5 minute read
Produmax recognised for engineering transformation
Yorkshire aerospace engineering specialist Produmax has won a new national award which recognises how its staff and management have worked together and developed their skills to grow the business.
The Sharing in Growth Ikigai trophy was handed over in front of Produmax’s 70-strong workforce as well as guests from Boeing, Lockheed Martin, Safran Nacelles, BAE Systems and Senior Aerospace, the EEF, Bradford City Council, and Keighley College.
The Ikigai trophy was presented to Produmax managing director Jeremy Ridyard by Dr Bryan Jackson CBE, chairman of Sharing in Growth (SiG), the intensive government-backed programme designed by industry to raise the competitiveness of the UK aerospace supply chain.
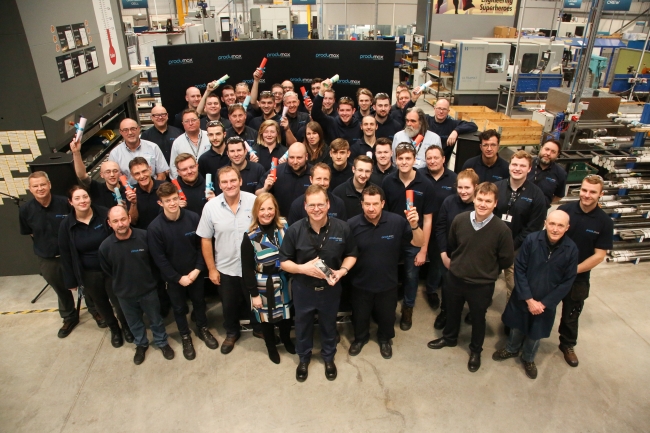
The Produmax team celebrate their skills awards with Ikigai trophy / Picture: SiG
Produmax, which specialises in the manufacture of flight control components, was selected for the Sharing in Growth transformation programme in 2014. Since then, with the support of Sharing in Growth, Produmax has created a vision to be engineering superheroes and developed its business significantly. Its total business transformation included opening new headquarters, changing its culture, creating a farsighted strategy and delivering operational performance in line with world-class practices. As a result, the family-run firm has secured almost £20 million in contracts, won three new customers and grown its workforce by 40%.
The company won Sharing in Growth’s new top award for pursuing a total business transformation. This included consolidating two older factories, including a Victorian tannery, into one new larger purpose-built plant which was fully-configured by the employees. To support an ambition to hit £10 million turnover by 2020, Produmax has now invested in a second factory on the same site to open later in 2018, creating further capacity and more jobs.
The company is a supplier to world-leading aerospace companies such as Boeing, Bombardier, Moog and Meggitt, exporting 80% of production overseas to countries including USA, Canada, Japan, Morocco, the Philippines, and Italy.
Produmax’s employees led a shopfloor tour that demonstrated the many advances implemented with the support of Sharing in Growth. These included business improvement techniques, lean manufacturing cells, single flow processes, multi-manning, lights out automation, a gated new product introduction system, new communications and staff engagement processes, manpower planning and problem solving.
Produmax managing director Jeremy Ridyard said: “With Sharing in Growth’s support, we developed a new strategy that required an efficiency model to support our component and assemblies business and a service model to deliver spares and new product introduction. As part of our business transformation, Sharing in Growth helped us change our culture, shopfloor layout, and processes to support continuous improvement. As a result our operational KPIs have improved to world-class levels. For example, we reduced lead-time from 32 days to 23 hours and machine set up time has been reduced by 75%.
“We are investing in people and technology. We are looking at hard meal cutting, complex assembly and additive layer manufacture and, through a Knowledge Transfer Partnership with Leeds University, we are solving technological challenges, like tool life management and operating temperatures so that we can increase capacity through automation, taking advantage of lights out weekend running.”
Finance director Mandy Ridyard explained that Produmax’s growth and success relied on the capability, enthusiasm and skills of its workforce and the support of Sharing in Growth: “Our vision is to be engineering superheroes and our strategy is to grow our factory, grow our people and grow our business. We managed to consolidate two factories into one new one, introduce new levels of automation and improve our culture and brand exposure all at the same time. We know employee engagement is key to cracking the productivity puzzle and we have increased our employee engagement by 25% to world-class levels and increased our productivity by 32%. We are very proud of our achievements and will keep applying continuous improvement for continued growth.”
