4 minute read • published in partnership with Evocon
Why OEE is the best investment in manufacturing for 2019
For manufacturers, the beginning of a new year is the time to reflect on what you accomplished. What you need to improve. And what you want to achieve going forward. Quite possibly you already have your goals set for 2019. But do you have a clear understanding, of how efficiently your machines are operating today? Or do you have accurate information about the main problems your shop floor is facing and which machine downtime reasons need the most attention? Or how much additional resources are actually at your disposal. But hidden in the current processes and what investments you need to make? Evocon explores how you can have access to production information that will help your company achieve the goals set for 2019.
At Evocon we have been working with manufacturers since 2010. Helping them monitor their OEE and gain much-needed transparency to make informed decisions. And based on our experience the questions above are precisely the ones that most companies are looking for answers to.
So the best way to jump-start the new year is to make sure that you have a system in place that gives you access to the information that you need. And with the availability of a cloud-based OEE software, like Evocon, it has never been easier.
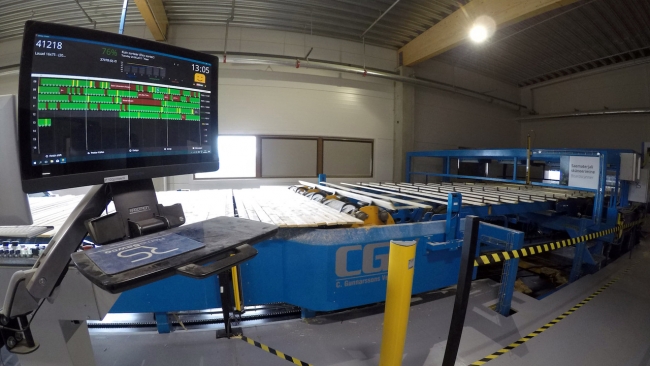
By monitoring machines with OEE software, a manufacturer can visualize the health of the production area / Picture: Evocon
Here are three reasons why investing in OEE software is the best decision you can make in 2019.
1 – Visualize the health of your factory
Let us consider the following example. You have 10 machines in your factory which are working in two shifts during business days. Totalling to approximately 5200 work shifts in a year. If each of these machines has 30 minutes of unplanned downtime in every work shift, that go unnoticed, then it equals 325 work shifts lost in one year. Which in turn means the company needs to compensate all the lost time and production output with extra work shifts either during the night or weekend.
A question you can ask yourself is this – how many extra shifts did you need in 2018? If you have factories in multiple countries then how many extra work shifts did your company, need globally? Following the example above, then how many of those can you avoid in 2019?
By monitoring your machines with an OEE software, you visualize the health of your production. And a real-time overview of every shift, hour-by-hour, gives you a precise overview of how you are using your planned production time. Also, how many unplanned and micro stoppages your production experiences. More importantly, it shows why these stoppages happen and where you can improve.
2 – Create an improvement plan that makes a difference
Let’s consider another example. Based on the data from the recent free trials that we conducted with our clients, there were approximately 24 unplanned (more than 3 minutes in length) and 87 micro stops (up to 3 minutes) on average per shift. If we extrapolate this data to the previous example of 10 machines and one month. Then it leaves us with 9 600 unplanned stops and 34 800 micro stops, monthly, for the whole factory.
Even though the numbers are enormous, it is essential to understand that being aware of your situation is the first step towards improving your processes.
The second step is to understand what are the reasons behind all those stops. And when you start to gather this information, then some downtime reasons you are already aware of – such as technical reasons, material problems, organisational mishap etc. But there are always reasons that go unnoticed. Reasons that most employees are unaware of which bring down the efficiency of your machines.
By investing in an OEE software, you give yourself the opportunity to get insight into all the production stops that happen in your factory. What is more, you can get most of this information already during the first month of monitoring your machines. Which in turn allows you to create a concrete improvement plan for the whole year.
So do your team a favour and eliminate the guesswork in 2019 and focus on what’s really important – taking care of your company.
3 – Validate investment decisions
We know that investing in production equipment is a costly undertaking. Whereas the expected break-even period can be up to 10 years or more. Unfortunately, a standard action when unable to meet demand is to buy new equipment. Sure, new machines are faster and help you increase output but is it necessary in the first place?
As the above example shows, then in most cases, there is a lot of unused resources available in the factory, and it is best to maximise the utilization of your current machines before buying new ones. By monitoring the OEE of your production machines, you will know precisely if and where to focus your investments.
But this is not the only reason how OEE monitoring helps. Once you have decided to invest in new machinery, you also need to make sure that they are running as efficiently as possible. Otherwise, you risk increasing the payback period of your machines.
Based on our experience, the average OEE of production lines and machines is around 42%. A world-class OEE is about 85%. But if your production equipment is at 42% OEE for years, without you knowing this, then, in essence, you are doubling the payback period of every machine you have. Instead of breaking even in 10 years, you are doing it in 20.
Are you planning capital expenditures to new equipment or technology in 2019? Before you undertake the costly road to investing, implementing and fine-tuning new machines make sure you actually know what is the potential of your production with current resources.