escalate and pivot quickly – whether it’s launching a new product or responding to supply chain disruptions.
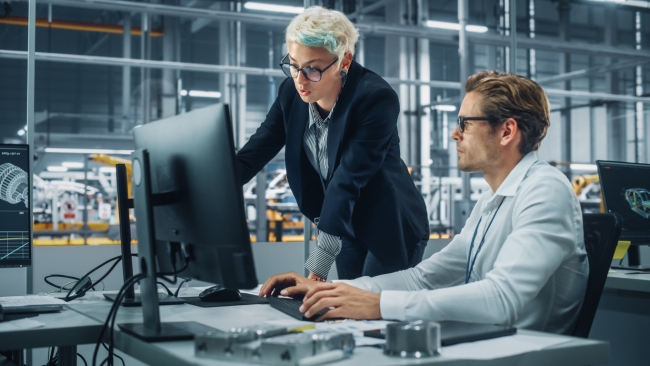
Digital manufacturing transforms operations by providing real-time insights, optimised workflows, and adaptive systems, leading to increased visibility, efficiency, and agility / Picture: Getty/iStock
Key technologies in digital manufacturing
Digital manufacturing is best understood as a toolbox of powerful, interconnected technologies that link every stage of production, from design and fabrication to shipping and maintenance.
• Communication technologies like Wi-Fi, Bluetooth, radio waves, fibre optic cables and mobile networks have revolutionised how data is gathered and shared. A prominent example is 5G, the latest generation of mobile networking technology known for its faster speeds, enhanced reliability and lower latency. Unlike earlier generations like 3G and 4G, 5G is purpose-built to support seamless communication between hundreds of machines, systems and devices.
• This network of interconnected devices creates what is known as the Internet of Things (IoT) Almost anything can be retrofitted to become an IoT device, even 100-year-old milling machines. This data can then be collected and analysed in real-time to monitor performance and alert engineers to potential issues.
• The power of data analytics lies in translating vast amounts of complex raw information into useful insights, enabling manufacturers to track key variables, fine-tune processes, improve output and minimise waste.
• Cloud computing has transformed how data is stored, processed and accessed. Through centralised data collection, real-time processing and instant collaboration across locations, cloud-based platforms allow companies to act on data without needing extensive on-premise infrastructure.
• Modern factories increasingly rely on smart automation systems that are flexible and multifunctional, allowing them to undertake complex tasks, alongside repetitive or hazardous jobs. Unlike traditional industrial robots, a collaborative robot (cobot) is designed to work alongside humans in a shared workspace. Cobots are often lightweight, adaptable and can learn from human interaction to perform a wide range of tasks.
• Virtual and augmented reality (VR/AR) technologies are reshaping how manufacturers design, train and troubleshoot. VR can simulate entire production environments, allowing engineers to test new layouts without disrupting operations. AR overlays digital information onto the real world, assisting workers with step-by-step assembly instructions and 24/7 support.
• Although a relatively new arrival, Artificial Intelligence (AI) has already begun to underpin many digital manufacturing technologies. Not to be confused with Machine Learning, when machines use past data to learn how to perform tasks, AI has a much broader scope of applications. AI-driven systems analyse vast datasets faster and more accurately than human operators, and can handle all types of data: structured, semi-structured and unstructured. This makes them ideal for predictive maintenance, quality assurance, business process automation, demand forecasting, supply chain optimisation and risk assessment.
