2 minute read
Nissan to supply 100,000 items of PPE from Sunderland plant
A team of Nissan volunteers are lending a hand to enable hundreds of thousands of protective face visors to reach frontline workers.
The team has created a parts processing line in the final assembly area at the company’s Sunderland plant to sort thousands of individual visor parts and pack them into sets of 125 for shipping direct to the NHS.
More than 77,000 visors will leave the plant by the end of this week, with up to 100,000 being distributed each week, from next week.
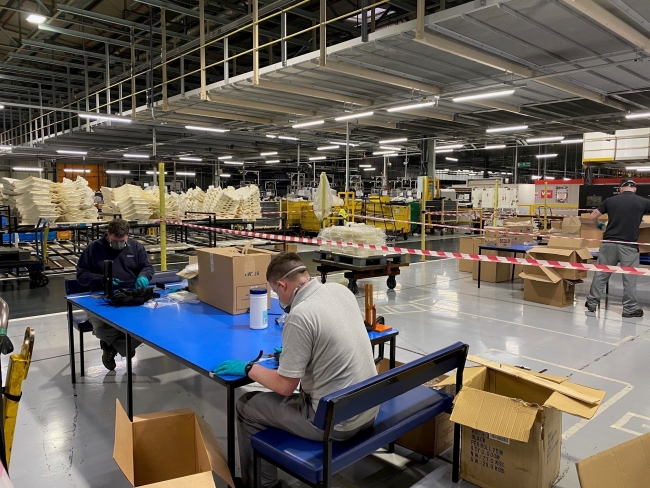
Up to 100,000 face visors per week will be delivered from Nissan’s Sunderland plant to the NHS / Picture: Nissan GB
In the first phase of the project, the team took delivery of hundreds of boxes of visor parts from volunteers from across the country who have been using their 3D printers to make the PPE.
Adam Pennick, Nissan’s production director, said: “It’s great to be able to play our part in helping to provide the NHS with these visors. Our people are experts in the logistics behind an effective supply chain, and we certainly weren’t short of volunteers for this project.”
The project was inspired by four brothers, two of whom, Anthony and Chris Grilli, are engineers based at Nissan’s Technical Centre in Cranfield, Bedfordshire. Production was initially kicked off with the support of crowd funding and used banks of 3D printers at the Grillis’ homes.
Anthony Grilli added: “We had the ability to support the national effort to produce more PPE for frontline health workers and we just had to help. We quickly mobilised to produce parts using our 3D printing capability at home and we’re grateful to everyone that donated through our crowd funding site to help us get this going.”
Nissan has provided funds for an injection moulding tool that increases the number of parts produced, which are now being sourced from companies in Lancashire, Coventry and Gateshead. Injection moulding provides a faster way to produce the plastic parts needed and has ramped up the volume.
The visors are made up of three individual parts: an elastic headband, frame, and see-through visor. These parts are sent to Nissan for packing and distribution in a ready-to-assemble format to an NHS procurement centre. The visors are shipped in this format at the request of the NHS to minimise damage risk during transit, and to ensure the maximum volume can be dispatched at once.
All four of the Grilli brothers are continuing to 3D print face visors at home and are supplying to local care facilities and hospices.