2 minute read
MTC programme produces high-stress ‘Super-Alloy’
Cutting-edge technology developed by a team at the Manufacturing Technology Centre in Coventry has resulted in a super-strength alloy capable of withstanding the massive stresses of space travel.
Scientists and engineers at the MTC have been working with one of the country’s leading surface engineering and metal coating companies to develop the ultra-resilient alloy using the latest shot-peening techniques.
Towcester-based Sandwell UK carries out surface coating and shot-peening processes for a number of high-stress applications including aerospace and Formula One. The processes produce stress layers which strengthen the mechanical properties of metal parts.
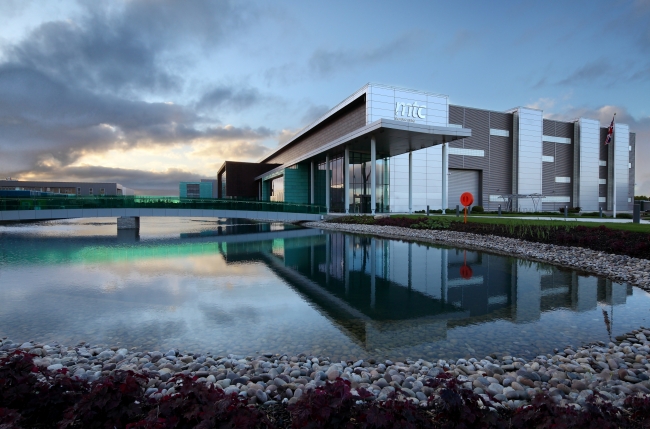
Leading surface engineering specialist Sandwell UK worked with MTC to develop an ultra-resilient hardening process / Picture: The MTC
Now, in the latest programme being carried out by the MTC and Sandwell UK, part-funded by the Government’s REACH fund for SMEs delivered by the MTC, engineers have developed a process which results in a highly resilient nano-structured surface on nickel alloy. After the process, the alloy has hardness properties suitable for the most high-fatigue environments. This makes it suitable for spacecraft, satellites, aerospace applications and Formula One, or for use in renewable energy systems such as highly-loaded wind generation components. The research is continuing, with funding from Innovate UK.
While these results have previously been achievable in a laboratory, MTC and Sandwell UK engineers have developed the process for commercial volume production.
The process will also help Sandwell’s other clients who include companies involved in the oil, gas and marine industries, including offshore drilling and exploration. A further result of the process is that the treated metal has anti-bacterial properties which could make it suitable for medical applications and implant parts.
Ken Young, the MTC’s technology director, said the process developed was a significant step forward in understanding nanostructure transformations in metals and alloys.
“It is delight to work with a world leading SME where our expertise can help them take their process knowledge to not only help existing clients, but also open up new market opportunities. Companies such as Sandwell show the future potential for British manufacturing to lead the world.”
Colin McGrory, technical director of Sandwell UK, added, “The surface structure resulting from the new process can significantly improve the fatigue performance of the material, and also reduce the effects of chemicals and reduce the rate of bacterial growth on the surface. We will continue to assess the benefits in material performance. We are indebted to the work of Yijun Liu and his team at the MTC and also to Birmingham University who validated the results using their transmission electron microscope.”
The MTC aims to provide a competitive environment to bridge the gap between university-based research and the development of innovative manufacturing solutions, in line with the Government’s manufacturing strategy. The MTC is part the High Value Manufacturing Catapult, supported by Innovate UK.