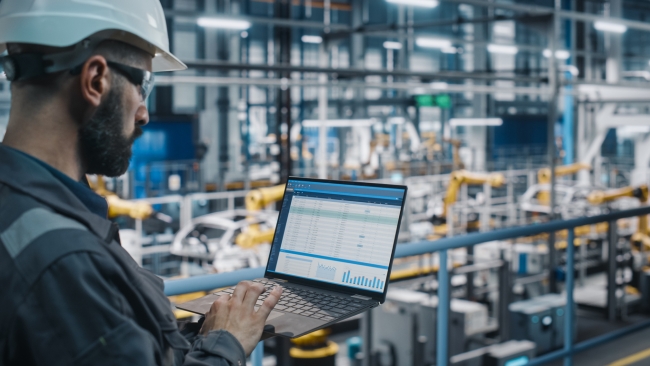
Key technologies like IoT, 5G, AI, cloud computing, and cobots are essential components, each contributing to specific aspects of production and data management / Picture: Getty/iStock
Key advantages of digital manufacturing
Imagine having a 360-degree view of your entire production process. With digital manufacturing, every product, machine, process and operator is connected by a digital thread. This seamless data flow ties everything together, delivering real-time insights that can reveal inefficiencies, quality issues or safety concerns before they escalate. Full operational visibility means companies aren’t flying blind, they’re making strategic decisions based on precise, current information.
Connecting disparate systems and data sources also allows manufacturers to create a digital passport containing key information about a product throughout its lifecycle. Details might include when and where it was manufactured and by who, raw material suppliers, shipping records, compliance information, its carbon footprint and whether it can be recycled or reused.
Other key benefits of digital manufacturing include:
• Greater efficiency and flexibility at both the machine and enterprise level
• Streamlined product development, reducing time and complexity
• Lower inventory and utility costs through better resource allocation
• Improved equipment uptime and longevity via predictive maintenance
• Higher quality output with less rework, reducing defects, production delays and costs
• More accurate demand forecasting and supply planning, minimising disruptions
• Stronger collaboration between employees, suppliers, distributors and customers
• New revenue opportunities like ‘as-a-Service’ business models
A recurring theme across these benefits is sustainability. An optimised factory that consumes less energy and materials is not only more cost-efficient but also has a smaller carbon footprint. Additionally, it has the insights to keep improving.
Companies that have integrated digital manufacturing technologies and approaches have reported double – even triple-digit – efficiency gains. At a time when manufacturers need to produce more while using fewer resources and generating less emissions, digital manufacturing offers a distinct advantage.
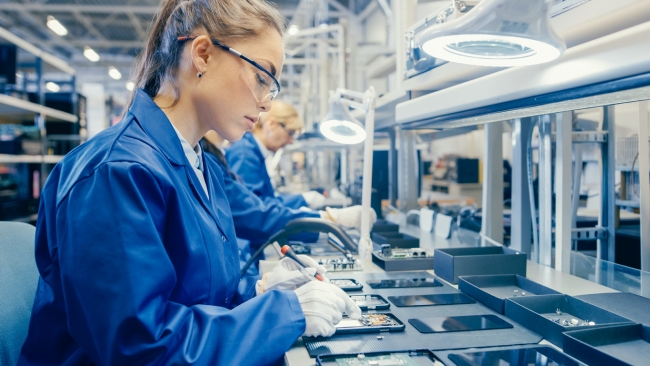
Without the ability to spot opportunities or problems and act on them, businesses may find themselves outpaced by those better equipped to adapt to rapid change / Picture: Getty/iStock
Who is digital manufacturing for?
Digital manufacturing isn’t reserved for large multinationals; it’s for every manufacturer. Whether you’re a small, family-run operation or a global enterprise, the principles of visibility, efficiency and agility are universally applicable.
For smaller manufacturers, digital solutions offer a way to compete with larger players by making operations more efficient and responsive. For large organisations, the challenge is often integration, bringing disparate, legacy systems and processes into a single, cohesive workflow.
Success lies in understanding how and where digital manufacturing can have the greatest impact. By targeting the right areas, integrating appropriate technologies and adopting a holistic, strategic approach, companies can unlock new levels of efficiency, innovation and resilience. That’s why industry-aligned expertise is essential – and where Cranfield University plays a pivotal role.
