3 minute read
Nottingham engineers produce 3D printed face shields for NHS
Engineers at the University of Nottingham have designed a PPE face shield with CE approval that is set to be 3D printed at scale for use by healthcare workers.
Using the latest in additive manufacturing (3D printing) technology and materials at the University’s Centre for Additive Manufacturing, and working with external collaborators, the team will deliver 5,000 face shields to Nottingham’s NHS and community healthcare workers.
Building on an open-source design of headband originally from HP, the team in the Faculty of Engineering made modifications to ensure the face shield could pass a regulatory test by BSI, the UK’s national standards body, to meet its essential health and safety requirements which ensures the highest level of protection is provided.
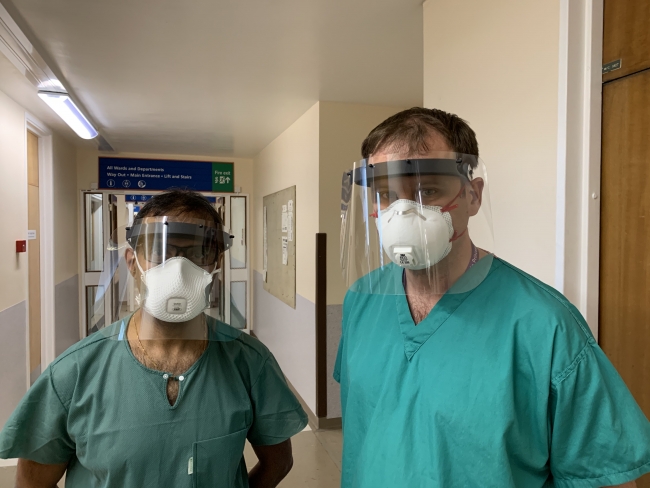
Engineers at the University of Nottingham have designed a PPE face shield that they are 3D printing at scale for healthcare workers / Picture: University of Nottingham
The face shields successfully passed the BSI tests and are CE approved for use as part of PPE for healthcare workers’ protection against Covid-19 in both hospital and community environments. They are provided in packs to the NHS, with five replacement visors per face shield as well as instructions for use.
The team have made the design and its accompanying documents ‘open-source’ to enable other manufacturers to produce the face shields – however, manufacturers will need to submit their product for testing to the BSI to obtain their own CE certification.
Professor Richard Hague, director of the Centre for Additive Manufacturing, said: “Our primary goal was to ensure that we delivered a PPE solution that was safe and certified so that healthcare workers can have confidence in the equipment they’re using. Using the flexibility of additive manufacturing (3D printing) and laser cutting technology, we’ve been able to arrive at a design, get it tested and approved, and then manufactured and delivered in a very quick timeframe.
“We have also had incredible support from our collaborators in getting these face shields to the NHS – the teamwork and willingness of people to help has been truly heart-warming and we are all extremely proud to be able to contribute to the nation’s fight against coronavirus.”
Professor Donal McNally, head of the Bioengineering Research Group in the Faculty of Engineering, added: “Having a PPE solution that meets National and EU safety standards is critical for deployment within the NHS. It has been a truly outstanding achievement to go from nothing to thousands of devices being used by local doctors and hospitals in less than a month. This would not have been possible without the extraordinary efforts of local manufacturing partners and BSI.”
Dr James Hopkinson, Local GP and joint clinical chair of NHS Nottingham and Nottinghamshire CCG, concluded: “We are extremely grateful to the University of Nottingham for developing and supplying the visors which will make a real difference to thousands of healthcare staff working on the frontline of the coronavirus outbreak.
“Packs of the face shields have already been delivered to local GP practices, and we have plans in place to share them with a range of other keyworkers such as people who care for others at home. I think this is a really positive example of talented professionals working across normal boundaries in order to support our local communities in what is an unprecedented and very challenging time.”
Design modifications were made by the team to conform to the BSI’s PPE regulations in order to obtain CE marking; this involved making the wrap-around visor element wider, as well as other alterations to improve comfort for users. The HP design was chosen by the Nottingham engineering team as it incorporates a cover at the top of the face shield which prevents fluid from entering the eyes from above – deemed critical by healthcare professionals.
The face shield comprises a 3D printed headband, a laser cut PET visor (with anti-fog coating) and is kept in place with a laser-cut adjustable strap. As well as using their own EOS Laser Sintering equipment, the University of Nottingham’s engineering team have been heavily supported by Matsuura UK to produce the 3D printed element, using their HP MultiJet Fusion process. The visor element has been made with the help of local firm, Prime Group, and Nottingham Trent University are now ramping up for production of the laser-cut strap.