Produmax implemented Sharing in Growth’s best practice to change its culture and engage employees. This included using a variety of communications techniques to appeal to different people which reinforced key messages. For example, to underpin their corporate value of Ubuntu (one team) company performance is shared with all employees, everyone uses the same building entrance, achievement of targets is celebrated by the whole team, and all are encouraged to build their skills through personal development plans. Some 40% of Produmax employees have studied or are studying for qualifications.
Presenting the Ikigai award, SiG chairman Bryan Jackson explained that Ikigai was a Japanese word that encapsulated passion and purpose. “Produmax are the embodiment of Ikigai in that they are good at producing something the world needs, they have grown the business and created a team culture where people are passionate about raising their skills to contribute to such a successful business.”
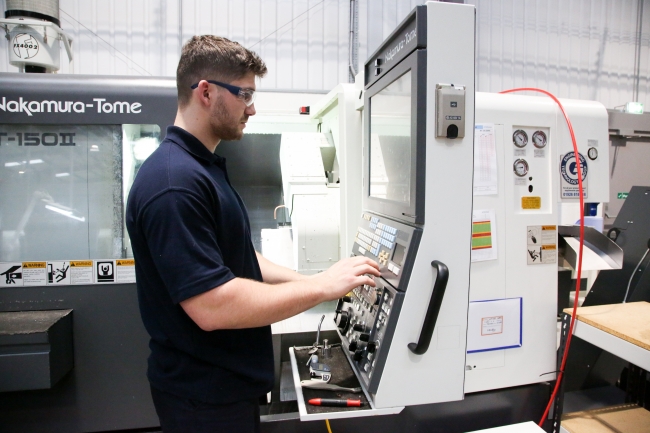
Luke Copsey, who started as an apprentice at Produmax, has achieved a number of qualifications since joining the firm in 2012 / Picture: SiG
The event also celebrated Produmax’s investment in staff development with the award of national qualifications to 14 Produmax staff as part of the Sharing in Growth programme. They were presented with a range of qualifications including Level 3 NVQ extended diplomas in mechanical manufacturing engineering, Level 2 and 3 certificates in business improvement techniques, HNDs and HNCs in mechanical engineering.
Luke Copsey started working as an apprentice at Produmax in 2012, having enjoyed a Saturday job at the company. He achieved an NVQ Level 3 in mechanical manufacturing engineering, a NVQ Level 2 in Business Improvement Techniques and an HNC in mechanical engineering. Luke said: “I love the culture at Produmax and the learning opportunities offered. And, having worked at the two old factories, I have enjoyed being part of Produmax’s development into a world-class company.”
Denzil Lawrence from Boeing, who is responsible for UK supplier development told the Produmax team: “This is a very exciting time to be in aerospace as 41,000 aircraft are going to be built in the next 20 years. Companies like Boeing rely on the skills of companies in their supply chain to be competitive. Produmax has been constantly learning and adapting to meet the changing needs of the market, training its people to rise to the challenge. You represent the best of British so please keep going, and you will stay as world-beaters.”
Nigel Strutt, UK Director, Supply Chain Policy, Governance and Operations Lockheed Martin UK, added: “Lockheed Martin recognises the valuable role supply chain companies play in maintaining our competitive edge in the marketplace. Produmax is an exemplar of a company which engages key stakeholders be they customers and or staff, and employs innovation and continuous improvement for sustainable growth. We continually seek to optimise supply partnerships based on mutual success so would strongly encourage other suppliers to aspire to follow the Produmax example.”
The SiG programme is supporting 63 companies across the UK and is endorsed by Airbus, BAE Systems, Boeing, Bombardier, GE, GKN, Leonardo, Lockheed Martin, MBDA, Rolls-Royce, Safran and Thales. It is supported by the Regional Growth Fund and more than £150 million in private investment.
With SiG support, the first 43 companies on the programme have secured more than £2 billion in contracts to date – almost 20% of which is for direct export. Consequently, having secured more than 3,000 jobs, SiG is well on target to hit its ultimate objective of safeguarding 10,000 UK jobs by 2022.