4 minute read
Progress made on £130m Battery Industrialisation Centre
The opening of the £130m UK Battery Industrialisation Centre (UKBIC) has moved a step closer with confirmation that the facility’s module and pack1 suite of specialist battery manufacturing equipment is now operational.
The assembly line is the first of UKBIC’s battery manufacturing equipment to have been installed and commissioned at the publicly funded 18,500 square metre facility in Coventry.
The highly flexible module and pack assembly line enables customers to test and produce low volumes of cylindrical2 and pouch3 cell battery technology. In addition, it has the capacity to produce 50 modules and 2.5 packs over every 8 hour shift.
The line has manual and automatic workstations; and has cylindrical cell pick and place capability, for cell voltage testing and impedance, as well as the ability to place cells into a module in either combination of cell orientation.
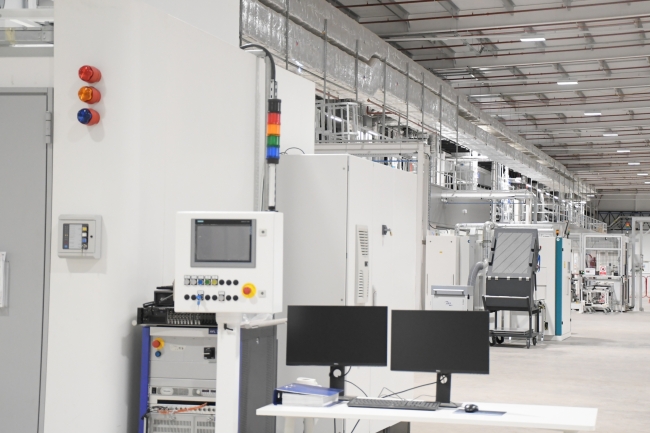
The opening of the £130m UK Battery Industrialisation Centre has moved a step closer with module manufacturing equipment now operational / Picture: UKBIC
Never miss the latest manufacturing news by signing up to our newsletter here
The facility also features a state-of-the-art laser precision specialist welder for welding cells to busbars at industry relevant speeds and accuracy. In addition, the line has pioneering battery leak functionality, which allows leaks to be more easily discovered prior to full scale up, whilst the layout has space reserved to accommodate future customer requirements such as alternative joining technologies and plasma cleaning.
Although UKBIC’s cell making equipment is identical to that of emerging gigafactories now under construction, UKBIC’s module and pack equipment mimics leading cutting-edge processes you would expect to find in high throughput battery assembly plants.
As well as module and pack capability, the battery manufacturing equipment being installed at the facility covers the whole production process from electrode manufacturing, cylindrical and pouch cell assembly, to formation aging and testing, as well as a prototyping competence centre for specialist ultra-low volume builds. The facility provides the missing link between battery technology, which has proved promising at laboratory or prototype scale, and successful mass production.
Ian Whiting, UKBIC’s commercial director, said: “We’re delighted to have our module and pack line up and running. This is the first part of the facility which customers can now use. Our unique, open-access facility allows organisations in the UK to prove whether their promising technologies can be manufactured at the required volume, speed, performance and cost to be commercially successful.
“Clients can bring their own employees in to work and be trained with us on the line. Customers can also integrate processes unique to their own products temporarily to our facility. And we can help them build ‘runner lines’ at UKBIC to enable them to prove higher throughput production in early stages whilst customers build their own production lines.”
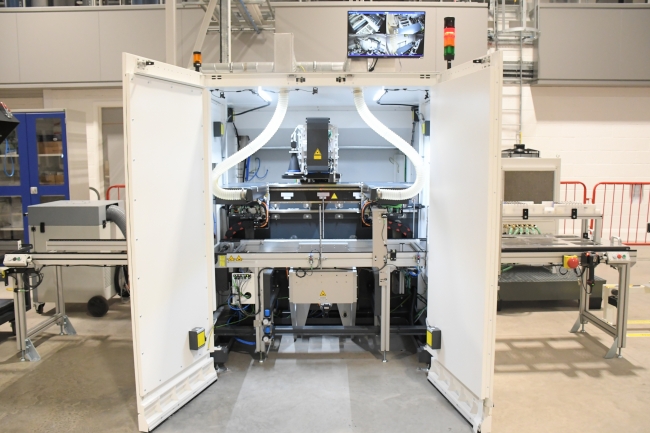
UKBIC is a key part of the Faraday Battery Challenge, a government programme to fast track the development of cost-effective, high-performance, durable, safe, low-weight and recyclable batteries / Picture: UKBIC
Tony Harper, industrial strategy challenge director for the Faraday Battery Challenge at UKRI, added: “The UK Battery Industrialisation Centre has a vital role to play in the development of the battery industry here in the UK. With the module and pack suite now operational this is a major step forward for the UK battery industry that will benefit companies of all sizes. I look forward to seeing the Centre grow and develop over the coming months as this world-class facility brings the full suite of battery manufacturing capabilities on stream.”
Professor David Greenwood, WMG director of industrial engagement and CEO, WMG HVM Catapult, concluded: “We’re delighted to see this critical step along the path to UK battery manufacture is complete. The UK Battery Industrialisation Centre is key to the UK’s battery scale up operations and as a founding partner, WMG are delighted to continue supporting their growth. Electrification is no longer just an issue for cars – WMG are supporting programmes in aerospace, rail, marine and freight as well as smaller vehicles like motorcycles and e-scooters. This new unique facility will allow companies to produce prototypes and limited volume production runs for these and other markets.”
——–
1 Module and pack: Simply put, battery packs are usually made of several modules and those modules are made up of numerous battery cells. The joining and mechanical assembly techniques used are critical to ensuring performance, repeatability and durability. Complexity is added when specialist cooling systems are integrated.
2 Cylindrical cell technology: The cylindrical cell continues to be one of the most widely used packaging types for primary and secondary rechargeable batteries. The advantages are ease of manufacture and good mechanical stability. The tubular cylinder can withstand high internal pressures without deforming.
3 Pouch cell technology: The pouch cell offers a simple, flexible and lightweight solution to battery design. The pouch cell makes the most efficient use of space and achieves a 90 to 95 percent packaging efficiency, the highest among battery packs.