As a specialist postgraduate university with award-winning expertise, large-scale facilities and unrivalled industry partnerships, Cranfield is uniquely positioned to support manufacturers with digital transformation. Our programmes are designed in close collaboration with industry, bridging the gap between theory and practice, ensuring that graduates are well-prepared to address current needs and challenges.
Whether you’re a manager looking to upskill your team or bring on board a new graduate, or an individual aiming to advance your career, transition into manufacturing or reach senior leadership, Cranfield provides a clear pathway to success.
Equipping professionals for modern manufacturing challenges
Cranfield is the UK’s largest provider of Master’s-level (MSc) graduates in engineering. Through our extensive research and consultancy with government and industry partners, students gain hands-on experience solving real-world challenges.
Our Engineering and Management of Manufacturing Systems MSc is designed to equip professionals with the knowledge to develop and manage competitive manufacturing and service operations. By focusing on industrially relevant projects, teamwork and transferable skills, this course ensures graduates can drive immediate impact – whether optimising supply chains, enhancing manufacturing performance or streamlining process flows.
Alessia Paoletti, Junior Digital Manufacturing Manager at Danone, explains how Cranfield’s’ MSc equipped her to contribute to the company’s digitalisation journey: “The knowledge I gained during the group project has proven invaluable. Our task was to develop a digital tool using Python based on data and requirements from a real company with a real need. This experience structured my approach to problem-solving, a skill I now use daily when creating dashboards from raw data.”
Our flexible course offerings include full-time, part-time and apprenticeship options, enabling eligible organisations to use their Apprenticeship Levy to cover tuition fees. With a strong emphasis on immersive, practical learning, collaborative projects and real-world case studies, our MSc programmes are helping tackle the challenges of modern manufacturing.
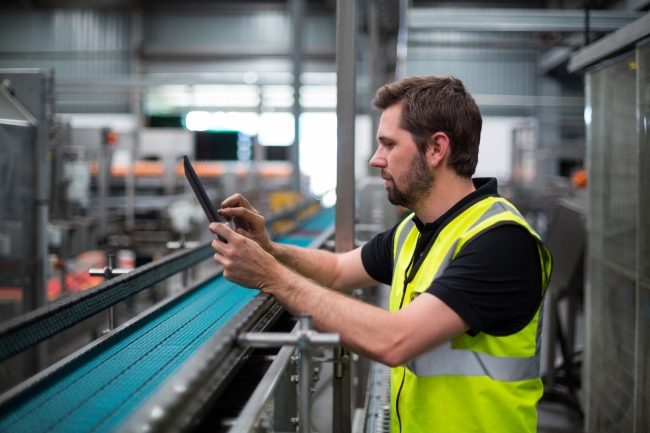
Digital manufacturing is applicable to all manufacturers, regardless of size, and partnerships with institutions like Cranfield University can provide the necessary expertise and support for successful digital transformation / Picture: Getty/iStock
Unlocking innovation through KTPs
Beyond traditional education, Knowledge Transfer Partnerships (KTPs) are another powerful avenue towards digital manufacturing. A KTP is a three-way collaborative project that connects your business with Cranfield’s world-class research and facilities and a skilled research graduate. KTPs focus on delivering a strategic innovation project to solve a specific challenge while driving innovation and competitive advantage.
Take, for example, our work with Levidian Nanosystems, a UK-based climate technology company, who partnered with Cranfield through a KTP project to enhance its flagship decarbonisation technology – the LOOP system. This innovative device converts methane gas into hydrogen gas and solid graphene, offering a scalable way for industries to reduce carbon emissions while unlocking new market opportunities.
However, the company faced a challenge. LOOP lacked real-time monitoring, making it difficult to predict failures or refine performance. Without these insights, maintenance was based on fixed schedules rather than system health. In addition, as demand for LOOP technology grows, ensuring consistent performance across different environmental conditions without real-time analytics and benchmarking proved complex.
