4 minute read
Timber manufacturer invests in cutting-edge technology
A masterpiece of Italian design technology costing as much as a Ferrari 458 has revved into action at one of the UK’s leading timber manufacturing companies.
Ruthin-based Clifford Jones Timber have been backed by the Welsh Government to spend £150,000 on a top of the range Masterwood 375 computer controlled five-axis machine.
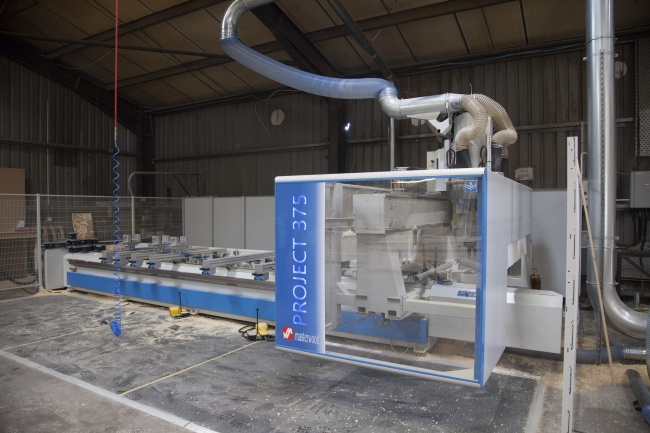
The Masterwood 375 at Clifford Jones Timber enables the firm to revolutionise their laminate production / Picture: Clifford Jones Timber
It will revolutionise their ability to produce high quality laminated timber to exact specifications, according to Chairman Richard Jones, whose grandfather founded the family firm in 1948.
He said: “It’s a major boost to us to have had the grant approved by the Welsh Government and we’re delighted to have taken delivery of what is a very sophisticated piece of machinery.
“It operates to very exact tolerances and measurements and will really introduce engineering standards to our laminated timber production.
“It will mean our customers can give us exact measurements and we can then programme the machine to exactly reproduce them – it means timber will have the same sort of tolerances that metals have.
“Because it’s computer-controlled it’s all about precision and we believe it’s a bit of a game-changer for us.”
Masterwood are an Italian company based in Rimini, on the Adriatic coast, with 50 years of experience of producing woodworking machines, mainly for the furniture industry.
The 375 machine is almost 20 feet long by six feet high, weighs seven tons and the fact that its machine tools can operate on five different axes gives it great flexibility of use.
Machine operator Michael Beaumont, from Llanbedr DC, near Ruthin, said: “It’s an amazing machine, an absolute joy to work with and a superb piece of kit.
“It’s a one-stop shop for all the tools you need and it can do everything you want and more – it’s more than meeting expectations and the future looks bright.
“We supply laminated wood lamp-posts for Center Parcs and it used to take us an hour and a half to do one of them – this can do two in eight minutes.”
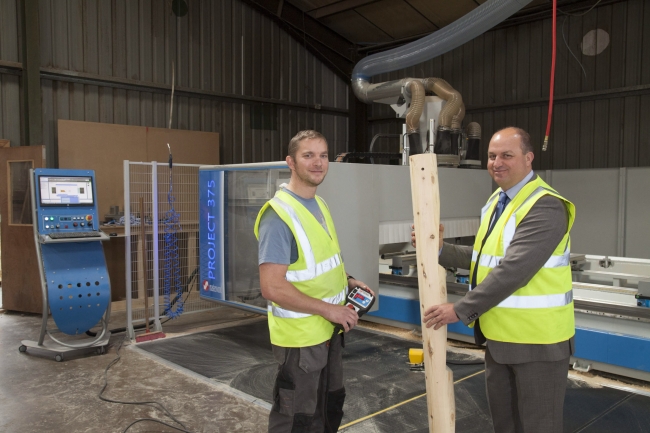
CNC machine operator Michael Beaumont, left, with chairman Richard Jones / Picture: Clifford Jones Timber
Clifford Jones Timber saw the potential for using it in their laminated timber production both for existing customers in the play, leisure and construction markets and for reaching new customers.
Laminated timber has the advantages of being much lighter than steel or concrete and much stronger and more durable than wood.
Clifford Jones Timber pioneered the manufacture of laminated timber in Wales when they invested more than £1 million in a laminating plant at their eco-friendly nine-acre headquarters site on Ruthin’s Brickfield Lane industrial estate.
The project was also backed by a Welsh Government grant of £157,000 with the process using hi-tech glue developed for the aero industry to bond lengths of timber together under high pressure.
The glue is the same as is used by British Aerospace for the wings it builds at Broughton for the Airbus and it produces a product that is four times stronger than conventional wood.
The laminated timber is made by drying layers of timber down below 18 per cent moisture in kilns before gluing them together in a quarter of a million pound laminator which takes just six minutes to bond it.
Their three kilns are powered by a 987 kilowatt biomass boiler which is fed with wood chippings taken from the 100,000 tons of timber which is processed at the Ruthin site every year.
It can then be manufactured into exact sizes using the new Masterwood 375 and Richard Jones added: “It is a continuation of our policy of diversification and sustainability.
“We look to make the most out of the 100,000 tons of timber that comes through our gates every year and we’re proud of the fact that everything that nothing leaves this site without an invoice.
“We are always looking to add value so that even the residues we produce in making over two million fence posts a year generate an income.
“Everything is used. That’s part of our culture that includes using sustainable timber from Welsh and Scottish FSC-certified forests and we aim to make the most of it because it makes good business sense and it makes sense for the planet as well.”
As well as laminated timber and fence posts Clifford Jones Timber also produce , fuel logs, gates and garden furniture with the residue going to make over 25,000 tons of pellets and briquettes for everything from biomass to barbecues.
They kiln-dry timber to improve preservative penetration on their treated timber, using on-site kilns powered by their own wood fuel, and sell kiln-dried logs – the offcuts from the fence posts.