Recognising the critical role of digital solutions in optimising their technology, Levidian turned to Cranfield and research engineer, Jayashri Goddanti. Through a KTP, the project successfully integrated digital twin technology into the LOOP system, unlocking unprecedented operational insights and predictive capabilities. This has provided tangible business value for Levidian, including:
• Real-Time Operational Visibility – Continuous performance monitoring enables operators to make quick and informed decisions, with increased transparency in system performance allowing for better communication with clients.
• High-Quality, Reliable Data – The digital model provides detailed insights into LOOP’s operation, ensuring that business decisions are backed by reliable evidence, improving efficiency and reducing uncertainty.
• Process Optimisation – Automatic data reporting simplifies compliance with industry and environmental regulations, with this information used to showcase the impact of LOOP to stakeholders and clients.
• Predictive Maintenance – The Digital Twin shifted LOOP from reactive to data-driven maintenance, reducing expected downtime and repair costs.
• Enhanced Scalability – Through advanced modelling and AI, the digital twin can forecast maintenance needs, optimise energy use and improve system longevity. Continuous learning from real-world data ensures the system becomes smarter and more accurate over time.
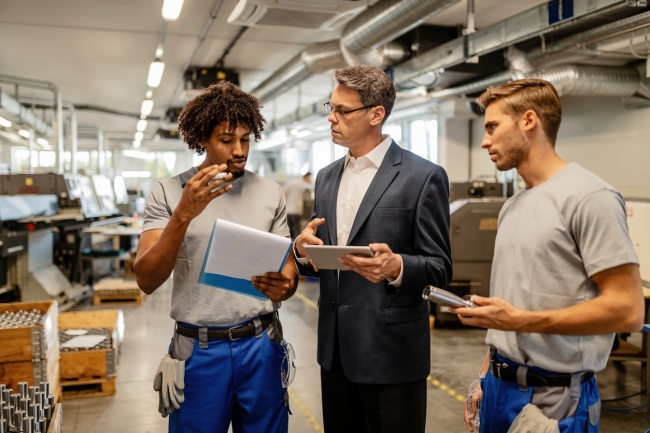
Companies that have integrated digital manufacturing technologies and approaches have reported double – even triple-digit – efficiency gains / Picture: Getty/iStock
Future-proofing your business
Technology is the engine that drives opportunity. Digital manufacturing goes beyond simply adding new tools; it’s about equipping your business to harness real-time insights, automate complex processes and respond to market shifts at pace. By integrating digital solutions, you unlock enhanced visibility across your operations, streamline workflows to boost productivity and build the agility required to meet evolving demands.
Digital manufacturing also isn’t a fleeting trend. The ability to collect, analyse and act on data will remain critical, continuously improving as technology evolves but remaining forever present. The future of industry lies in harnessing these digital tools, with the benefits extending far beyond the factory floor.
On the other hand, ignoring these trends can have lasting consequences. Companies that delay their digital adoption risk higher operational costs, sluggish responsiveness and, ultimately, lost market share.
Without the ability to spot opportunities or problems and act on them, businesses may find themselves outpaced by those better equipped to adapt to rapid change. The cost of inaction grows over time as outdated processes lead to greater inefficiencies and further missed opportunities.
Staying ahead means building future-ready teams today. By collaborating with Cranfield’s experts and leveraging our facilities, you can secure the knowledge and practical expertise necessary to integrate digital manufacturing solutions effectively into your operations.
Our tailored courses and Knowledge Transfer Partnerships provide hands-on experience and actionable insights, ensuring that you’re prepared for current challenges with a foundation to build tomorrow’s innovations.
The time to act is now
Connect with us to learn how digital manufacturing can redefine the possibilities for your business and secure your competitive edge for years to come. Embrace the digital future today and lead the change – because the ability to adapt, innovate and excel will define tomorrow’s industry leaders.
Subscribe to Cranfield Insights here, for more thought leadership, insights and applications for industry professionals.